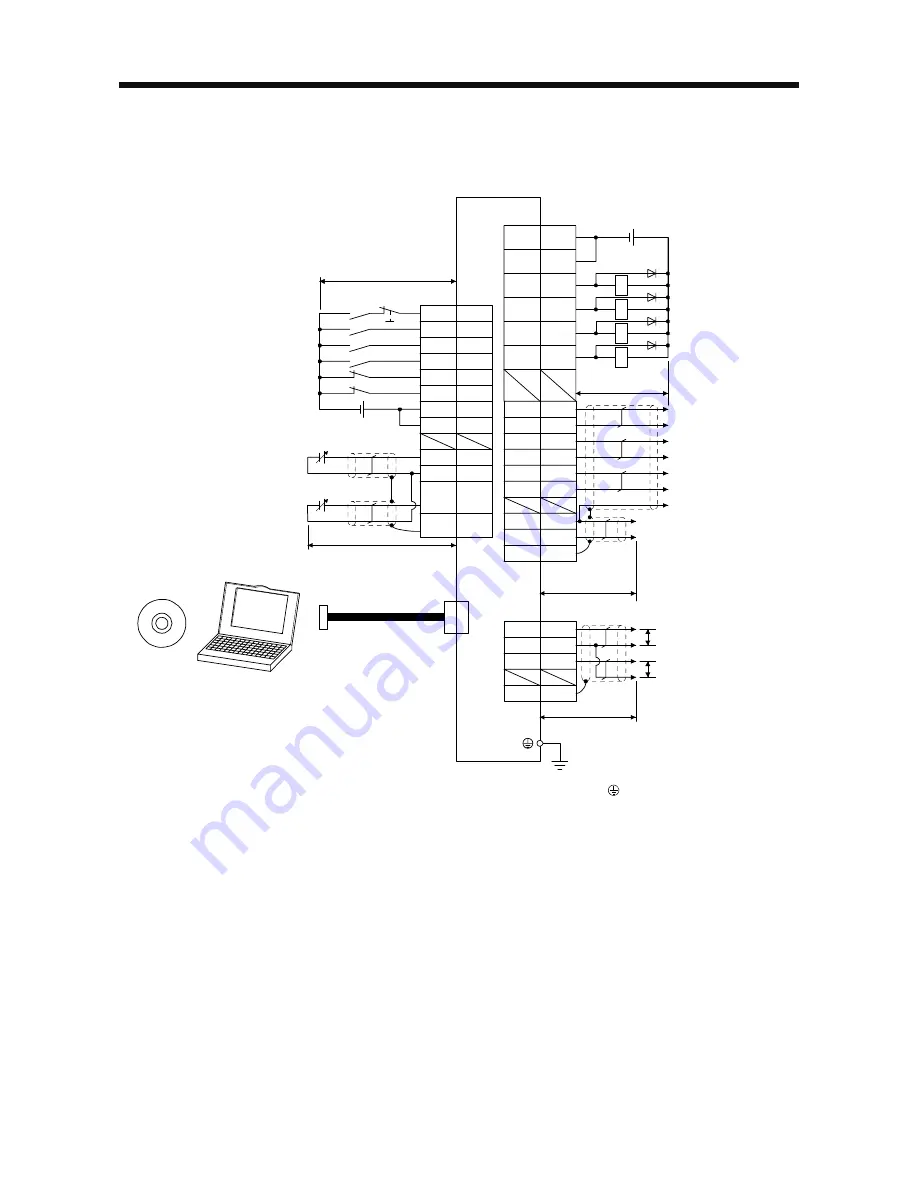
3. SIGNALS AND WIRING
3 - 11
3.2.2 Speed control mode
(1) For sink I/O interface
(Note 11)
Power supply
(Note 1)
(Note 2)
(Note 7)
CN1
(Note 7)
CN1
Servo amplifier
(Note 7)
CN1
47
DOCOM
46
DOCOM
48
ALM
23
ZSP
24
SA
49
RD
4
LA
5
LAR
6
LB
7
LBR
34
LG
33
OP
SD
2 m or less
8
LZ
9
LZR
20
DICOM
21
DICOM
10 m or less
2
2 m or less
28
27
VC
SD
TLA
LG
+
CN3
(Note 10) Analog speed command
±10 V/rated speed
(Note 8) Analog torque limit
+10 V/maximum torque
(Note 9)
MR Configurator2
RA1
RA2
RA3
RA4
24 V DC (Note 4)
24 V DC (Note 4)
42
15
19
41
43
44
EM2
SON
ST1
ST2
LSP
LSN
Forward rotation start
Reverse rotation start
Encoder Z-phase pulse
(open collector)
Speed reached
Ready
10 m or less
2 m or less
26
MO1
30
LG
29
MO2
± 10 V DC
± 10 V DC
SD
-10 V to +10 V
0 V to +10 V
Forced stop 2
Servo-on
Forward rotation
stroke end
Reverse rotation
stroke end
(Note 3, 5)
(Note 5)
Plate
Plate
Plate
USB cable (option)
Personal
computer
Analog monitor 1
Analog monitor 2
Malfunction (Note 6)
Zero speed detection
Encoder A-phase pulse
(differential line driver)
Encoder Z-phase pulse
(differential line driver)
Encoder B-phase pulse
(differential line driver)
Control common
Note 1. To prevent an electric shock, always connect the protective earth (PE) terminal (marked ) of the servo amplifier to the
protective earth (PE) of the cabinet.
2. Connect the diode in the correct direction. If it is connected reversely, the servo amplifier will malfunction and will not output
signals, disabling EM2 (Forced stop 2) and other protective circuits.
3. The forced stop switch (normally closed contact) must be installed.
4. Supply 24 V DC ± 10% to interfaces from outside. The total current capacity is up to 300 mA. 300 mA is the value applicable
