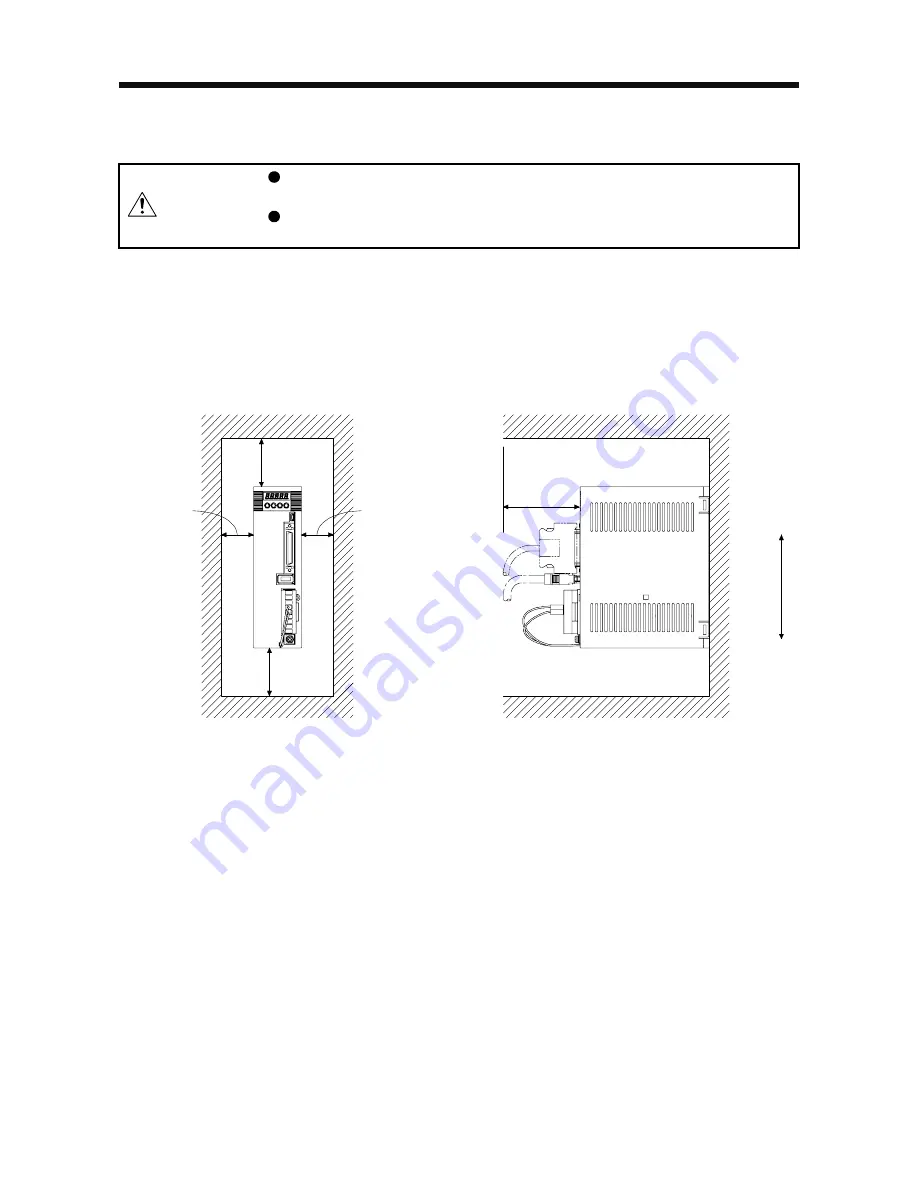
2. INSTALLATION
2 - 2
2.1 Installation direction and clearances
CAUTION
The equipment must be installed in the specified direction. Otherwise, it may
cause a malfunction.
Leave specified clearances between the servo amplifier and the cabinet walls or
other equipment. Otherwise, it may cause a malfunction.
MR-JE-40A to MR-JE-100A have a regenerative resistor on their back face. The regenerative resistor
generates heat of 100
˚
C higher than the ambient temperature. Please fully consider heat dissipation,
installation position, etc. when mounting it.
(1) Installation clearances of the servo amplifier
(a) Installation of one servo amplifier
40 mm
or more
10 mm
or more
10 mm
or more
40 mm
or more
Servo
amplifier
Cabinet
Cabinet
Wiring allowance
80 mm
or more
Top
Bottom
Summary of Contents for MELSERVO-JE MR-JE-100A
Page 23: ...1 FUNCTIONS AND CONFIGURATION 1 12 MEMO ...
Page 29: ...2 INSTALLATION 2 6 MEMO ...
Page 91: ...3 SIGNALS AND WIRING 3 62 MEMO ...
Page 171: ...5 PARAMETERS 5 44 MEMO ...
Page 195: ...6 NORMAL GAIN ADJUSTMENT 6 24 MEMO ...
Page 221: ...7 SPECIAL ADJUSTMENT FUNCTIONS 7 26 MEMO ...
Page 249: ...8 TROUBLESHOOTING 8 28 MEMO ...
Page 255: ...9 DIMENSIONS 9 6 MEMO ...
Page 263: ...10 CHARACTERISTICS 10 8 MEMO ...
Page 293: ...11 OPTIONS AND PERIPHERAL EQUIPMENT 11 30 MEMO ...