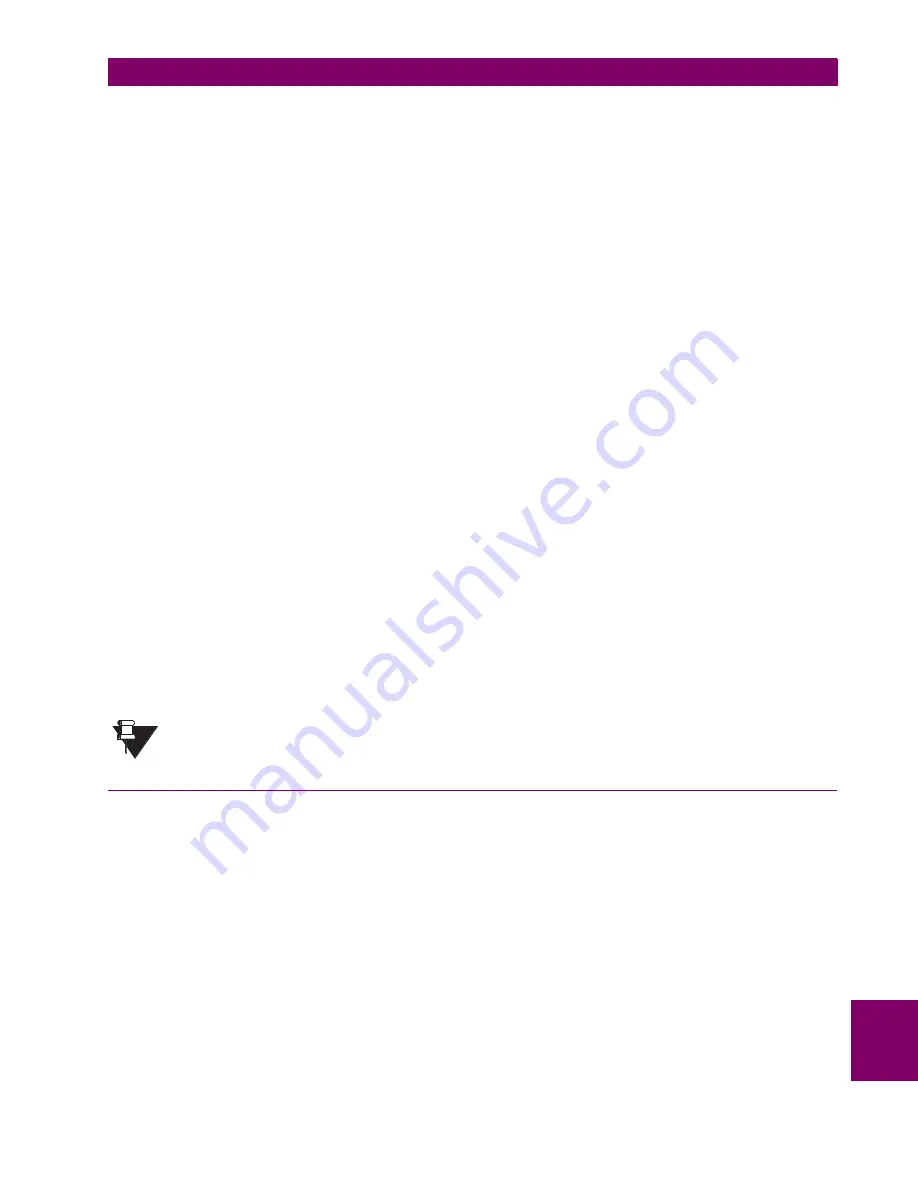
GE Power Management
745 Transformer Management Relay
10-31
10 COMMISSIONING
10.6 PROTECTION SCHEMES
10
c) OPERATING TIME
Select 3 or 4 delay times at which the timing is to be measured. With the Interval Timer enabled, set the current
level to the desired value and apply suddenly by closing the double-pole switch. Record the operate time and
compare to the expected value. Repeat for the all the desired values of current.
d) SLOPE
1.
To measure the slope, connect current signals to the relay as shown in Figure 10–10: RESTRICTED
GROUND TEST SETUP on page 10–30.
2.
Inject the
I
1
current such that the ground differential pickup value divided by the
I
1
current is less than the
slope setting. Set
I
2
= 0 A. The element will operate as since the current appears as ground differential.
3.
The slope is calculated from the values of
I
ground differential
and
I
max
as shown below:
I
max
represents the maximum phase current for the winding being measured.
4.
As
I
2
is increased, the element will reset when the percentage of slope drops below the slope setting.
Slowly increase
I
2
until the element operates again. Calculate the slope at this point.
5.
Decrease the slope setting to 0% then continue to increase the
I
2
current until the element resets. Slowly
increase
I
2
until the element operates again.
6.
The reset level should be 97% of the operate level. When the element resets, the TRIP and message indi-
cators should remain on if the TARGET was selected as latched. Otherwise only the TRIP indicator should
remain on.
e) WINDING 2 OR 3 ELEMENTS
Since the second Restricted Ground Fault element can be set with completely different parameters than the
first element winding, it is necessary to repeat the full set of tests described in this section for each winding.
To test the second element, disable all protection elements except for the W2 (or W3 as appropriate)
Restricted Ground Fault element. Connect the ground current signal to F12 and E12. Repeat all the tests
described for the Winding 1 element in this section.
The blocking from logic input, if enabled, can be tested as described in earlier tests for other
elements.
10.6.14 NEGATIVE SEQUENCE TIME OVERCURRENT
This procedure verifies that the Negative Sequence Time Overcurrent performance matches the in-service set-
tings. Since these elements can have any one of a multitude of timing curves, a table of expected operating
times versus applied current should be prepared prior to testing the elements. The negative-sequence element
measures the derived negative-sequence component of the phase current signals connected to the phase
input CTs. Refer to Section 5.9: TIME OVERCURRENT CURVES on page 5–91 for additional information on
timing curves.
If the relay elements are set for
Linear
reset characteristic when measuring the operating times, ensure that
there is sufficient time between test current injections for the element to reset fully. Otherwise, erroneous timing
measurements will be obtained.
Settings for these elements are found under:
SETPOINTS/S4 ELEMENTS/NEG SEQ OC/W1 NEG SEQ TIME OC/...
a) WINDING #1 ELEMENT
%slope
I
ground differential
I
max
--------------------------------------------
100%
×
=
NOTE
Summary of Contents for 745 TRANSFORMER MANAGEMENT RELAY
Page 30: ...2 8 745 Transformer Management Relay GE Power Management 2 3 SECURITY 2 GETTING STARTED 2 ...
Page 210: ...7 36 745 Transformer Management Relay GE Power Management 7 2 BLOCK DIAGRAMS 7 SCHEME LOGIC 7 ...
Page 322: ...9 12 745 Transformer Management Relay GE Power Management 9 3 USING 745PC 9 745 PC SOFTWARE 9 ...
Page 396: ...A 4 745 Transformer Management Relay GE Power Management A 1 FIGURES AND TABLES APPENDIXA A ...
Page 400: ...C 2 745 Transformer Management Relay GE Power Management C 1 WARRANTY INFORMATION APPENDIXC C ...
Page 406: ...vi 745 Transformer Management Relay GE Power Management ...
Page 407: ...GE Power Management 745 Transformer Management Relay NOTES ...