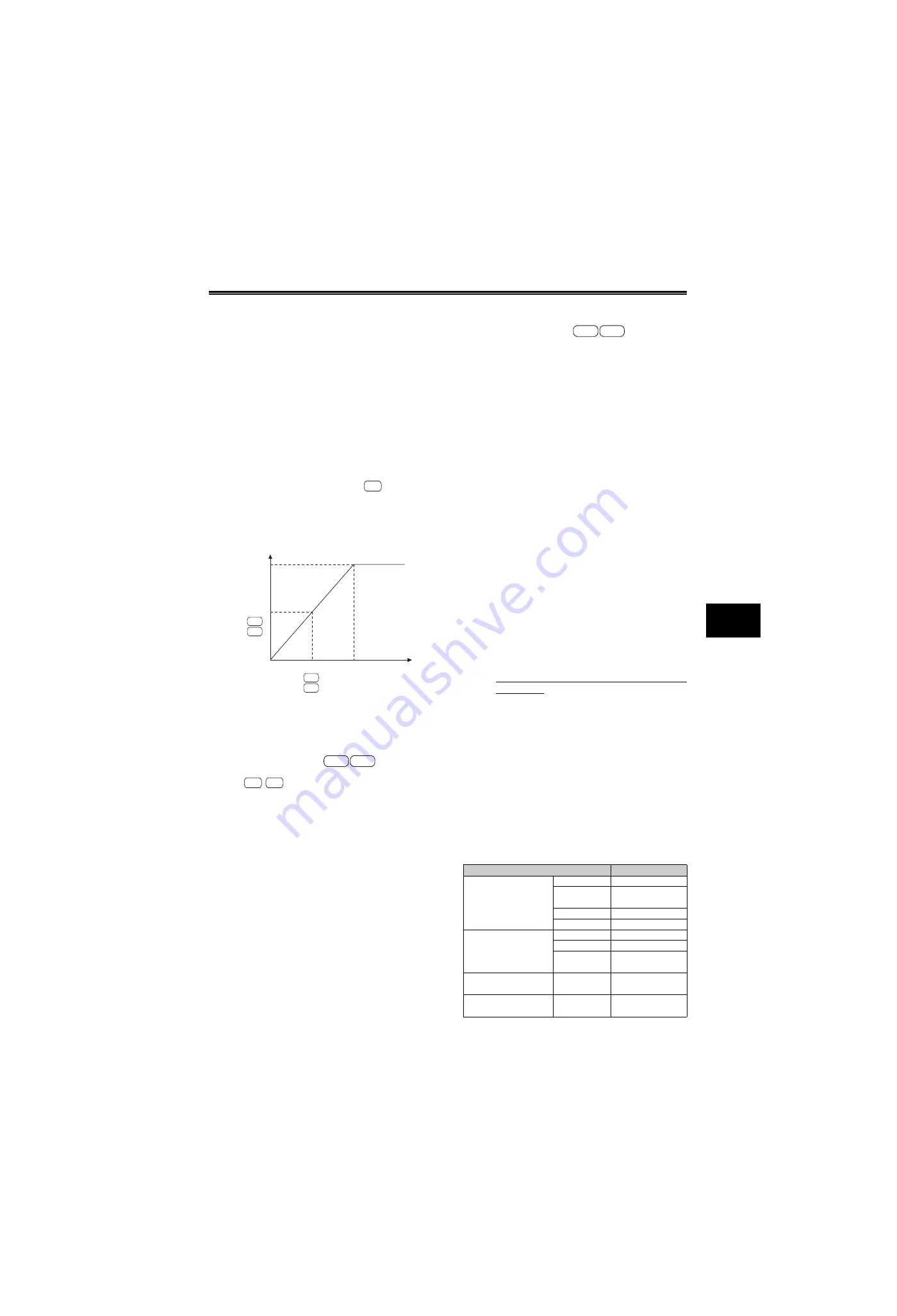
371
PARAMETER
2
P
ARAM
ETE
R
frequency. Adjust the coasting time between 0.1s and
5s according to the load specifications.
