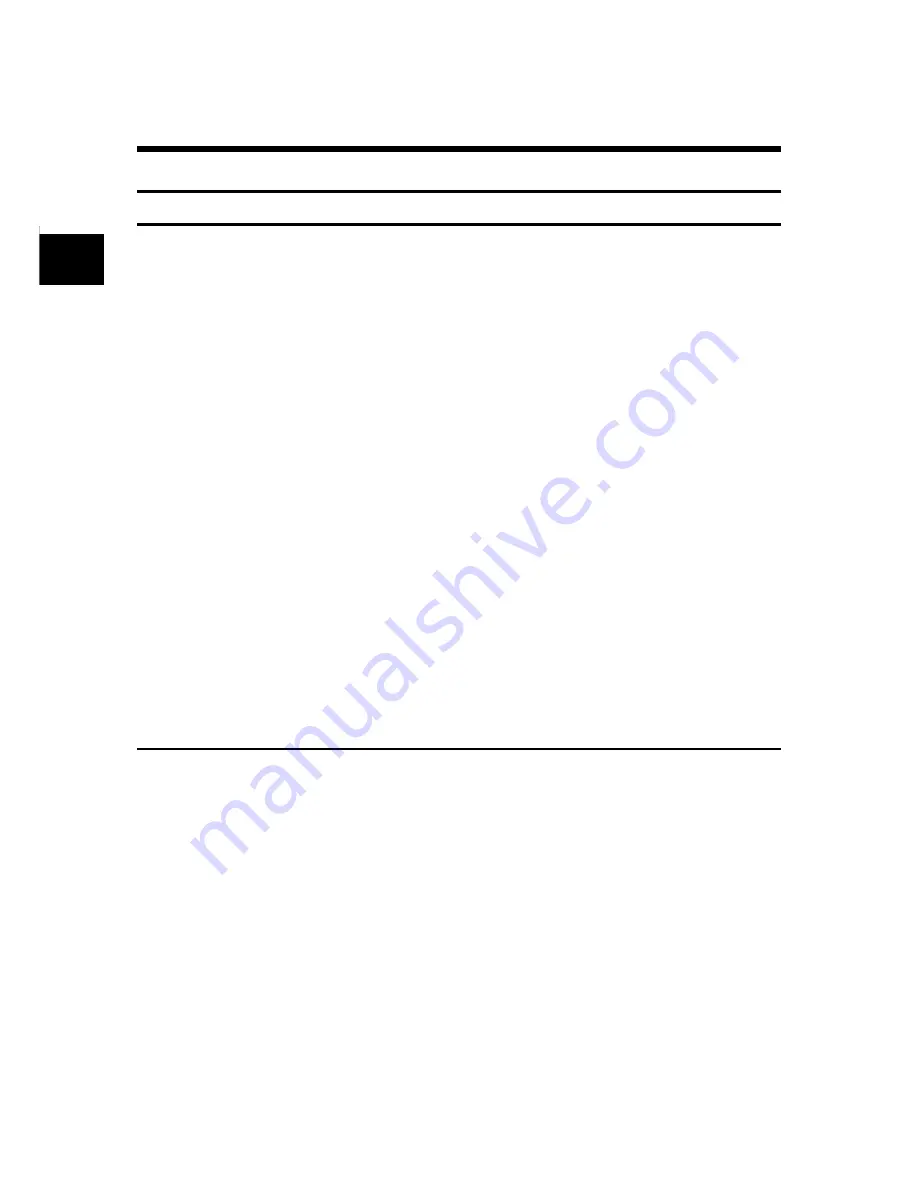
CHAPTER 2 WIRING
2-34
Description of I/O Signals
2
2.5.3 Signal Descriptions
Input signal
Servo-on [S-ON]: Sequence input signal (Reference value 1)
The signal makes the servomotor ready to rotate.
Function
The servomotor is ready to rotate while the servo-on [S-ON] signal remains turned on.
