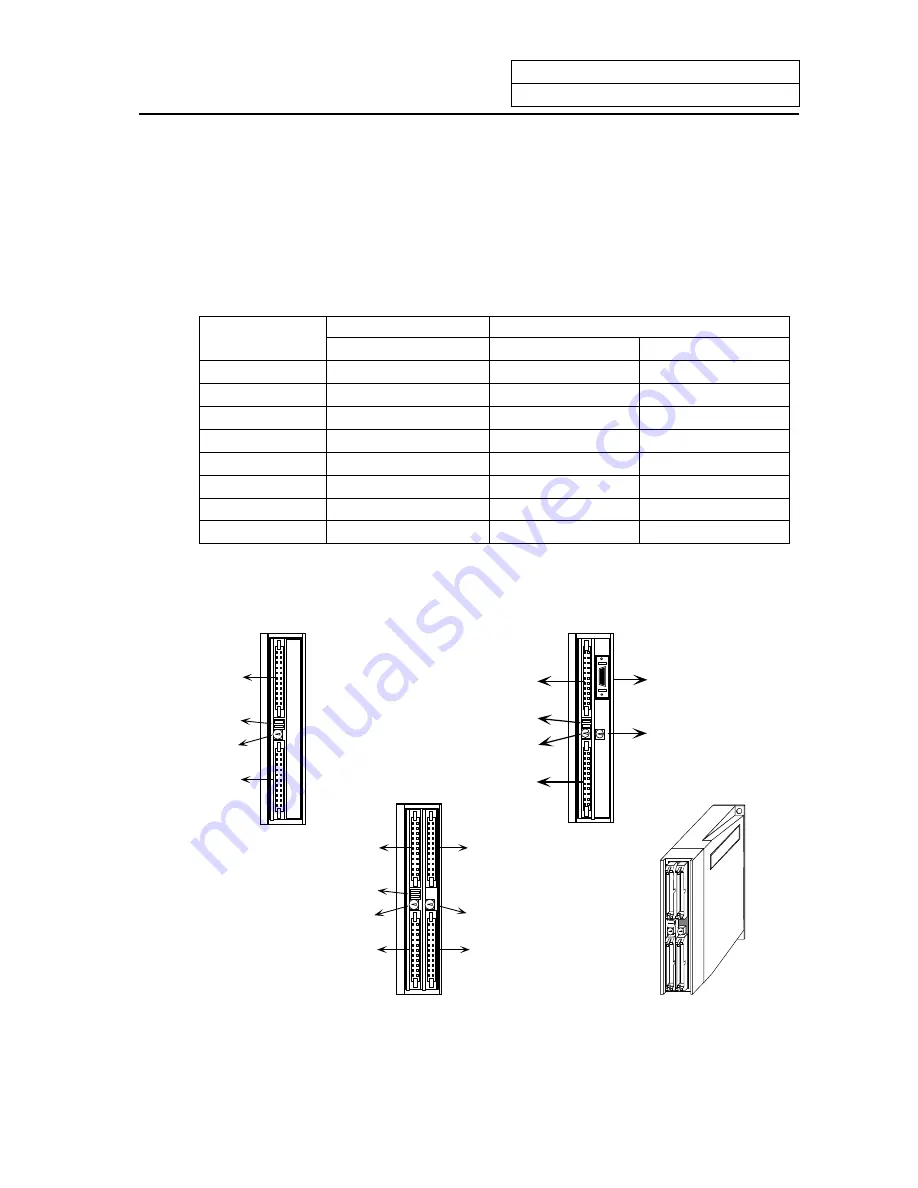
2. Start up and Adjustment Procedure
2.2 Confirmation of Connections
III
-5
2) Remote I/O unit setting switches
There is a lever-type switch (DS1) and rotary switch (CS1) in the center from of the remote I/O
unit.
The
DX10
model has one of each switch, and DX11
/12
/14
has two of each switch.
All DS1 levers must be set and fixed to "OFF: left side". The CS1 setting is "0" to "7", and should
be set while referring to the following table. However, the PCB output (DO) on the right side of
DX11
/12
looking from the front is a 16-point PCB, so take care.
Make sure that the CS1 setting No., is different from other CS1 setting Nos.
Remote I/O unit CS1 setting
Read in device No.
Output device No.
Rotary switch
CS1 No.
PCB at left/right of unit
PCB at left of unit
PCB at right of unit
0 X00~X1F
Y00~Y1F
Y00~Y0F
1 X20~X3F
Y20~Y3F
Y20~Y2F
2 X40~X5F
Y40~Y5F
Y40~Y4F
3 X60~X7F
Y60~Y7F
Y60~Y8F
4 X80~X9F
Y80~Y9F
Y80~Y8F
5 XA0~XBF
YA0~YBF
YA0~YAF
6 XC0~XDF
YC0~YDF YC0~YCF
7 XE0~XFF
YE0~YFF
YE0~YEF
(Note 1)
The rotary switch settings "0 and 1" are used with the base I/O unit, so set the remote I/O unit
connected to the base I/O unit between 2 and 7.
Left input
connector
DIO
specification
switch (DS1)
Rotary
switch (CS1)
Left output
connector
DX10
Front view
Front view
Left input
connector
DIO
specification
switch (DS1)
Rotary
switch (CS1)
Left output
connector
Left input
connector
DIO
specification
switch (DS1)
Rotary
switch (CS1)
Left output
connector
Front view
Outline drawing
DX11
/ DX12
DX14
Right input
connector
Rotary switch
Right output
connector
Analog signal input/
output connector
Rotary switch
Содержание EZMotion-NC E60 Series
Страница 1: ......
Страница 15: ...I OPERATION SECTION ...
Страница 361: ...II MACHINE OPERATION MANUAL ...
Страница 399: ...III SETUP ...
Страница 472: ...IV APPENDIXES ...
Страница 510: ......