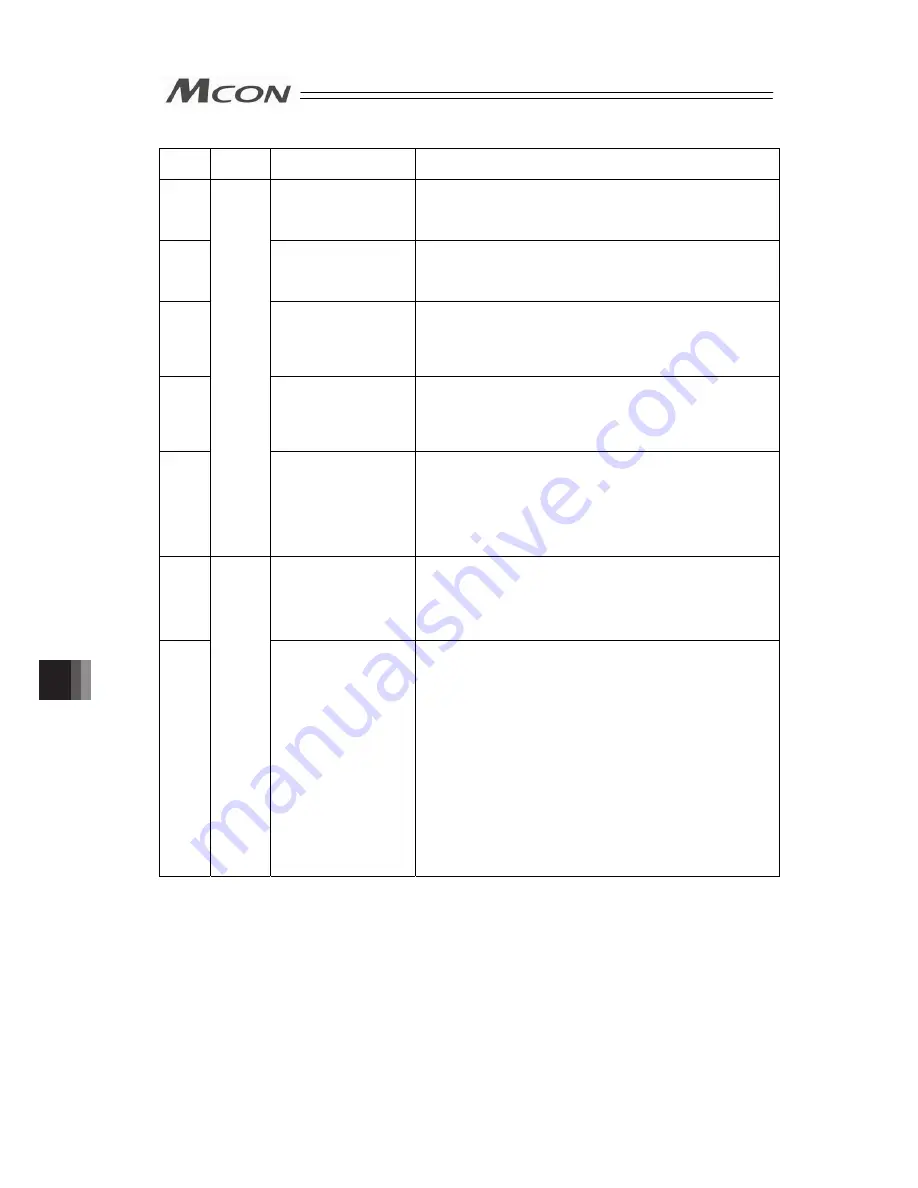
336
Alarm
Code
Alarm
Level
Alarm Name
Cause/Treatment
085
Position No. error during
movement
Cause
: A non-existing (invalid) position number was
specified in the positioner mode.
Treatment : Check the position table again and indicate an
effective position number.
090
Software reset command
in servo-ON condition
Cause
: A software reset command was issued when the
servo was ON.
Treatment : Issue a software reset command after confirming
that the servo is OFF (SV signal is 0).
091
Position No. error in
teaching
Cause
: The position number out of the available range was
selected in the teaching.
Treatment : Set the indication position number to 255 or less in
Positioner 1 or Positioner 2 Mode, or to 64 or less in
Remote I/O Teaching Mode.
092
PWRT signal detection
during movement
Cause
: The current position write signal PWRT was input in
the teaching mode of PIO pattern 1 while the
actuator was jogging.
Treatment : Check that JOG+/- signal is not on and stopped
(MOVE output signal is off) before inputting.
093
Operation
release
PWRT signal detection
in incomplete home
return
Cause
: The current position write signal PWRT was input in
the teaching mode of PIO pattern 1 when home
return was not yet completed.
Treatment : Input the HOME signal first to perform home return,
and then input the PWRT signal after confirming
that the home return has completed (HEND output
signal is ON).
0A0
PIO function assignment
error
Cause
: Data input in Parameter No. 25 PIO Pattern Select
is not appropriate.
Treatment : Select either of PIO Patterns 0, 1, 2, 4 or 5.
Select 6 when in a mode other than Remote I/O
Mode.
0A1
Cold start
Parameter data error
Cause
: The data input range in the parameter area is not
appropriate.
Example 1) This error occurs when the magnitude
relationship is apparently inappropriate
such as when 300mm was incorrectly
input as the value of the soft limit negative
side while the value of the soft limit
positive side was 200.3mm.
Example 2) In rotary axis, when the index mode is
changed to the normal mode and the soft
limit negative side is 0, this error is issued.
Set the soft limit negative side to a value
-0.3mm is added to the outer side of the
effective stroke. [Refer to 8.2 [2] Soft limit
+, Soft limit -]
Treatment : Change the value to the appropriate one.
Chapter 9
Troubleshooting
Содержание MCON-C
Страница 1: ...MCON C CG Controller Instruction Manual Fourth Edition ...
Страница 2: ......
Страница 22: ...12 International Standards Compliances MCON with the following overseas standard RoHS Directive CE Marking UL ...
Страница 48: ...38 Chapter 1 Specifications Check ...
Страница 264: ...254 Note 1 blinking Note 2 single flash Note 3 double flash Timing of LED flashing 3 10 Fieldbus Status LEDs ...
Страница 268: ...258 3 10 Fieldbus Status LEDs ...
Страница 274: ...264 Chapter 4 Vibration Suppress Control Function ...
Страница 278: ...268 Chapter 5 Collision Detection Feature ...
Страница 284: ...274 Chapter 6 Power saving Function ...
Страница 292: ...282 Chapter 7 Absolute Reset and Absolute Battery ...
Страница 358: ...348 Chapter 9 Troubleshooting ...
Страница 368: ...358 4 TP adapter and accessories 1 TP adapter external dimensions RCB LB TGS Chapter 10 Appendix ...
Страница 474: ...Chapter 10 Appendix 464 ...
Страница 478: ......
Страница 479: ......