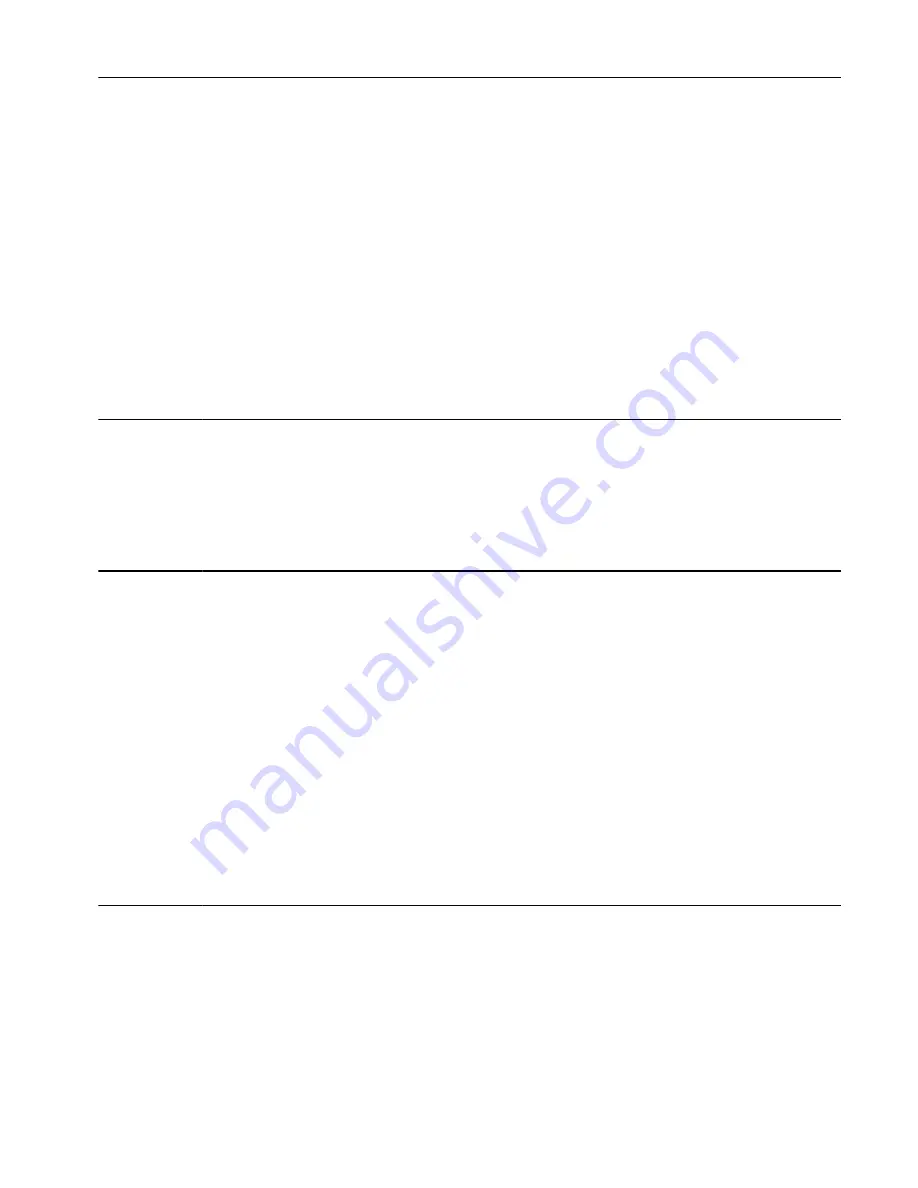
Reaction:
The NC switches to follow-up mode.
NC Start disable in this channel.
Interface signals are set.
Alarm display.
NC Stop on alarm.
Remedy:
Please inform the authorized personnel/service department.
Check the interface signals DB380x DBX2.1 (Servo enable), DB380x DBX4001.7 (Pulse enable), check the drive signals
DB390x DBX4001.7 (Pulses enabled), DB390x DBX4001.5 (Drive ready) for example with the PLC status display in the
DIAGNOSTICS operating area. Check the encoder selection (for axes) as well as other signals enabling motion according
to the drive type used.
When the terminal enables of the drive have failed, trace back the wiring or hardware function (for example relay function)
or proceed as stated in the relevant drive documentation.
With SAFETY: With active actual-value linkage, output of the error message on the slave axis can be prevented by
increasing MD36060 $MA_STANDSTILL_VELO_TOL (default value is 5 mm).
Programm
continuation:
Clear alarm with the Delete key or NC START.
21613
Axis %1 measuring system changing
Parameters:
%1 = Axis name, spindle number
Explanation:
The measuring system for this axis is changing.
Reaction:
Alarm display.
Remedy:
-
Programm
continuation:
Alarm display showing cause of alarm disappears. No further operator action necessary.
21614
[Channel %1: ] Axis %2 hardware limit switch %3
Parameters:
%1 = Channel number
%2 = Axis name, spindle number
%3 = String (+, - or +/-)
Explanation:
The signal DB380x DBX1000.1 und .0 (Hardware limit switch plus/minus) has been set at the NC/PLC interface.
Reaction:
NC Start disable in this channel.
Alarm display.
Remedy:
Please inform the authorized personnel/service department.
1. With axes that have already been referenced, the software limit switch 1 or 2 should respond before the hardware limit
switch is reached. Check MD36110 $MA_POS_LIMIT_PLUS, MD36100 $MA_POS_LIMIT_MINUS, MD36130
$MA_POS_LIMIT_PLUS2 and MD36120 $MA_POS_LIMIT_MINUS2 and the NC/PLC interface signal for the selection
DB380x DBX1000.3 / 1000.2 (1st/2nd software limit switch plus/minus) and correct, if necessary (PLC user program).
2. If the axis has not yet been referenced, it is possible to depart from the hardware limit switch in the opposite direction
in JOG mode.
3. Check the PLC user program and the connection from the switch to the PLC input module, provided the axis has not
reached the hardware limit switch at all.
Programm
continuation:
Clear alarm with the RESET key. Restart part program
21615
[Channel %1: ] Axis %2 taken from traverse mode to follow-up mode
Parameters:
%1 = Channel number
%2 = Axis name, spindle number
Explanation:
This axis has been taken from traverse mode and put into "Follow-up" mode, for instance because the pulse enable for
the drive has been reset.
Reaction:
NC Start disable in this channel.
Interface signals are set.
Alarm display.
NC Stop on alarm.
SINUMERIK 808D ADVANCED alarms
5.2 NCK alarms
Diagnostics Manual
Diagnostics Manual, 06/2015, 6FC5398-6DP10-0BA2
319