when all I/O signals are used. The current capacity can be decreased by reducing the number of I/O points. Refer to section
3.9.2 (1) that gives the current value necessary for the interface. The illustration of the 24 V DC power supply is divided
between input signal and output signal for convenience. However, they can be configured by one.
5. When starting operation, always turn on EM2 (Forced stop 2), LSP (Forward rotation stroke end) and LSN (Reverse rotation
stroke end) (normally closed contact).
6. ALM (Malfunction) turns on in normal alarm-free condition (normally closed contact).
7. The pins with the same signal name are connected in the servo amplifier.
8. TLA will be available when TL (External torque limit selection) is enabled with [Pr. PD03], [Pr. PD11], [Pr. PD13], [Pr. PD17],
and [Pr. PD19]. (Refer to section 3.6.1 (5).)
9. Use SW1DNC-MRC2-E. (Refer to section 11.4.)
10. Use an external power supply when inputting a negative voltage.
11. Configure a circuit to turn off EM2 when the power is turned off to prevent an unexpected restart of the servo amplifier.
12. Plus and minus of the power of source interface are the opposite of those of sink interface.
Summary of Contents for MELSERVO-JE MR-JE-100A
Page 23: ...1 FUNCTIONS AND CONFIGURATION 1 12 MEMO ...
Page 29: ...2 INSTALLATION 2 6 MEMO ...
Page 91: ...3 SIGNALS AND WIRING 3 62 MEMO ...
Page 171: ...5 PARAMETERS 5 44 MEMO ...
Page 195: ...6 NORMAL GAIN ADJUSTMENT 6 24 MEMO ...
Page 221: ...7 SPECIAL ADJUSTMENT FUNCTIONS 7 26 MEMO ...
Page 249: ...8 TROUBLESHOOTING 8 28 MEMO ...
Page 255: ...9 DIMENSIONS 9 6 MEMO ...
Page 263: ...10 CHARACTERISTICS 10 8 MEMO ...
Page 293: ...11 OPTIONS AND PERIPHERAL EQUIPMENT 11 30 MEMO ...