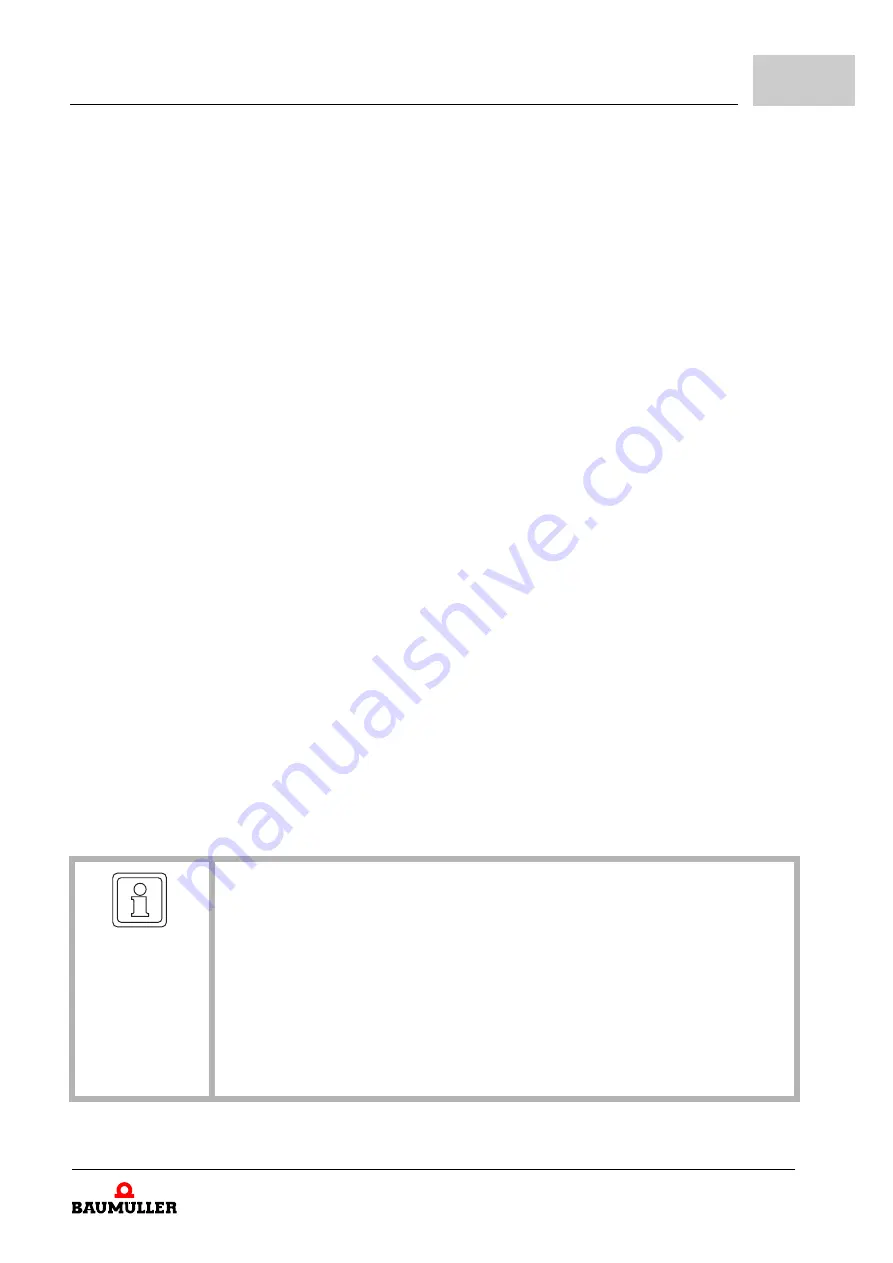
Description of the Software Modules and Parameters
Parameter manual
b maXX
BM3000
Document no.: 5.12001.07
205
4
Rotor resistance
Rotor leakage inductance
A total of 4 parameters are entered in the current controller module and 3 or 4 parameters
in the motor identification plate module. Additionally, it is possible to calculate the current
controller with the identified parameters in ProDrive.
123.12
Time constant of step response
This parameter displays the identified time constant for asynchronous motors. The cur-
rent level for this is approx. 80% (current rise from 75% to 85%) of the maximum current
(
). For synchronous motors the current level is 85% (current rise from 75% to
95%) of the maximum current and from that the value can be compared with the Result
Current Controller Tn (
) in order to assess the saturation effects. A clear satura-
tion effect is present if the step response time constant is clearly less than the value of
the Result Current Controller Tn (
has in
effect been measured with a current of 50% of the maximum current (
).
123.14
Normalized error
This parameter shows the normalized error that has been established while determining
the step response time constant (
). The quality of the evaluation can be as-
sessed from the value and a value of less than 5% can be considered good.
123.15
Dead time compensation table
Table of the current-dependent correction of the voltage setting based on the measured
IGBT dead time.
The table is displayed graphical in ProDrive on page "Autotuning current controller" by
clicking on button "Dead time compensation".
NOTE!
Up to Firmware version
V01.08:
The table is valid for the set operating frequency of
the power unit at time of measurement, only. Measurement for the dead time com-
pensation must be made again if the operating frequency (
) was changed!
From Firmware version
V01.09:
If the correction table (dead time) is measured during
the adaption of the dead time compensation according to the PWM frequency is ac-
tive (
bit 3 = 1), the effective voltage of the dead time compensation is cor-
rected according to the effective PWM frequency. Therefore, a dead time
measurement after a change of the PWM frequency is not necessary anymore. How-
ever, the best results are generally reached if the used PWM frequency corresponds
to the PWM frequency at the moment of the dead time measurement.