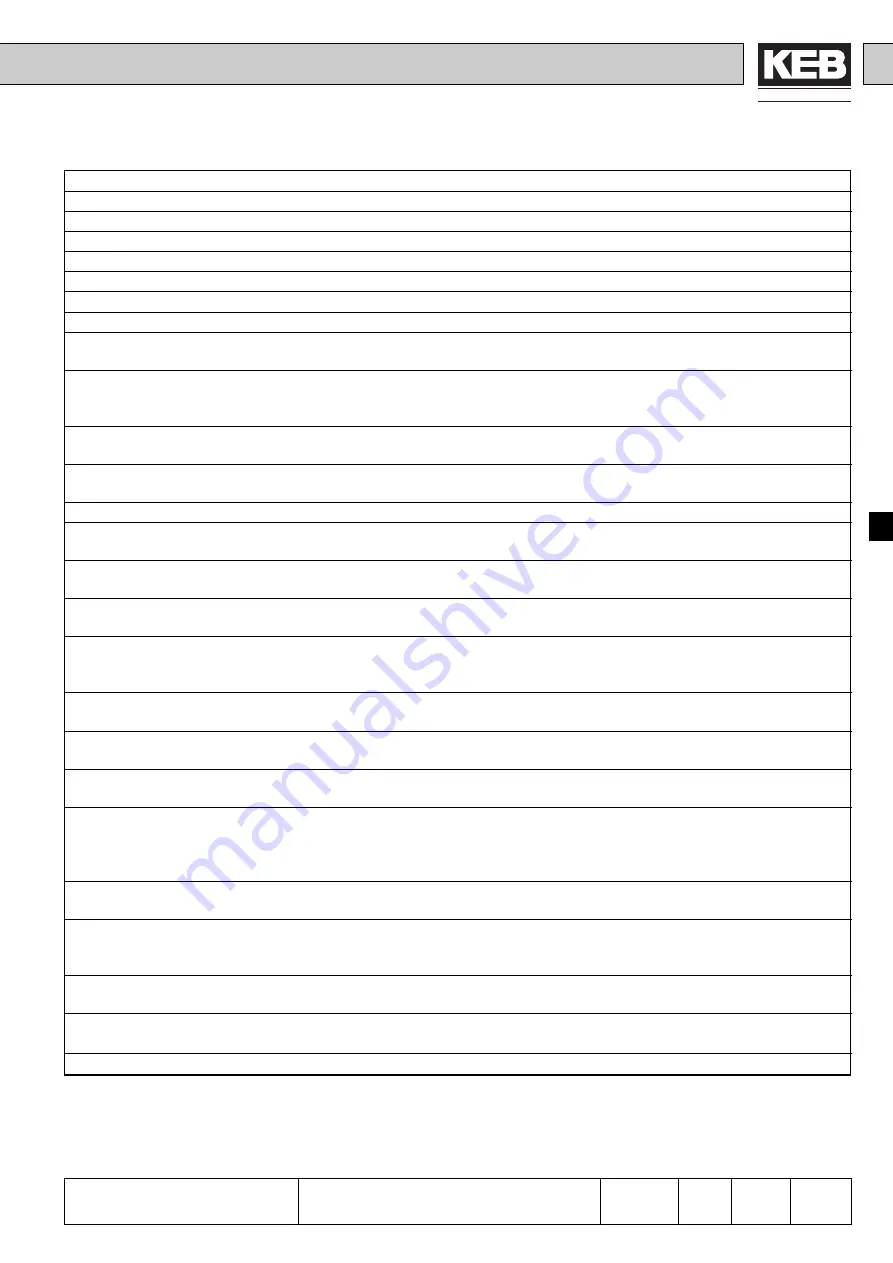
11
ANTRIEBSTECHNIK
6
3
11
KEB COMBIVERT F4-F
Name: Basis
02.03.99
6
Section
Page
Date
©
KEB Antriebstechnik, 1999
All Rights reserved
Chapter
Functional Description
Digital In- and Outputs
10
*1
Speed controller in the limit (torque limit CS.06...CS.09 reached)
11
*1
Optional controller in the limit
12
*2
Drive accelerates
13
*2
Drive decelerates
14
*2
Drive operates with constant speed
15
*2
Drive operates uneven 0 with constant speed
16
*3
Clockwise rotation (forward); not at noP, LS, abnormal stopping or fault
17
*3
Counter clockwise rotation (reverse); not at noP, LS, abnormal stopping or fault
18
Actual speed (ru.1) > speed level 1...4 adjusted in LE.4...LE.7. Speed level 1 applies to do.1 and do.5,
speed level 2 applies to do.2 and do.6...and so forth.; LE.37 defines the speed hysteresis.
