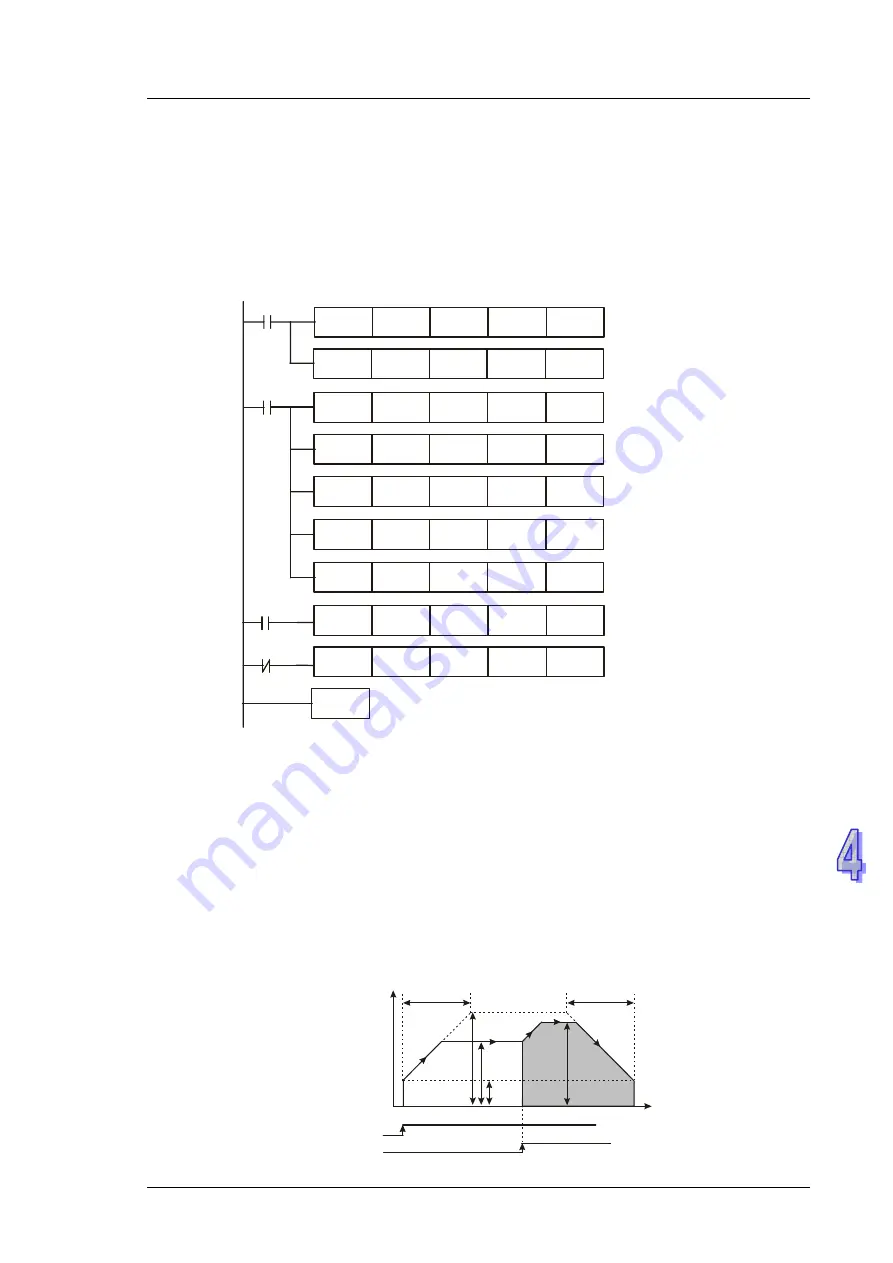
4 . P o s i t i o n i n g U n i ts
MN05003006E F or more information visit:
w w w. e a t o n . c o m
4-37
Once the mode is enabled, the execution will follow the operation speed (I) and enter
operation speed (II) after the 1
st
movement is complete. The execution will stop after
operation speed (II) is reached.
y
When X0 = Off, stop the execution of 2-speed positioning.
5.
Program example
Ladder diagram:
Explanation:
Read the current position
Read the current speed
Set up as 2-speed positioning
mode
Set up target position I
Set up operation speed I
Set up target position II
Set up operation speed II
Enable the 2-speed
positioning mode
Stop the execution
M1000
M1002
X0
X0
K0
K35
K1
K0
K23
K1
K25
K1
END
DTO
DFROM
K0
K33
K1
DFROM
DTO
TO
K0
K31
K1
TO
K0
K31
K0
K27
K1
K29
K1
DTO
DTO
K0
K32
K1
DTO
D100
D200
K4
K10000
K1000
K30000
K10000
K256
K2
K1
K0
K0
Interrupt 2-speed Positioning
1.
Control requirements
y
Write K8 (H’8, i.e. b3 = 1) into CR#32 to enable interrupt 2-speed positioning
y
Set up CR#25, #26 (target speed I).
y
Set up CR#27, #28 (target position II) and CR#29, #30 (target speed II).
2.
Devices
y
X0 = On: software starts.
y
X0 = Off: stop the execution (controlled by the software)
3.
Interrupt 2-speed positioning mode
Speed
T
ACC
T
DEC
V
MAX
Time
V
BIAS
Start
DOG
V(I)
V(II)
P(II)