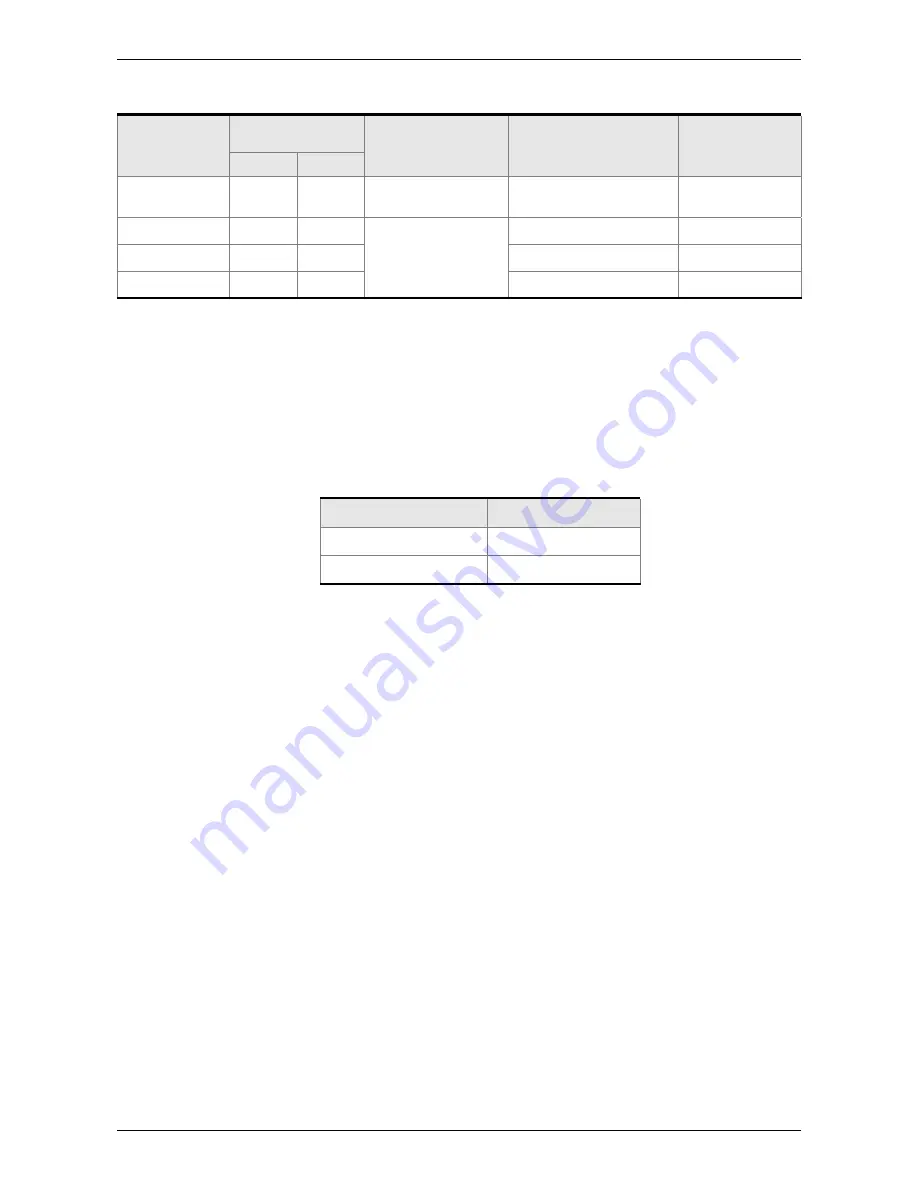
ASDA-B2
Chapter 5 Trial Operation and Tuning
Revision May, 2018
5-9
The speed command selection is determined by SPD0 and SPD1. See the table below.
Speed
Command No.
DI signal of CN1
Command Source
Content
Range
SPD1
SPD0
S1 0
0
External analog
command
Voltage between
V-REF and GND
-10V ~ +10V
S2 0
1
Register parameter
P1-09
-50000 ~ 50000
S3
1
0
P1-10
-50000 ~ 50000
S4
1
1
P1-11
-50000 ~ 50000
0: means DI is OFF; 1: means DI is ON
Register parameter
The parameter setting range is from -50000 to 50000.
Setting speed = Setting value x unit (0.1 r/min).
For example: P1-09 = +30000; Setting speed = +30000 x 0.1 r/min = +3000 r/min
Command setting of speed register
P1-09 is set to 30000
Input command
Rotation direction
P1-10 is set to 1000
+ CW
P1-11 is set to -30000
- CCW
STEP 3:
(1) Users switch ON DI1 and Servo ON.
(2) Both DI3 (SPD0) and DI4 (SPD1), the speed command, are OFF, which means it
currently executes S1 command. The motor rotates according to analog voltage
command.
(3) When DI3 (SPD0) is ON, it means it currently executes S2 command (3000 r/min).
The speed is 3000 r/min at the moment.
(4) When DI4 (SPD1) is ON, it means it currently executes S3 command (100 r/min).
The speed is 100 r/min.
(5) When both DI3 (SPD0) and DI4 (SPD1) are ON, it means S4 command (-3000 r/min)
is executed at the moment. The speed is -3000 r/min.
(6) Step (3), (4), and (5) can be repeatedly executed.
(7) If users desire to stop the motor, switch OFF DI1 (Servo OFF).