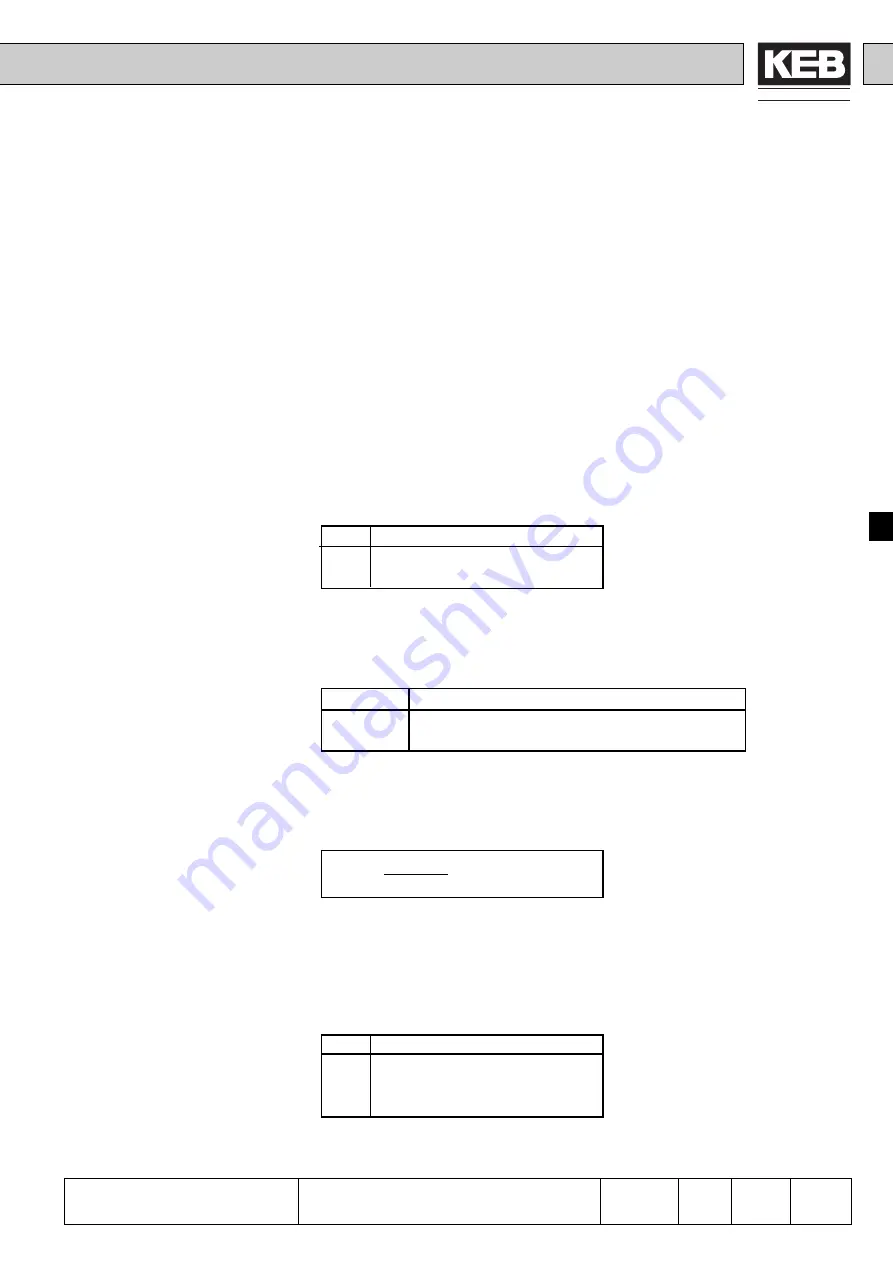
3
ANTRIEBSTECHNIK
6
10
3
KEB COMBIVERT F4-F
Name: Basis
15.03.99
6
Section
Page
Date
©
KEB Antriebstechnik, 1999
All Rights reserved
Chapter
Functional Description
Synchronous Control
6.10 Synchronous
Control
6.10.1 Activating
Synchronous
Control
The synchronous control can be activated/deactivated by way of a programmable
input (see Chapter „Digital Inputs“). When using bus or keyboard the synchronous
control can be activated/deactivated with parameter Sn.0.
Sn.0
Function
0
Synchronous control off
1
Synchronous control on
Writing on this parameter sets the angular difference to zero.
The synchronous module realizes a multi-motor synchronous control. Several motors
can be operated
•
speed synchronous
•
angular synchronous
to a master drive (control drive). The speed relations are individually adjustable. The
control drive must not be controlled. The synchronous module can only be activated
when the inverter is fitted with a second incremental encoder input.
Is synchronous operation
possible?
One look onto parameter In.57 answers this question. The following display indications
mean:
•
„0“ synchronous operation possible
•
„4“ not possible
•
„7“ synchronous operation possible when the interface is switched to
input (dr.39 = „1“).
6.10.2 KP Synchronous
Control (Sn.1)
With Sn.1 it is selected between speed and angular syncrhonous control. Furthermore,
the proportional part of the synchronous control is adjusted.
Sn.1
Function
0
Speed synchronous control
1...65535
Angular synchronous control with proportional part
The gear ratio between master speed and slave speed is adjusted in Sn.2. The ratio is
sign-affected; i.e. negative sign means opposite rotation direction.
6.10.3 Gear Ratio
Master/Slave
(Sn.2)
Slave
Master
Sn.2 =
= -20,000...20,000
6.10.4 Angular
Correction
(Sn.5...7)
Three parameters exist for the angular adjustment between master and slave. The
intended
position correction angle is entered in Sn.6
(0…360°), intended
complete
revolutions are entered in Sn.7
(0…65535). The real correction can then be triggered
by way of a programmable input in the desired direction (see Chapter „Digital Inputs“).
The second possibility to start the correction offers Sn.5:
Sn.5
Function
0
No correction
1
Correction in positive direction
2
Correction in negative direction
Synchronous control (Sn.0)