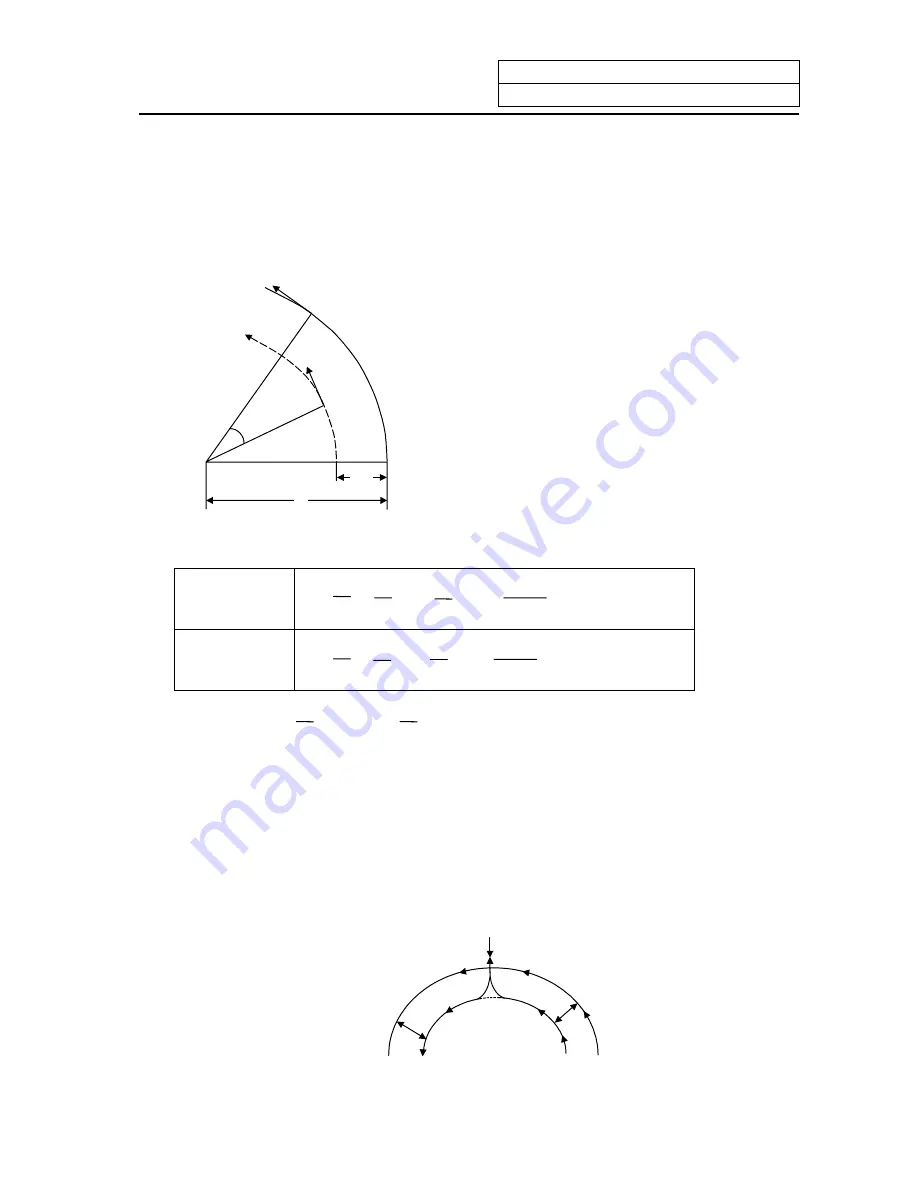
Appendix 3. Circular Cutting Radius Error
IV
-3
Appendix 3 Circular Cutting Radius Error
When circular cutting is performed, an error is caused between the command coordinate and the
tracking coordinate due to the tracking delay in the smoothing circuit and servo system, and the
workpiece ends up with a radius smaller than the commanded value. The method for obtaining this
error (radius error) is shown below.
A : Command coordinate
B : Tracking coordinate
R : Command radius (mm)
∆
R : Radius error (mm)
∆θ
: Angle error (rad)
F : Cutting feed rate (m/min)
A
F
B
∆θ
R
∆
R
F
The radius error
∆
R and angle error
∆θ
are calculated from the following formula.
Exponential
acceleration/
deceleration
∆
R = • ( Ts
2
+ Tp
2
) • ( )
2
(mm)
Linear
acceleration/
deceleration
∆
R = • ( Ts
2
+ Tp
2
) • ( )
2
(mm)
∆θ
= tan
–1
(Ts • ) + tan
–1
(Tp • ) (rad)
Ts: Time constant (s) of specified smoothing circuit
Tp: Position loop time constant
(Note
1)
When
the
∆
R radius error applying with circular cutting does not come within the allowable
value, proceed to reduce the cutting feed rate F, set Ts to a lower value or review the
program.
(Note
2)
In the steady state,
∆
R is constant. However, it is not constant with command start and stop
transitions. Under command start and stop conditions, therefore, the tracking coordinate
should be as shown in the figure below.
Start/stop
Command
Tracking
∆
R
∆
R
1
2
1
2
1
R
F × 10
3
60
1
24
1
2
1
R
F × 10
3
60
F
R
F
R
Содержание EZMotion-NC E60 Series
Страница 1: ......
Страница 15: ...I OPERATION SECTION ...
Страница 361: ...II MACHINE OPERATION MANUAL ...
Страница 399: ...III SETUP ...
Страница 472: ...IV APPENDIXES ...
Страница 510: ......