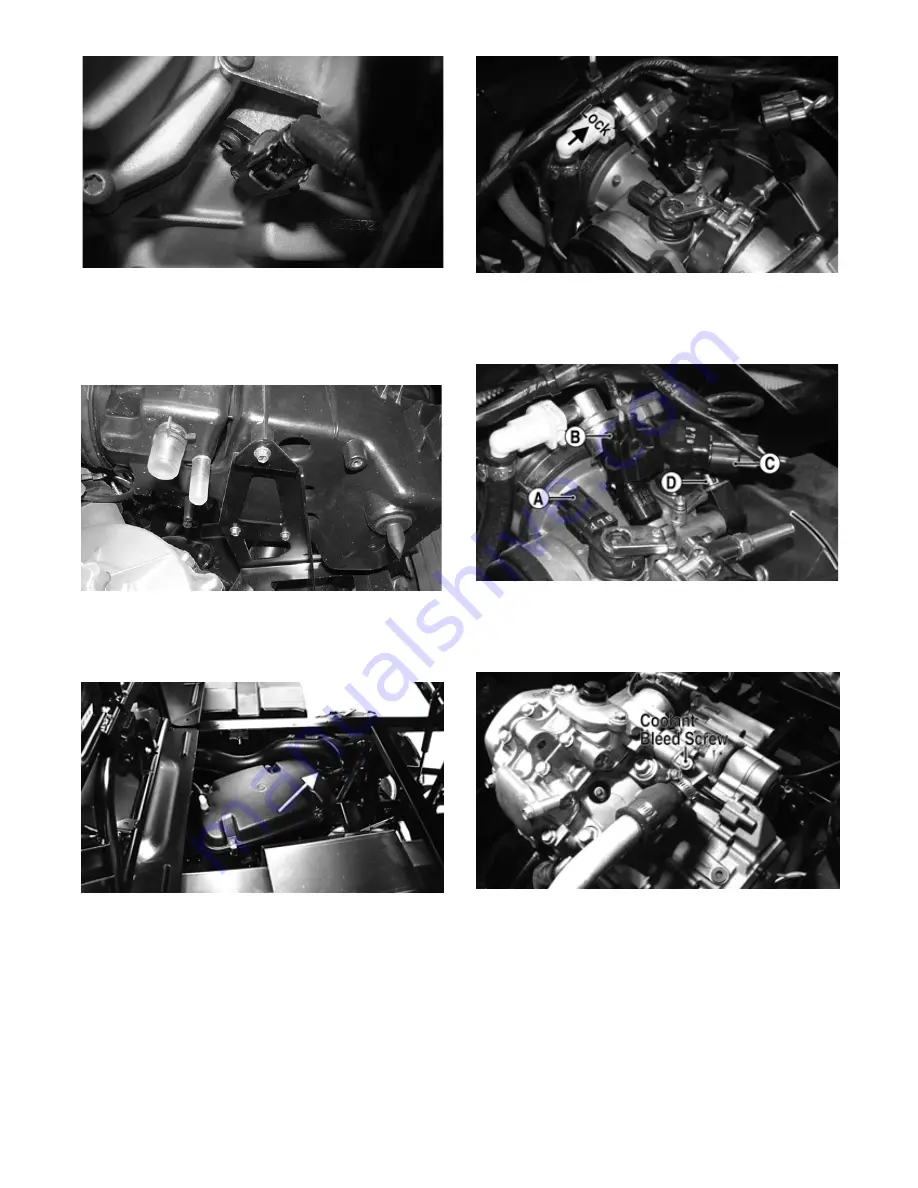
48
HDX359
15. Install the throttle body into the intake manifold boot
and secure with the clamp. Tighten to 30 in.-lb.
16. Install the air filter assembly and secure to the frame
with the cap screws; then secure the intake boot with
the clamp and tighten securely.
HDX287
17. Connect the IAT sensor connector to the IAT sensor
and the crankcase breather tube to the crankcase;
then install the air filter intake tube and secure with a
clamp and sheet metal screw.
HDX031A
18. Connect the gasline hose to the throttle body making
sure the gasline hose connector fully engages and
locks onto the fuel rail.
HDX138B
19. Connect the MAP sensor connector (A), fuel injector
connector (B), ISC connector (C), and TPS connec-
tor (D); then install new nylon ties as noted during
removing.
HDX136A
20. Pour the recommended amount of oil and coolant
into the engine and radiator; then loosen the coolant
bleed screw to allow trapped air to escape. When
clear coolant flows, tighten the bleed screw.
HDX158B
21. Connect the positive battery cable to the battery first;
then connect the negative battery cable to the battery.
22. Install the center skid plate, center floorboard, sec-
ond row footrest, and seat base; then install the seat
back and seat.
23. Start the engine and check for leaks allowing to
warm up for several minutes; then shut the engine off
and check engine oil and coolant levels.
Содержание HDX CREW 2017
Страница 1: ...2017 S SERVICE ERVICE MANUAL ANUAL www arcticcat com...
Страница 151: ...150 NOTES...