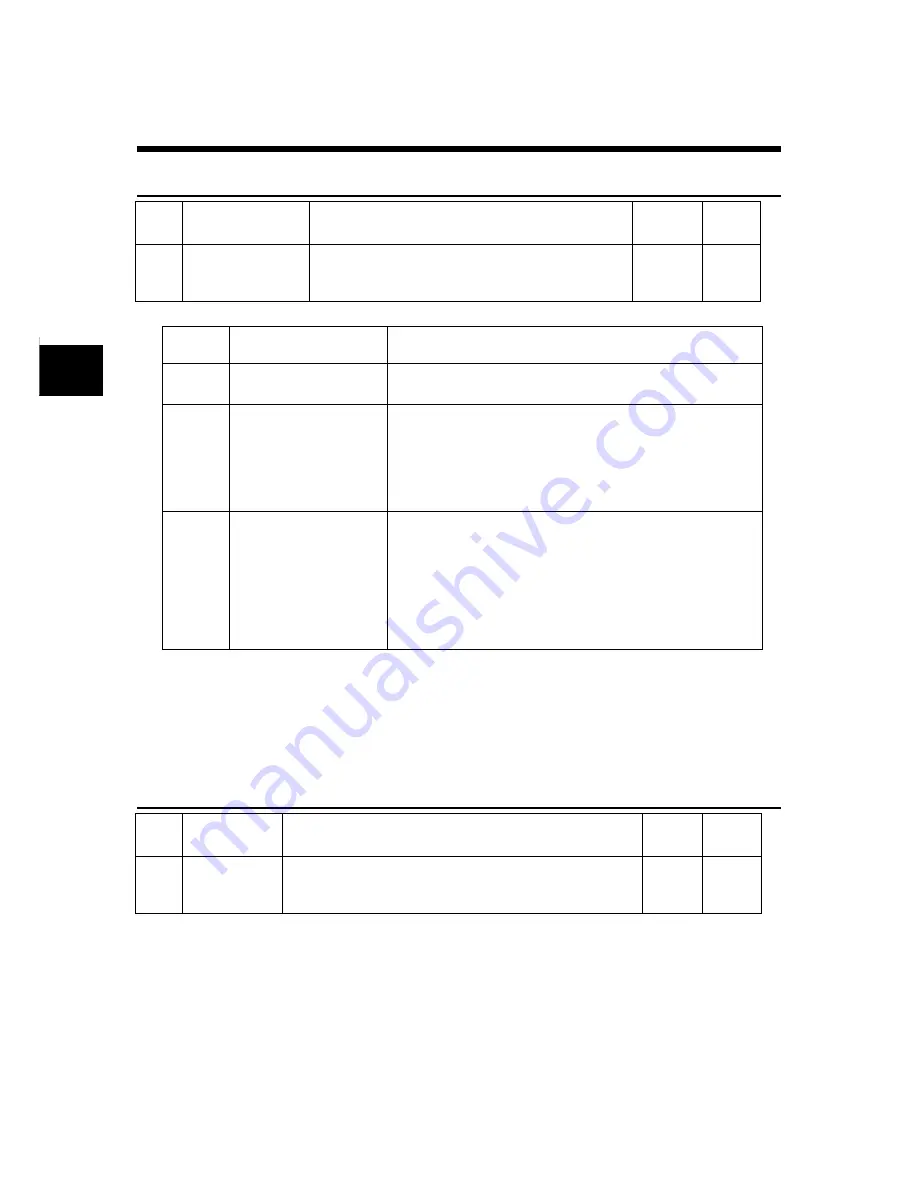
CHAPTER 4 PARAMETER
4-4
Basic Parameters
4
4.2.2 Description of Each Parameter
PA1_02 INC/ABS system selection
No. Name
Setting
range
Default
value
Change
02
INC/ABS selection 0: Incremental system 1:Absolute system
2: Non-overflow absolute system
(not detect the multi-turn overflow)
0 Power
Select either the relative position (incremental) system or absolute position system.
Reference
value
Function Description
0
Relative position
(incremental) system
The current position is lost after the control power is turned
off. Homing must be performed again.
