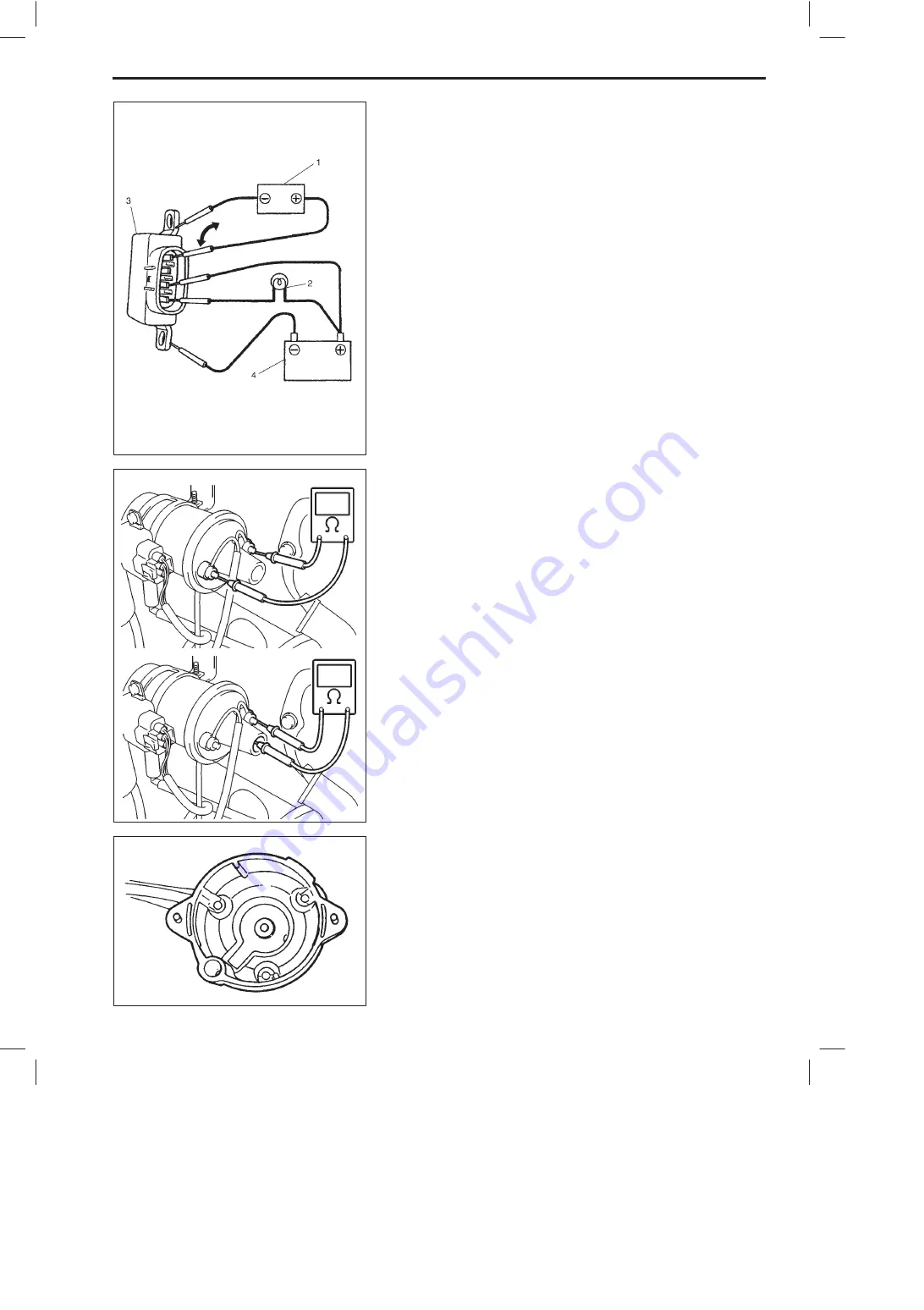
3) Arrange 3 new batteries in series (1) (check total voltage is
above 4.7V)
4) Connect light bulb (2) between “c” terminal of igniter (3) and bat-
tery (4) positive (+) terminal, then connect battery negative (–)
terminal to igniter body.
Also connect battery positive (+) terminal, and “b” terminal/ of
igniter.
Check that the light bulb does not illuminate.
5) Connect negative (–) terminal of batteries and igniter body.
Check that the light bulb illuminate when positive (+) terminal of
batteries is connected to “a” terminal of igniter.
If inspection result is not satisfactory, replace igniter.
6) Install igniter.
IGNITION COIL
1) Pull out high-tension cord by gripping its cap.
2) Disconnect ignition coil coupler.
3) Measure primary and secondary coil resistances.
Ignition coil resistance (at 20
_
C/68
_
F)
Primary
: 1.33 – 1.63
(A)
. .
Secondary: 10.7 – 14.5 k
(B)
.
(A)
(B)
DISTRIBUTOR
INSPECTION
Distributor Cap and Rotor
Check cap and rotor for crack and their terminals for corrosion and
wear. Replace as necessary.
IGNITION SYSTEM
6F-9