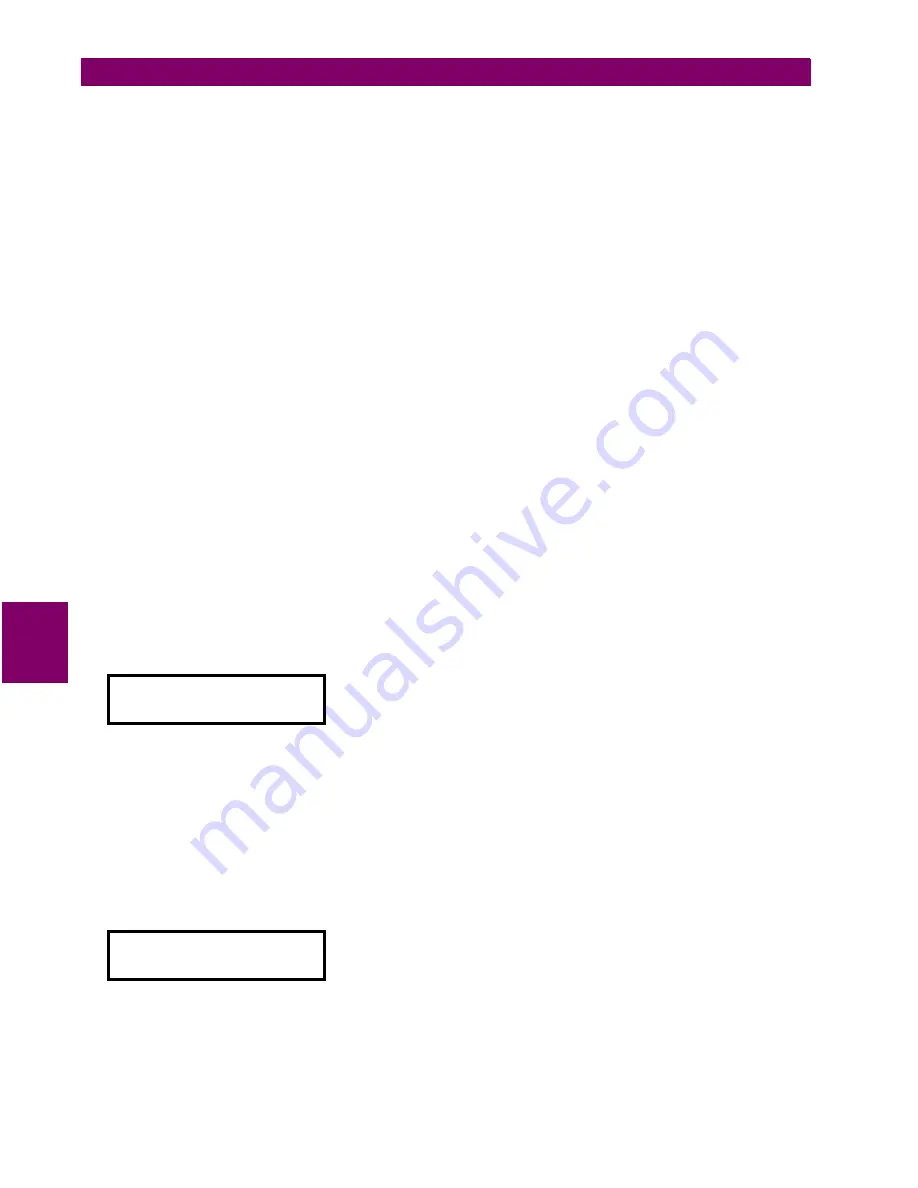
6-20
745 Transformer Management Relay
GE Power Management
6.6 TARGET MESSAGES
6 ACTUAL VALUES
6
The bottom line of the display (i.e.,
<CAUSE>
) will be the name of the element that has been activated. Follow-
ing are the elements available on the 745 (and which may appear in an active target display).
The recorded event displayed for Logic inputs and Virtual Inputs will show the programmed name of the input/
output. An active target display may also be generated as a result of a self-test error. When this occurs, the tar-
get message will look like this:
<ERROR> in the display will be one of the following:
For more detail about these errors, refer to Section 6.7: SELF-TEST ERRORS.
