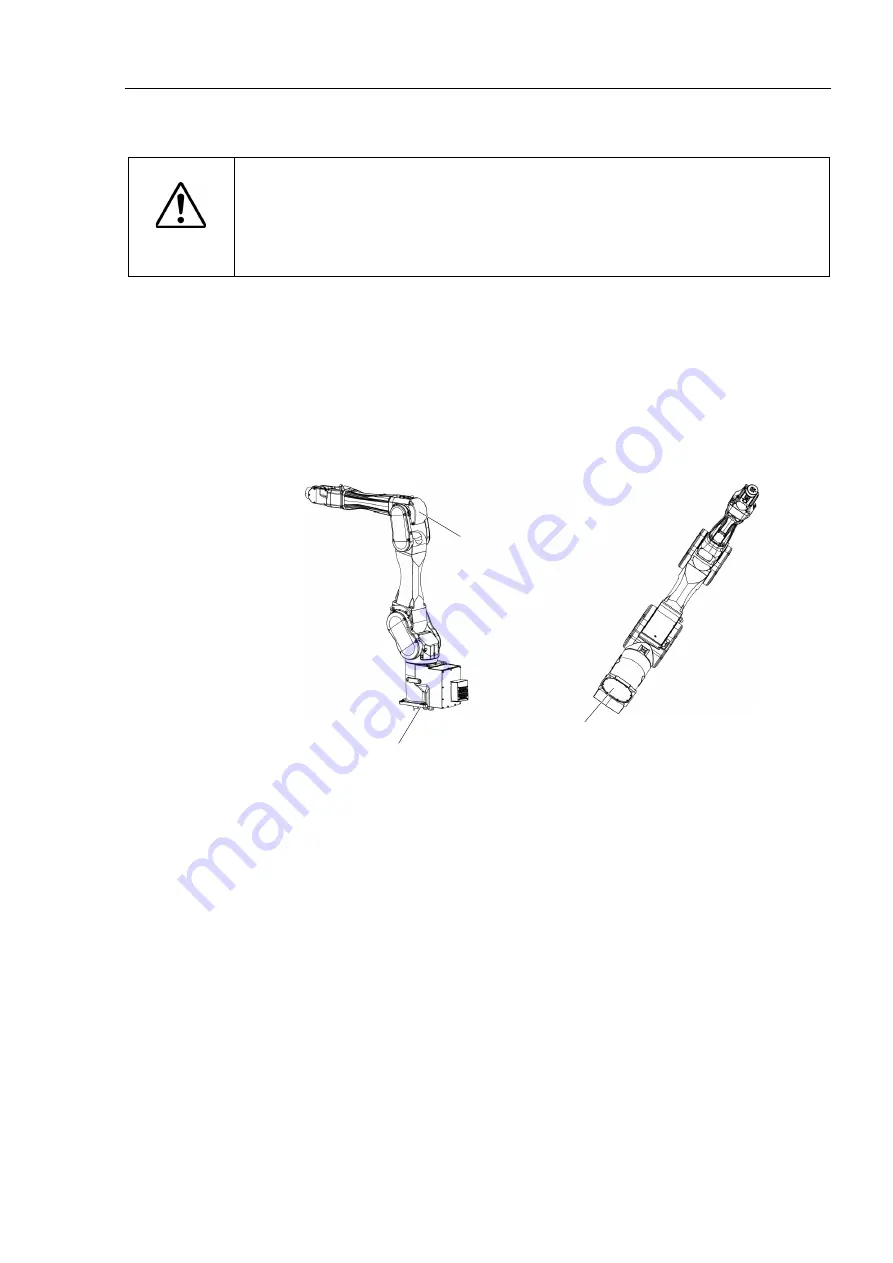
Maintenance 16. Calibration
C12 Rev.3
291
Also, pay attention to the following points at the encoder initialization.
CAUTION
■
The Joint #1 and Joint #4 have no mechanical stops and they may be rotated
more than 360 degrees. If the encoder initialization is performed with improper
posture, the Manipulator moves outside the operation range. If the Manipulator
was moved outside the operation range, the internal wiring may be damaged by
being twisted or pinched and it may result in Manipulator malfunction.
When the home positions of the Joints #1 and #4 are uncertain, check torsion of the internal
cables. The home positions are where the Manipulator has the internal cables not twisted
at the basic orientation described in
Setup & Operation 3.7 Checking the Basic orientation
.
Torsion of the internal cables can be checked by removing the following covers.
Joint #1 : Base cover (Cable backward model)
: Connecter plate (Cable downward model)
Joint #4 : Arm #3 cover (common between cable downward and cable backward models)
Connecter plate
(Cable downward model)
Arm #3 cover
(common between cable downward
and cable backward models)
Base cover
(Cable backward model)
NOTE
Summary of Contents for C12 Series
Page 1: ...Rev 3 EM204R4255F 6 Axis Robots C12 series MANIPULATOR MANUAL ...
Page 2: ...Manipulator manual C12 series Rev 3 ...
Page 8: ...vi C12 Rev 3 ...
Page 14: ...Table of Contents xii C12 Rev 3 ...
Page 16: ......
Page 30: ...Setup Operation 2 Specifications 16 C12 Rev 3 2 4 Outer Dimensions Unit mm ...
Page 84: ......
Page 155: ...Maintenance 4 Cable Unit C12 Rev 3 141 4 2 Connector Pin Assignment 4 2 1 Signal Cable ...
Page 156: ...Maintenance 4 Cable Unit 142 C12 Rev 3 ...
Page 157: ...Maintenance 4 Cable Unit C12 Rev 3 143 ...
Page 158: ...Maintenance 4 Cable Unit 144 C12 Rev 3 4 2 2 Power Cable ...