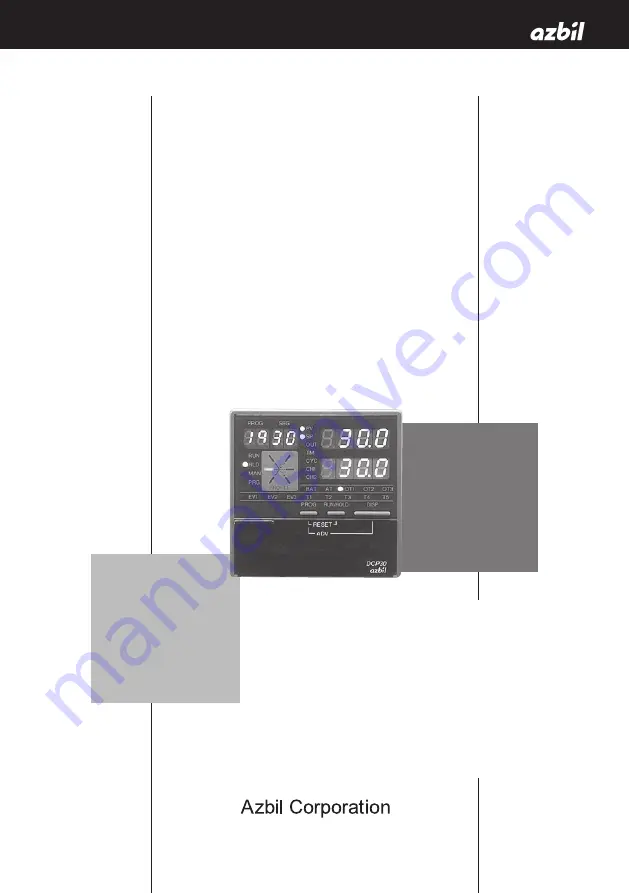
Thank you for purchasing an Azbil
Corporation product.
This manual contains information
for ensuring the correct use of this
product. It also provides necessary
information for installation, main-
tenance, and troubleshooting.
This manual should be read by
those who design and maintain
equipment that uses this product.
Be sure to keep this manual nearby
for handy reference.
DCP31
DIGITRONIK
Digital Program
Controller
User's Manual
No. CP-UM-1757E
(Not for use in Japan)