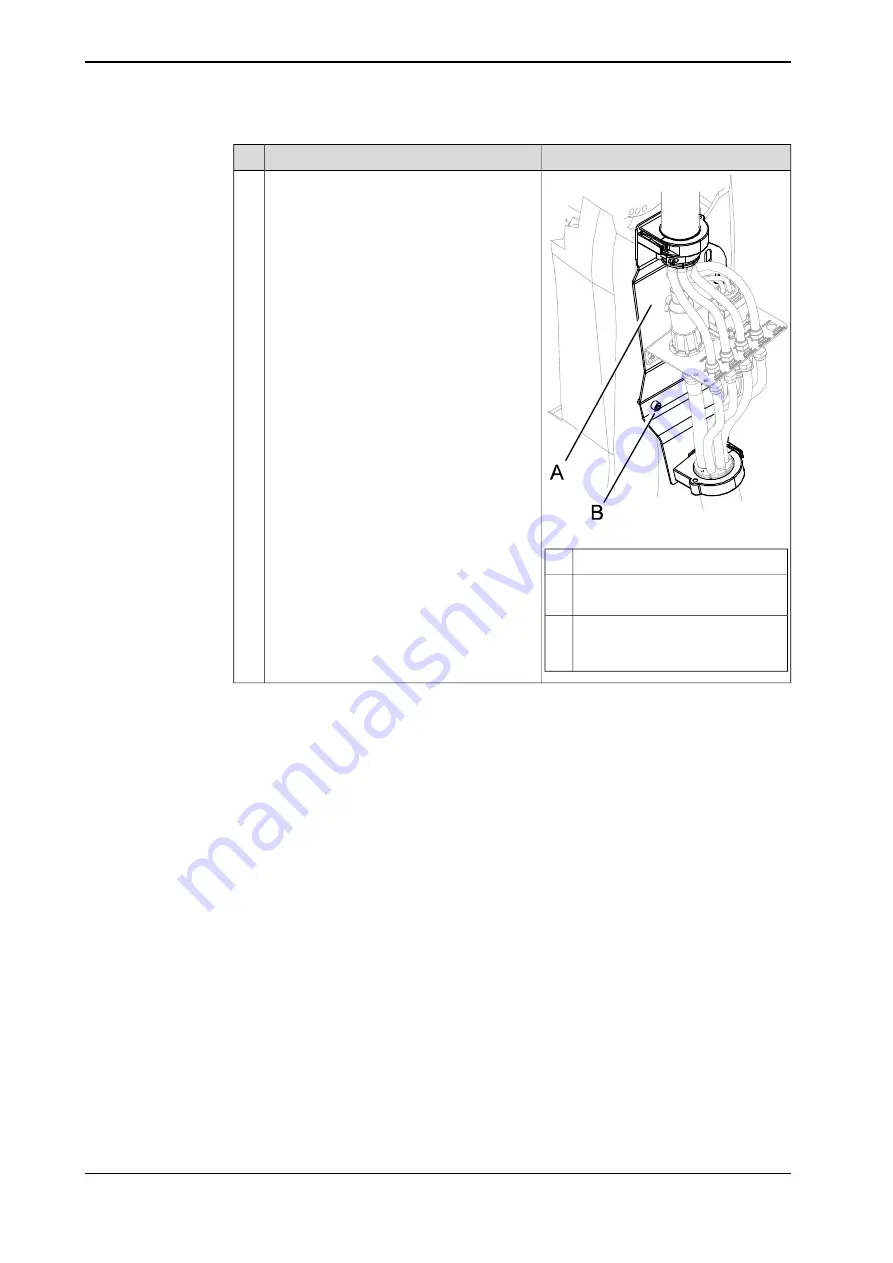
Note
Action
xx0700000327
Fit the lower arm plate to the lower arm with
its attachment screws.
Lock the screws with locking liquid.
6
Lower arm plate
A
Screw, M12x25, quality 8.8-A3F (4
pcs) (short upper arm)
B
Screws, M12x25 (2 pcs) and
M12x35 (2 pcs) with 2 washers,
quality 8.8-A3F (long upper arm)
C
Continues on next page
56
Product manual - DressPack/SpotPack IRB 6640
3HAC028638-001 Revision: K
© Copyright 2007-2018 ABB. All rights reserved.
2 Installation
2.2.3 Fitting the attachments of IRBDP MH2 LE and IRBDP SW2 LE
Continued
Summary of Contents for DressPack IRB 6640
Page 1: ...ROBOTICS Product manual DressPack SpotPack IRB 6640 ...
Page 8: ...This page is intentionally left blank ...
Page 18: ...This page is intentionally left blank ...
Page 44: ...This page is intentionally left blank ...
Page 194: ...This page is intentionally left blank ...
Page 220: ...This page is intentionally left blank ...
Page 324: ...This page is intentionally left blank ...
Page 338: ...This page is intentionally left blank ...
Page 364: ...This page is intentionally left blank ...
Page 366: ...This page is intentionally left blank ...
Page 369: ......