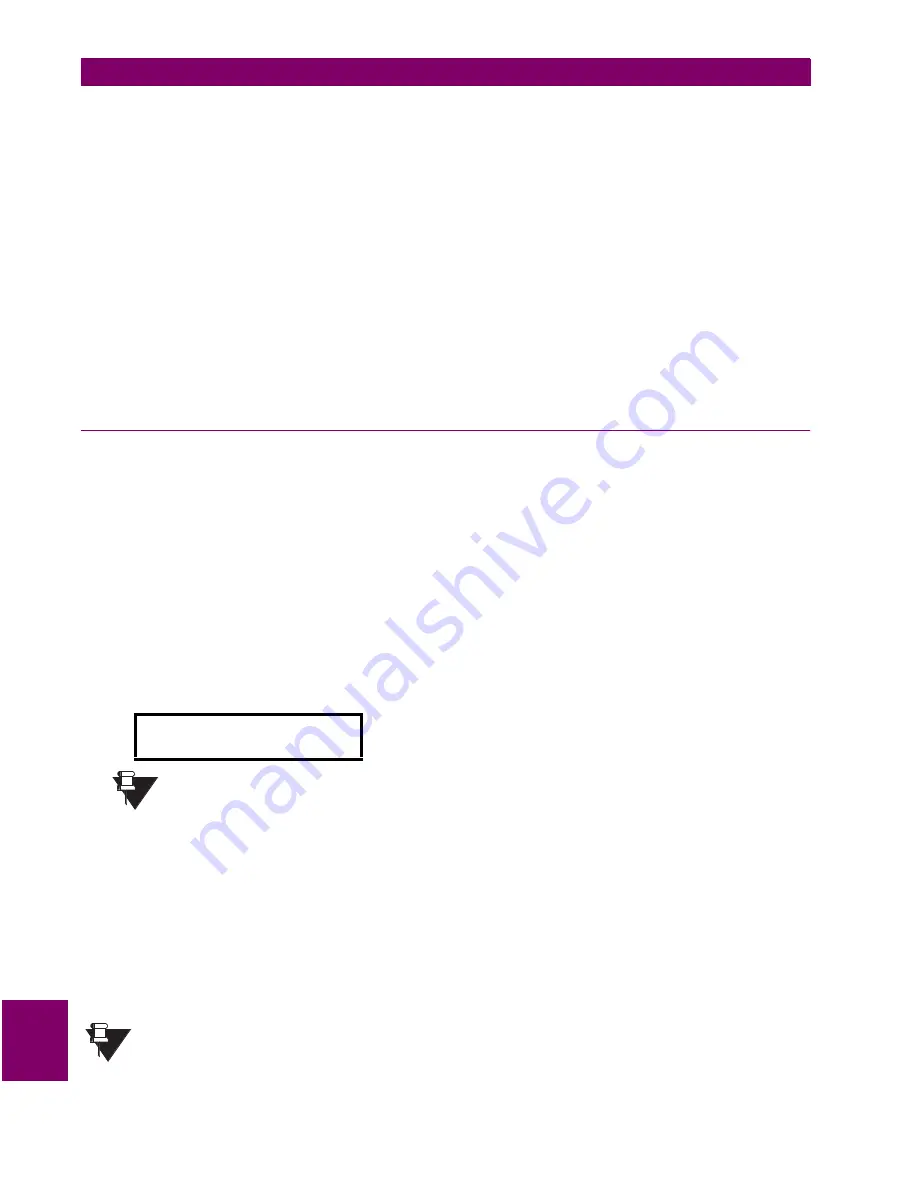
10-20
745 Transformer Management Relay
GE Power Management
10.6 PROTECTION SCHEMES
10 COMMISSIONING
10
k) TARGET, OUTPUT CONTACT, & DISPLAY OPERATION
Verify the correct operation of all targets and output contacts and display messages during the above Percent
Differential tests.
l) BLOCKING FROM LOGIC INPUTS
Each element can be programmed to be blocked by a logic input, virtual input, virtual output, output relay oper-
ation, or self-test relay operation. This procedure verifies that the differential element is blockable by Logic
Input 1.
1.
Select Logic Input 1 as shown:
SETPOINTS/S4 ELEMENTS/DIFFERENTIAL/PERCENT DIFFERENTIAL/PERCENT DIFFERENTIAL BLOCK:
Logc Inpt 1
2.
Apply current to operate the differential element then assert Logic Input 1. Verify that the element has reset
and that all targets can be reset.
3.
With Logic Input 1 asserted, remove the current and reapply. Verify that the element did not operate.
10.6.3 INSTANTANEOUS DIFFERENTIAL PROTECTION
Settings for this element are under the setpoints group:
SETPOINTS/S4 ELEMENTS/INST DIFFERENTIAL/...
All other protective elements must be disabled to ensure that trip relay(s) and auxiliary relays are operated by
element under test. Monitor the appropriate contact per intended settings of the FlexLogic.
a) MINIMUM PICKUP
1.
The operating level of the A-phase element is measured by applying an AC current to terminals H1 and
G1. Monitor the appropriate trip and auxiliary contact(s) as the current is increased from 0 A. Due to the
auto-configuration feature, it may be easier to read the actual differential current on the relay rather com-
puting it. Compare the value of the differential current at which operation is detected against the setpoint:
SETPOINTS/ S4 ELEMENTS/INST DIFFERENTIAL/INST DIFFERENTIAL PICKUP
2.
Check that the TRIP and MESSAGE indicators are flashing and the following trip message is displayed:
The message may show operated instead of latched if the target is set to Self-Reset.
b) OPERATING TIME
1.
To measure the basic operating time of the instantaneous differential elements, connect an AC current sig-
nal to terminals H1 and G1 through a double-pole, single-throw switch. The second pole of the switch
starts a timer circuit that will be stopped by the operation of the relay trip contact. Refer to Figure 10–5:
TIMER TEST CIRCUIT on page 10–16.
2.
Close the switch and set the current level to 2 times the pickup value measured earlier. Re-open the switch
and reset all targets on the relay. Ensure that the timer circuit functions correctly.
3.
Close the switch and record operating time of relay.
All the differential currents are calculated using the same principal used in Section 10.5.4:
TRANSFORMER-TYPE SELECTION on page 10–9. The differential current derivation is
affected by phase shift compensation and zero sequence removal.
yy
LATCHED:
∅
A (BC)
yy
Inst Differential
NOTE
NOTE
Summary of Contents for 745 TRANSFORMER MANAGEMENT RELAY
Page 30: ...2 8 745 Transformer Management Relay GE Power Management 2 3 SECURITY 2 GETTING STARTED 2 ...
Page 210: ...7 36 745 Transformer Management Relay GE Power Management 7 2 BLOCK DIAGRAMS 7 SCHEME LOGIC 7 ...
Page 322: ...9 12 745 Transformer Management Relay GE Power Management 9 3 USING 745PC 9 745 PC SOFTWARE 9 ...
Page 396: ...A 4 745 Transformer Management Relay GE Power Management A 1 FIGURES AND TABLES APPENDIXA A ...
Page 400: ...C 2 745 Transformer Management Relay GE Power Management C 1 WARRANTY INFORMATION APPENDIXC C ...
Page 406: ...vi 745 Transformer Management Relay GE Power Management ...
Page 407: ...GE Power Management 745 Transformer Management Relay NOTES ...