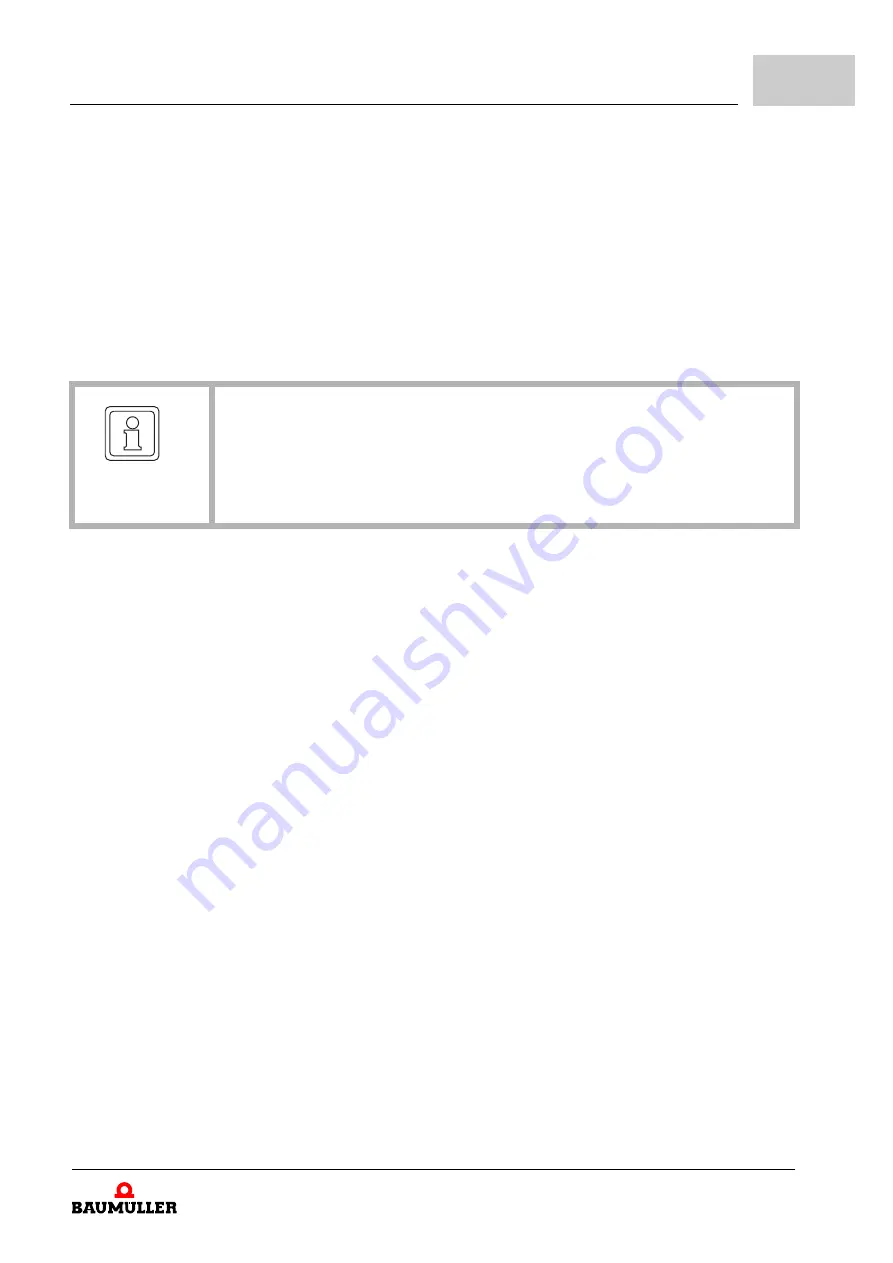
Description of the Software Modules and Parameters
Parameter manual
b maXX
BM3000
Document no.: 5.12001.07
633
4
– Synchronicity is considered to be established when the slave axis enters the
Synchronization velocity window for the first time around the speed set val-
ue of the master axis. From this point, the controller will independently switch from
the internal ramp generator to the set value of the master axis.
– If the master axis changes its speed during synchronization in progress, the target
speed for the ramp generator will be adjusted accordingly.
If the new target speed slows down, braking occurs with a deceleration value
to the new value.
In the case of the S-curve, the current acceleration value must first be reduced through
the jerk value setting
, which means the speed will first be increased further.
m
Bit
9: Speed profile of the ramp generator
This bit is used to set the speed profile for the ramp generator. The ramp generator is
active with the virtual master axis and speed synchronization processes.
m
Bit 12: Virtual master axis - Handling the speed set value of the virtual master
axis
If Bit 12 is set to 0, the value in Parameter
Speed set value is routed through
the ramp generator of the synchronous operation to the transmission input. Parame-
ters
apply as profile data. The profile type is set in the
Mode Bit 9.
If Bit 12 is set, the speed set value is immediately routed to the transmission input with-
out ramp generator. Optionally, an interpolation can also be activated for the speed set
value. When the interpolation is active, the result will be a set value at the transmission
input that is delayed by an interpolation interval of - 1 ms.
The interpolation interval setting is entered in
Virt. lead set value cycle.
145.3
Gear slave axis revolutions
Counter in the transmission ratio i of the electronic transmission.
The input of 0 is rejected and the old value remains effective. The control word Bit 8 must
be used to stop the slave axis.
NOTE!
With deactivated speed synchronization (Bit 8 = 0) the slave axis may not be added
to a moving master axis and a stop may not be ended. Because the master axis set
value is transferred immediately, an undesired fast acceleration may occur depend-
ing on the master speed. This may lead to damage to the mechanism and trigger a
error when position error monitoring is active.