As well, there is an additional message that may appear as a target message. It looks like this:
This message will be placed in the target message queue whenever
S1 745 SETUP/INSTALLATION/745 SETPOINTS
is set to
Not Programmed
. This serves as a warning that the relay has not been programmed for the installation
and is therefore not in the in-service state.
Table 6–2: 745 PROTECTION ELEMENTS
Percent Differentl
Inst Differential
W1 Phase Time OC
W2 Phase Time OC
W3 Phase Time OC
W1 Phase Inst OC 1
W2 Phase Inst OC 1
W3 Phase Inst OC 1
W1 Phase Inst OC 2
W2 Phase Inst OC 2
W3 Phase Inst OC 2
W1 Ntrl Time OC
W2 Ntrl Time OC
W3 Ntrl Time OC
W1 Ntrl Inst OC 1
W2 Ntrl Inst OC 1
W3 Ntrl Inst OC 1
W1 Ntrl Inst OC 2
W2 Ntrl Inst OC 2
W3 Ntrl Inst OC 2
W1 Gnd Time OC
W2 Gnd Time OC
W3 Gnd Time OC
W1 Gnd Inst OC 1
W2 Gnd Inst OC 1
W3 Gnd Inst OC 1
W1 Gnd Inst OC 2
W2 Gnd Inst OC 2
W3 Gnd Inst OC 2
W1 Rest Gnd Fault
W2 Rest Gnd Fault
W3 Rest Gnd Fault
W1 Neg Seq Time OC
W2 Neg Seq Time OC
W3 Neg Seq Time OC
W1 Neg Seq Inst OC
W2 Neg Seq Inst OC
W3 Neg Seq Inst OC
Underfrequency 1
Underfrequency 2
Freq Decay Rate 1
Freq Decay Rate 2
Freq Decay Rate 3
Freq Decay Rate 4
Overfrequency
5th Harmonic Level
Volts-per-hertz 1
Volts-per-hertz 2
W1 THD Level
W2 THD Level
W3 THD Level
W1 Harmonic Derating
W2 Harmonic Derating
W3 Harmonic Derating
Analog Level 1
Analog Level 2
W1 Current Demand
W2 Current Demand
W3 Current Demand
Xformer Overload
Logic Input 1
Logic Input 2
Logic Input 3
Logic Input 4
Logic Input 5
Logic Input 6
Logic Input 7
Logic Input 8
Logic Input 9
Logic Input 10
Logic Input 11
Logic Input 12
Logic Input 13
Logic Input 14
Logic Input 15
Logic Input 16
Virtual Input 1
Virtual Input 2
Virtual Input 3
Virtual Input 4
Virtual Input 5
Virtual Input 6
Virtual Input 7
Virtual Input 8
Virtual Input 9
Virtual Input 10
Virtual Input 11
Virtual Input 12
Virtual Input 13
Virtual Input 14
Virtual Input 15
Virtual Input 16
y
SELF-TEST ERROR:
y
<ERROR>
Logic Power Out
Analog Output
Emulation Software
Real-Time Clock
Battery
Bad Xfmr Settings
Flexlogic Eqn
DSP Processor
EEPROM Memory
Access Denied
Not Calibrated
Int Temperature
IRIG-B Signal
y
SETPOINTS HAVE NOT
y
BEEN PROGRAMMED!
Summary of Contents for 745 TRANSFORMER MANAGEMENT RELAY
Page 30: ...2 8 745 Transformer Management Relay GE Power Management 2 3 SECURITY 2 GETTING STARTED 2 ...
Page 210: ...7 36 745 Transformer Management Relay GE Power Management 7 2 BLOCK DIAGRAMS 7 SCHEME LOGIC 7 ...
Page 322: ...9 12 745 Transformer Management Relay GE Power Management 9 3 USING 745PC 9 745 PC SOFTWARE 9 ...
Page 396: ...A 4 745 Transformer Management Relay GE Power Management A 1 FIGURES AND TABLES APPENDIXA A ...
Page 400: ...C 2 745 Transformer Management Relay GE Power Management C 1 WARRANTY INFORMATION APPENDIXC C ...
Page 406: ...vi 745 Transformer Management Relay GE Power Management ...
Page 407: ...GE Power Management 745 Transformer Management Relay NOTES ...