When the servo-on signal is turned off, the gate for IGBT is turned off and the servomotor does
not rotate. At this time, the servomotor in free-run and all rotation commands are ignored.
If the signal is turned off during rotation, controlled stop is caused according to the setting of
PA2_61 (action sequence at servo-on OFF). The stopping profile follows the setting of PA2_61
(action sequence at servo-on OFF), too.
If there is no alarm, activation of servo-on [S-ON] and forced stop [EMG] arranges the state ready
to rotate.
Parameter setting
To assign the servo-on [S-ON] signal to IQ area (sequence input terminal), specify the
corresponding value ("1") to the input terminal function setting parameter.
VS type: If not assigned to CONT 1 to 5, it is activated with ON signal in IQ area.
If assigned to CONT 1 to 5, it is activated when the signal (normally open contact) in IQ
area and signal (normally open contact) of CONT signal are both turned on.
Forward command [FWD]: Sequence input signal (Reference value 2)
Reverse command [REV]: Sequence input signal (Reference value 3)
The signal makes the servomotor keep running while it remains turned on.
(1) Speed control
VS type: The motor rotates at the speed specified in IQ area (word +12).
When both the forward rotation command [FWD] and reverse rotation command [REV]
are turned on, the motor is controlled to stop.
(2) Position control
VS type: When the position control (%QX*.14.9) is turned on, the position control mode is
activated while the signal is turned on.
While [FWD] (%QX*.14.14) or [REV] (%QX*.14.13) is turned on, the motor rotates at
the speed command set value (%QW*.12). The motor rotation speed 4000H is
equivalent to 3000 [r/min].
The motor rotation speed can be set at 6000 [r/min] by setting a value for the parameter
PA2_92 (SX extension function) (for VS) of 6000H.
Summary of Contents for ALPHA 5 RYT-SX
Page 1: ...MEHT301a FUJI SERVO SYSTEM USER S MANUAL RYT SX type ...
Page 19: ...0 1 CHAPTER 0 INTRODUCTION 0 ...
Page 34: ...CHAPTER 0 INTRODUCTION 0 16 Combination between Servomotor and Servo Amplifier 0 ...
Page 35: ...1 1 CHAPTER 1 INSTALLATION 1 ...
Page 45: ...2 1 CHAPTER 2 WIRING 2 ...
Page 142: ...CHAPTER 2 WIRING 2 98 Description of I O Signals 2 ...
Page 143: ...3 1 CHAPTER 3 OPERATION 3 ...
Page 197: ...4 1 CHAPTER 4 PARAMETER 4 ...
Page 296: ...CHAPTER 4 PARAMETER 4 100 Output Terminal Function Setting Parameters 4 ...
Page 297: ...5 1 CHAPTER 5 SERVO ADJUSTMENT 5 ...
Page 329: ...6 1 CHAPTER 6 KEYPAD 6 ...
Page 371: ...7 1 CHAPTER 7 MAINTENANCE AND INSPECTION 7 ...
Page 389: ...8 1 CHAPTER 8 SPECIFICATIONS 8 ...
Page 414: ...CHAPTER 8 SPECIFICATIONS 8 26 Dimensions of Servo Amplifier 8 ...
Page 415: ...9 1 CHAPTER 9 CHARACTERISTICS 9 ...
Page 425: ...10 1 CHAPTER 10 PERIPHERAL EQUIPMENT 10 ...
Page 463: ...11 1 CHAPTER 11 ABSOLUTE POSITION SYSTEM 11 ...
Page 473: ...12 1 CHAPTER 12 POSITIONING DATA 12 ...
Page 482: ...CHAPTER 12 POSITIONING DATA 12 10 Response Time 12 ...
Page 483: ...13 1 CHAPTER 13 PC LOADER 13 ...
Page 513: ...14 1 CHAPTER 14 APPENDIXES 14 ...
Page 545: ...CHAPTER 14 APPENDIXES Service Network 14 33 14 14 8 Service Network ...
Page 546: ...CHAPTER 14 APPENDIXES 14 34 Service Network 14 ...