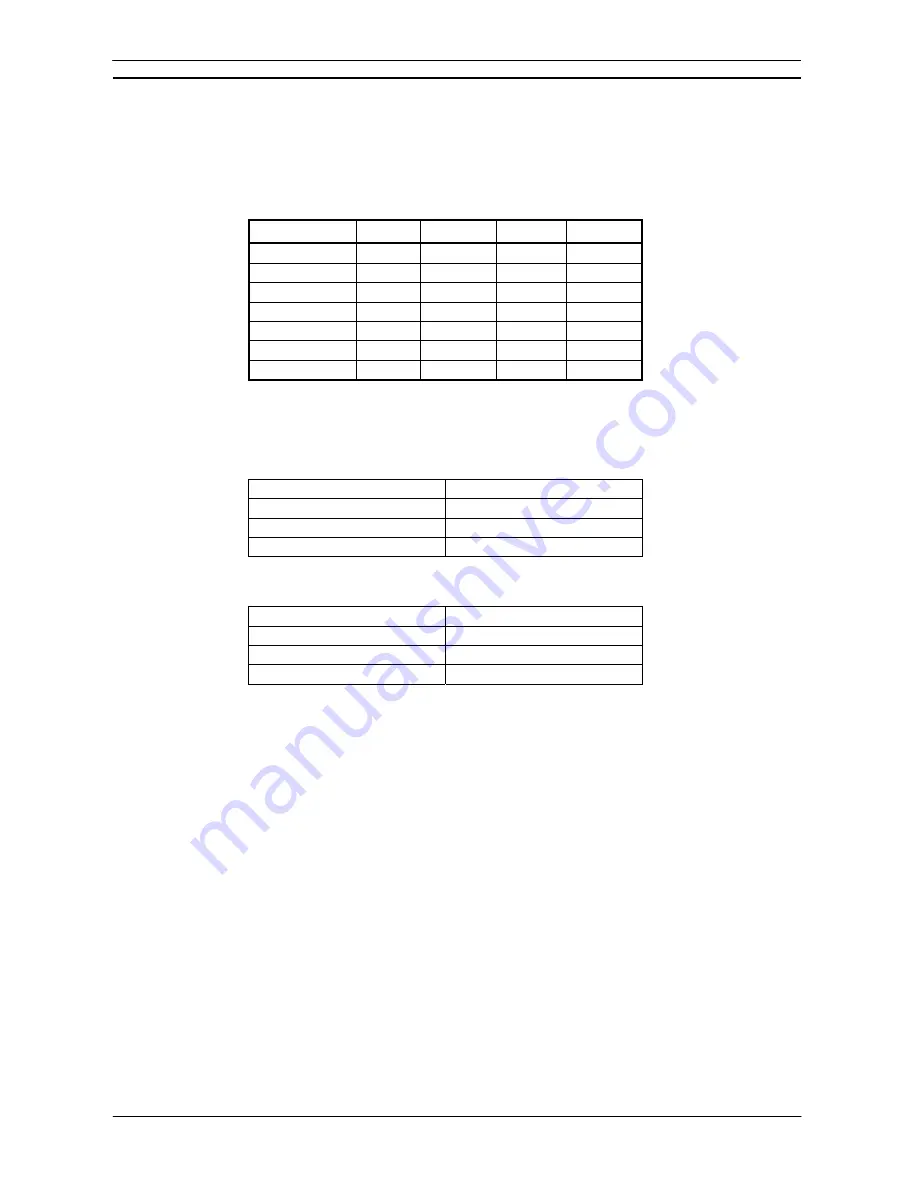
PART 3: CX-Server Runtime
CHAPTER 3 – Communications
OMRON
CX-Server Runtime_Page 20
♦
RS232 connection via a standard serial port on the computer (COM1 etc.) using either CIF01 or CIF02
cable.
The
Driver
tab is similar to that belonging to SYSMAC WAY; however, for some PLCs fixed values are
entered and these cannot be altered (see table below). The SC1-Series PLC Toolbus configuration ensures
successful connection to the PLC every time, independently of the rate specified by the user provided the
Auto
Baud Rate Detection
setting has been checked.
PLC
Fixed
Data Bits
Parity
Stop Bits
CS1/CJ1 Series
Yes
8
None
1
CV/CVM
Series
Yes 8 Odd 1
C Series
No
- - -
- - -
- - -
CPM1/CPM1A
- - -
- - -
- - -
- - -
SRM1/SRM1-V2
- - -
- - -
- - -
- - -
CPM”*/CPM2*-S*
- - -
- - -
- - -
- - -
CQM1/CQM1H
- - -
- - -
- - -
- - -
Serial Networks
When connecting a computer to a serial network of PLCs, each PLC needs to be configured so that it has a
different Unit number. The Unit number for C-series PLCs should be configured as follows:
CPU-mounted Host Link unit:
DIP switches on back of unit
Rack-mounted Host Link unit:
Rotary switches on front of unit
Direct CPU RS232 port:
Internal DM settings
Direct CPU Peripheral port:
Internal DM settings
The Unit number for CV-series PLCs and CS1-series PLCs should be configured as follows:
Rack-mounted Host Link unit:
Unit Setup dialog
Direct CPU RS232 port:
Host Link settings dialog
Direct CPU Peripheral port:
Fixed as Unit 0
Remote SYSBUS/2 Peripheral port:
Fixed as Unit 0
Note
The unit number rotary switches on the top of CV-series SIO units are the unit
number of that Special I/O Unit on that PLC rack and not the Unit number of the PLC
on the serial network.
Network Communications (End Connection)
Each network supports a protocol (or set of rules) determining the manner in which a message is transmitted.
Requests sent by an are formatted into the relevant protocol with each message being validated and prioritised
according to the rules associated with that protocol.
Once a connection has been established between a device and CX-Server, a set of routing rules and tables are
defined which organise the connection between these two processes. The manner of routing depends upon the
protocol (identified with each network type) involved in communicating with the PLC.
The Routing Tables are created via offline table editors but they can also be manipulated online using the CX-
Net Network Configuration tool. These tables, although they vary in format, contain the network, memory and
node address information required to ensure that information is directed correctly across the relevant network.
They also allow the connections to be defined for PLCs which are to act as gateways.
Refer to the PLC Tools
User Manual
Chapter 8 - CX-Net Network Configuration Tool for further information.
When employing SYSMAC LINK, Controller Link and SYSMAC NET networks, each PLC must be
configured on each network to have different Node numbers. If two or more networks are joined together,
Routing Tables must be created and each network given a unique Network number in order to establish
communications between them.
FinsGateway is also needed to establish Controller Link, SYSMAC LINK and SYSMAC Net on NT; refer to the
FinsGateway Manual for further information.
Summary of Contents for Sysmac WS02-CXPC1-EV3
Page 1: ...Cat No W414 E1 01 SYSMAC...
Page 2: ......
Page 3: ...SYSMAC WS02 CXPC1 EV3 CX Programmer Ver 3 1 Operation Manual Revised November 2002...
Page 4: ......
Page 6: ......
Page 7: ...PART1 CX Programmer...
Page 8: ......
Page 24: ......
Page 34: ......
Page 106: ......
Page 130: ......
Page 131: ...PART 2 CX Server PLC Tools...
Page 132: ......
Page 136: ......
Page 158: ......
Page 168: ......
Page 194: ......
Page 206: ......
Page 250: ......
Page 298: ......
Page 304: ......
Page 305: ...PART 3 CX Server Runtime...
Page 306: ......
Page 310: ......
Page 338: ......
Page 344: ......
Page 378: ......
Page 384: ......
Page 388: ......