19
Apparent current (ru.9) > apparent current level 1...4 adjusted in LE.12...LE.15. Apparent current level 1
applies to do.1 and do.6, apparent current level 2 applies to do.2 and do.6 ...and so forth.; LE.38 defines the
current hysteresis.
20
*1
Torque (ru.2) > torque level 1...4 adjusted in LE.20...LE.23. Torque level 1 applies to do.1 and do.5; torque
level 2 applies to do.2 and do.6 ...and so forth.; LE.40 defines the hysteresis.
21
Angular displacement (ru.27) > angular level 1...4 adjusted in LE.28...LE.31. Angular level 1 applies to do.1
and do.5, angular level 2 applies to do.2 and do.6 ...and so forth.; LE.39 defines the angular hysteresis.
22
Reference point run completed
23
Load (ru.7) > than the load level 1...4 adjusted in LE.8...LE.11. Load level1 applies to do.1 and do.5; load
level 2 applies to do.2 and do.6 ...and so forth.
24
Overload-signal 80%
! ru.24 is an overload counter that counts in steps of 1%. At 100% the inverter switches
off with E.OL. At 80% the output is set.
25
Overload-signal 40%
! ru.24 is an overload counter that counts in steps of 1%. At 100% the inverter switches
off with E.OL. At 40% the output is set.
26
Overtemperature-signal
is set, when the heat sink temperature exceeds 70...90°C depending on the
power stage. In case the temperature does not drop below the tripping level it is being switched off with error
E.OH 10 s after setting the output.
27
Setpoint speed (ru.4) > than the speed level 1...4 adjusted in LE.4...LE.7. Speed level 1 applies to do.1 and
do.5, speed level 2 applies to do.2 and do.6...and so forth.; LE.37 defines the speed hysteresis.
28
*1
Speed controller deviation (ru.28) > than the speed level 1...4 adjusted in LE.4...LE.7. Speed level 1 applies
to do.1 and do.5, speed level 2 applies to do.2 und do.6...usw.; LE.37 defines the speed hysteresis.
29
Constant current exceeded at low speed (warning); The OL2 function is dependent of the heat sink teperature.
The prewarning is set if the the load is so high that E.OL2 is triggered at max. heat sink temperature.
30
Target window reached
; is set, when after giving a positioning command the actual position equals the
setpoint position. The tolerance defined by the target window (Pd.12). Only available in positioning operation
(Sn.0 = 0; Pc.0 = 1). Attenion! If a new positioning command is started the signal remains set during the
brake release time.
31
Actual position > than the positioning level 1...4 adjusted in LE.50...LE.61. Positioning level 1 applies to do.1
and do.5; positioning level 2 applies to do.2 and do.6 ...and so forth.; LE.48 defines the hysteresis.
32
Brake control
; by selecting this switching condition the function „brake handling“ (see chapter 6.8) is activated.
Depending on the operating state of the inverter and the brake parameters LE.66...LE.68 a signal is generated
for the brake control.
33
Fault signal
; Inverter has disabled the modulation after an error or fast stop and automatic restart is not
activated for the respective error (Pn.0 or Pn.1).
34
Temperature control for water-cooled inverter (see chapter 6.8.6 Temperature Control)
Attention! This function should only be used via transistor output with the respective following electronics.
35
Coolant warning for water cooled inverter (see chapter 6.8.6 Temperature Control)
*1
Function available only for controlled operation.
*2
This function refers to the setpoint ramps only, i.e. if the ramp generator has not been passed (e.g. in case of fast setpoint setting, activated
synchronous controller or positioning controller) then the function is not available. If the drive cannot follow the adjusted ramps,then the
output switches in dependence on the setpoint value and not the actual value.
*3
As *2 but not available in the positioning module.