1
Absolute position
system
The current position is stored in memory even after the
control power is turned off. Homing is unnecessary. You
can operate in the limited range. If the operation range is
exceeded, an alarm and stoppage are caused.
(Operation range: between -32768 and +32768 revolutions
of motor shaft)
2
Non-overflow absolute
system (not detect the
multi-turn overflow)
The current position is stored in memory even after the
control power is turned off. Homing is unnecessary.
Because there is no limit in the operation range, this
system is best for the control of the rotating body. (The
multi-turn data over flow alarm is not detected.)
Multi-rotation data should be processed at the host
controller suitably.
Specify so that the ratio of PA1_06 to 07 = 2
n
/1.
To establish an absolute position system, set this parameter at "1" or "2." In addition, install the
optional absolute backup battery.
Because a multi-rotation data loss alarm (dL1 alarm) is detected when the power is turned on,
perform position presetting to remove the alarm and start operation.
•
To use in an absolute position system, refer to "CHAPTER 11 ABSOLUTE POSITION
SYSTEM."
PA1_03 Command pulse form selection
No. Name
Setting
range
Default
value
Change
03
Command
pulse form
selection
0: Command pulse/direction
1: Forward/reverse pulse 2: A / B phase pulse
1
Power
This parameter is enabled only under position control.
You can select the signal format of the command pulse input terminal.
The pulse format of the command pulse input terminals [CA], [*CA], [CB] and [*CB] of the servo
amplifier can be specified.
The maximum input frequency is 1.0 [MHz] at differential input or 200 [kHz] at open collector input.
However, enter each signal so that the following conditions are satisfied (the same signal conditions
apply to CA, *CA, CB and *CB).
In case of A/B phase pulse, the rising or falling edge of the A-phase signal or B-phase signal is counted
as a single pulse, so that a single-pulse input is equivalent to four pulse counts.
Summary of Contents for ALPHA 5 RYT-SX
Page 1: ...MEHT301a FUJI SERVO SYSTEM USER S MANUAL RYT SX type ...
Page 19: ...0 1 CHAPTER 0 INTRODUCTION 0 ...
Page 34: ...CHAPTER 0 INTRODUCTION 0 16 Combination between Servomotor and Servo Amplifier 0 ...
Page 35: ...1 1 CHAPTER 1 INSTALLATION 1 ...
Page 45: ...2 1 CHAPTER 2 WIRING 2 ...
Page 142: ...CHAPTER 2 WIRING 2 98 Description of I O Signals 2 ...
Page 143: ...3 1 CHAPTER 3 OPERATION 3 ...
Page 197: ...4 1 CHAPTER 4 PARAMETER 4 ...
Page 296: ...CHAPTER 4 PARAMETER 4 100 Output Terminal Function Setting Parameters 4 ...
Page 297: ...5 1 CHAPTER 5 SERVO ADJUSTMENT 5 ...
Page 329: ...6 1 CHAPTER 6 KEYPAD 6 ...
Page 371: ...7 1 CHAPTER 7 MAINTENANCE AND INSPECTION 7 ...
Page 389: ...8 1 CHAPTER 8 SPECIFICATIONS 8 ...
Page 414: ...CHAPTER 8 SPECIFICATIONS 8 26 Dimensions of Servo Amplifier 8 ...
Page 415: ...9 1 CHAPTER 9 CHARACTERISTICS 9 ...
Page 425: ...10 1 CHAPTER 10 PERIPHERAL EQUIPMENT 10 ...
Page 463: ...11 1 CHAPTER 11 ABSOLUTE POSITION SYSTEM 11 ...
Page 473: ...12 1 CHAPTER 12 POSITIONING DATA 12 ...
Page 482: ...CHAPTER 12 POSITIONING DATA 12 10 Response Time 12 ...
Page 483: ...13 1 CHAPTER 13 PC LOADER 13 ...
Page 513: ...14 1 CHAPTER 14 APPENDIXES 14 ...
Page 545: ...CHAPTER 14 APPENDIXES Service Network 14 33 14 14 8 Service Network ...
Page 546: ...CHAPTER 14 APPENDIXES 14 34 Service Network 14 ...