(4) Restart cushion time [Pr. 58]
Cushion time is the length of time taken to raise the
voltage appropriate to the detected motor speed
(output frequency prior to instantaneous power failure
when
Pr. 162
= "1" or "11").
Normally the initial value need not be changed for
operation, but adjust it according to the magnitude of
the load inertia (J) of the load or torque.
[
Pr. 58 Restart cushion time
] is invalid during encoder
feedback control ([
Pr. 162
= 2, 12]), Real sensorless
vector control or vector control on
.
The SU and FU signals are not output during a
restart. These are output after the restart cushion
time has elapsed.
(5) Automatic restart operation selection [Pr.
163*, 164*, 165, 611]
(*Not available for
.)
In
, voltage rise time at a restart can be
adjusted as shown above using [
Pr.163, 164
]. Using
[
Pr. 165
], the stall prevention operation level at a
restart can be set.
Acceleration time (acceleration slope) can be set
using [
Pr. 611 Acceleration time at a restart
] separately
from the acceleration time in normal operation. For
[
Pr. 611
], set the acceleration time to reach [
Pr.20
Acceleration/deceleration reference frequency
] from 0Hz.
(If the [
Pr. 21 Acceleration/deceleration time increments
]
setting is changed, the setting increments of [
Pr. 611
]
remain unchanged.)
(6) Frequency search gain
(Pr. 298)
, offline
auto tuning
(Pr. 96)
When automatic restart after instantaneous power
failure operation (with frequency search) is valid at V/
F control, perform offline auto tuning.
Perform offline auto tuning during V/F control in the
following order to set
Pr. 298
Frequency search gain
automatically.
(Refer to page 268 during Advanced magnetic flux
vector control and General-purpose magnetic flux
vector control.)
z
Checking the wiring and load
Check the following before performing offline auto
tuning.
1) Connect a motor, and select V/F control. Note that
the motor should be at a stop at a tuning start.
2) The motor capacity should be equal to or one rank
lower than the inverter capacity.(Note that the
capacity is 0.1kW or more.)
3) Auto tuning can be performed with load (such as
friction and steady load) connected to the motor.
Note that tuning is more accurate with smaller
load. Tuning accuracy is not affected if the inertia
is large.
4) Even when [
Pr.96
=21] (tuning without running
motor), the motor may run slightly. Therefore, fix
the motor securely with a mechanical brake, or
before tuning, make sure that there will be no
problem in safety if the motor runs.
*Especially fix the motor securely in vertical lift
applications. Note that tuning performance is
unaffected even if the motor runs slightly.
z
Parameter setting
Set the following parameters.
1) [
Pr. 96 Auto tuning setting/status
]
............ Set 21.
Tuning is performed without running the
motor.
2) [
Pr. 9 Electric thermal
]
............ Set motor rated current (A).
3) [
Pr. 71 Applied motor
]
............ Select the setting value from the
below table.
A700
Voltage
100%
[
Pr.164
]
[
Pr.163
]
[
Pr.58
]
Time
0
A700
F700
A700
F700
E700
D700
A700 F700
Motor
Pr.71
Setting
Mitsubishi standard
motor
Mitsubishi high
efficiency motor
SF-JR
3
SF-JR 4P
1.5kW or less
23
SF-HR
43
Others
3
Mitsubishi constant-
torque motor
SF-JRCA 4P
13
SF-HRCA
53
Others (SF-
JRC, etc.)
13
Other manufacturer's
standard motor
—
3
Other manufacturer's
constant torque motor
—
13
E700
D700
Содержание FR-A700 Series
Страница 245: ...279 2 PARAMETER PARAMETER MEMO ...
Страница 440: ...474 PARAMETER MEMO ...
Страница 522: ...556 SELECTION MEMO ...