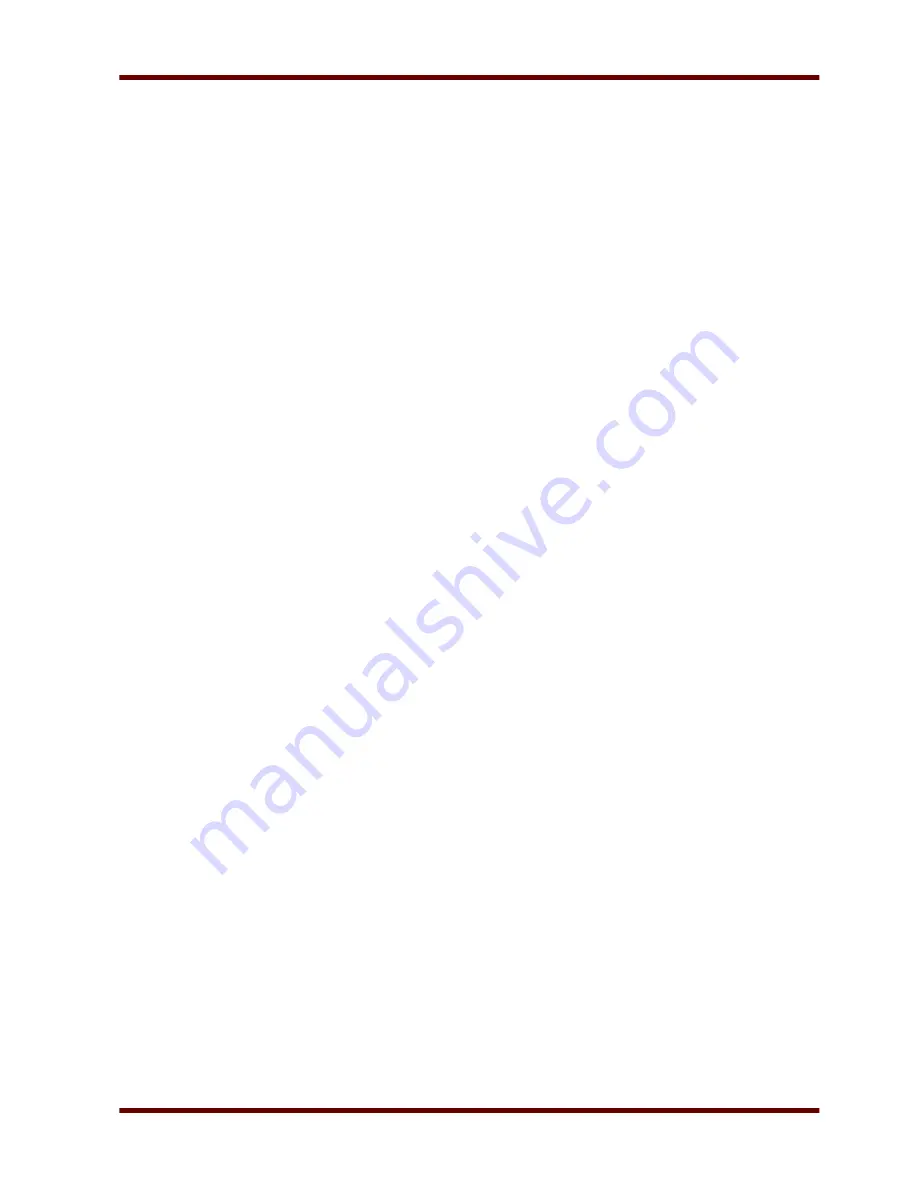
Protective Elements
Blocking Conditions
The reasons for a Motor Start Blocking are as follows.
The Motor Start will be blocked due to:
•
There are too many starts per hour (if configured).
•
The waiting time between starts is not elapsed (if configured).
•
If the Anti Backspin protection detects a reversing of the motor (reversing not allowed, if configured).
•
The thermal model blocks the motor (if configured).
•
External Blocking becomes active (if configured).
When any of Anti-Backspin, thermal, and external blocks are on, the »
MStart.Blo«
signal will be set. The »
TBS«
and »SPH« can turn on the »
MStart.Blo«
signal only if the motor is not in a cold start sequence; »
NOCS«
block
can not cause the »
MStart.Blo«
signal to be set.
Start Limits
Because motor starting consumes a considerable amount of thermal energy compared to its normal load
conditions, the number of starts in a given time period must be monitored and controlled. The protective device
has three functions that contribute to the start limits monitoring. These are:
•
TBS (Time between Starts);
•
SPH (Starts per Hour); and
•
NOCS (Number of Cold Starts).
Most motors can tolerate some number of consecutive cold starts before the time between starts is enforced.
The protective device treats a start as the first in a sequence of cold starts if the motor has been stopped for at
least the time period that is the greatest of »
one hour«
and »
TBS
«. Subsequent starts are treated as additional
cold starts in the same sequence, only if they run no more than ten minutes, until the set number of cold starts is
reached. Once the motor is in the cold starting sequence, it will ignore »
TBS«
and »
SPH
« limits. The cold start
sequence will be terminated if the motor has run for more than ten minutes for a cold start before it exhausts
»
NOCS«
, then starts after this are subject to time and count limits imposed by »
TBS«
and »
SPH«
. If the motor
reaches the »
NOCS«
limit in a cold start sequence, »
NOCS«
block signal will be set and »
TBS«
will start to time.
When »
TBS«
reaches its limit while the »NOCS« block signal is still set, the cold start sequence will be
terminated and the »
NOCS«
block will be released. Meanwhile, the »
SPH«
will start to count at the last start in
the complete cold start sequence.
Stop Cycle
The run cycle continues until the motor current level falls below the Stop Current Threshold setting current on all
three phases. Then a stop is declared. The start limits (also referred as Jogging start limits) and the anti-
backspin time delay (ABS) are checked. If blocking conditions exist, the protective device can be configured to
block a motor from starting. Remaining jogging block times are displayed and counted down, indicating how
long to wait. If there are no such starting block conditions in effect, the protective device is ready for a new start.
Anti-Backspin Delay Time (ABS)
»ABS«
sets the time in seconds before a motor restart is permitted after a trip or stop condition. This function
can be set to »
inactive«
.
This function is used with a motor driving a pump working into a head, or any other load that tends to spin in a
reverse direction (backspin) when the motor is de-energized. It blocks starting during the time when the motor
might be rotating in reverse following a trip. Also, this function may be used simply to set idle time (time between
stop and start) before a restart is permitted.
EN MRM4 01/11
Page 267
Summary of Contents for MRM4
Page 1: ...MRM4 HighPROTEC Motor Protection Device Manual DOK HB MRM4E...
Page 3: ...Order Code EN MRM4 01 11 Page 3...
Page 18: ...Important Definitions Page 18 EN MRM4 01 11 41 SG Prot ON 42 SG ON Cmd SG Prot ON SG ON Cmd...
Page 115: ...Navigation Operation Navigation Operation EN MRM4 01 11 Page 115 1 2 3 5 7 6 8 10 9...
Page 162: ...Recorder Name Description I 2 TripCmd Signal Trip Command Page 162 EN MRM4 01 11...