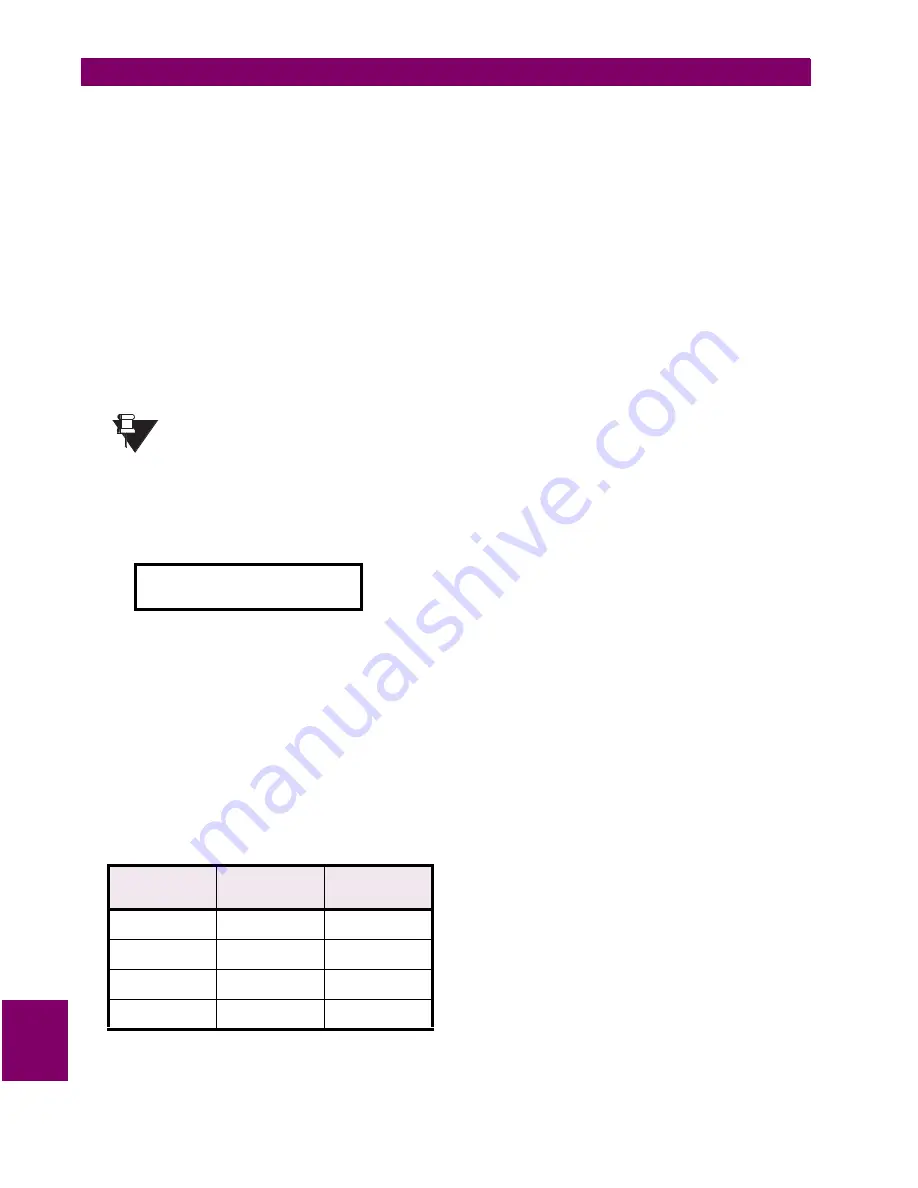
10-32
745 Transformer Management Relay
GE Power Management
10.6 PROTECTION SCHEMES
10 COMMISSIONING
10
To ensure that only the Negative Sequence Time Overcurrent element operates the trip relays (and any other
output relays selected by the logic) disable all protection features except Negative Sequence Time Overcur-
rent. Use the general test setup shown in Figure 10–9: GENERAL TEST SETUP on page 10–21.
Connect the current supply to terminals X = H1 and Y = G1 to test the Winding 1 negative-sequence element.
Monitor the appropriate output relays as per the relay FlexLogic settings.
b) PICKUP LEVEL
1.
With the interval timer disabled, apply the current signal and slowly increase its magnitude until the trip
relay and all selected auxiliary relays operate. If the relay has a very inverse time characteristic, it is easier
and more accurate to increase the current far above the pickup level until the trip relay operates then
reduce the current to just above the operate level. Then, slowly reduce the current below the operate level
and observe for a reset action on the trip relay. This reset level for the current should be approximately
98% of the pickup level. Once the relay drops out,
slowly
increase the current until the trip contact closes.
The operate level should correspond to the pickup setting:
SETPOINTS/S4 ELEMENTS/NEG SEQ OC/W1 NEG SEQ TIME OC/W1 NEG SEQ TIME OC PICKUP
With current applied to a single phase, the negative sequence current component is calculated
from:
Hence, the phase current will be three times the pickup setting.
2.
Check that, when the element operates, the TRIP and PICKUP LEDs are on and the following message is
displayed:
3.
Reduce the current until the element resets. The reset level should be 97% of the operate level. When the
element resets the TRIP and message indicators should remain on if the TARGET was selected as
latched. Otherwise only the TRIP indicator remains on.
Reset indicators and clear messages.
c) OPERATING TIME
Using a table like the one shown below, select 3 or 4 values of current multiples at which the timing is to be
measured. Enter the expected operating times from the timing curve applied in the settings. Using the setup in
Figure 10–9: GENERAL TEST SETUP on page 10–21 with the Interval Timer enabled, set the current level to
the desired value (taking into account the relationship mentioned above) and apply suddenly by closing the
double-pole switch. Record the operate time and compare to the expected value. Repeat for all desired values
of current.
yy
LATCHED (OPERATED):
yy
W1 Neg Seq Time OC
CURRENT
MULTIPLE
NOMINAL
TIME
MEASURED
TIME
1.5
3
5
NOTE
I
neg seq
1
3
---
I
phase
×
=
Summary of Contents for 745 TRANSFORMER MANAGEMENT RELAY
Page 30: ...2 8 745 Transformer Management Relay GE Power Management 2 3 SECURITY 2 GETTING STARTED 2 ...
Page 210: ...7 36 745 Transformer Management Relay GE Power Management 7 2 BLOCK DIAGRAMS 7 SCHEME LOGIC 7 ...
Page 322: ...9 12 745 Transformer Management Relay GE Power Management 9 3 USING 745PC 9 745 PC SOFTWARE 9 ...
Page 396: ...A 4 745 Transformer Management Relay GE Power Management A 1 FIGURES AND TABLES APPENDIXA A ...
Page 400: ...C 2 745 Transformer Management Relay GE Power Management C 1 WARRANTY INFORMATION APPENDIXC C ...
Page 406: ...vi 745 Transformer Management Relay GE Power Management ...
Page 407: ...GE Power Management 745 Transformer Management Relay NOTES ...