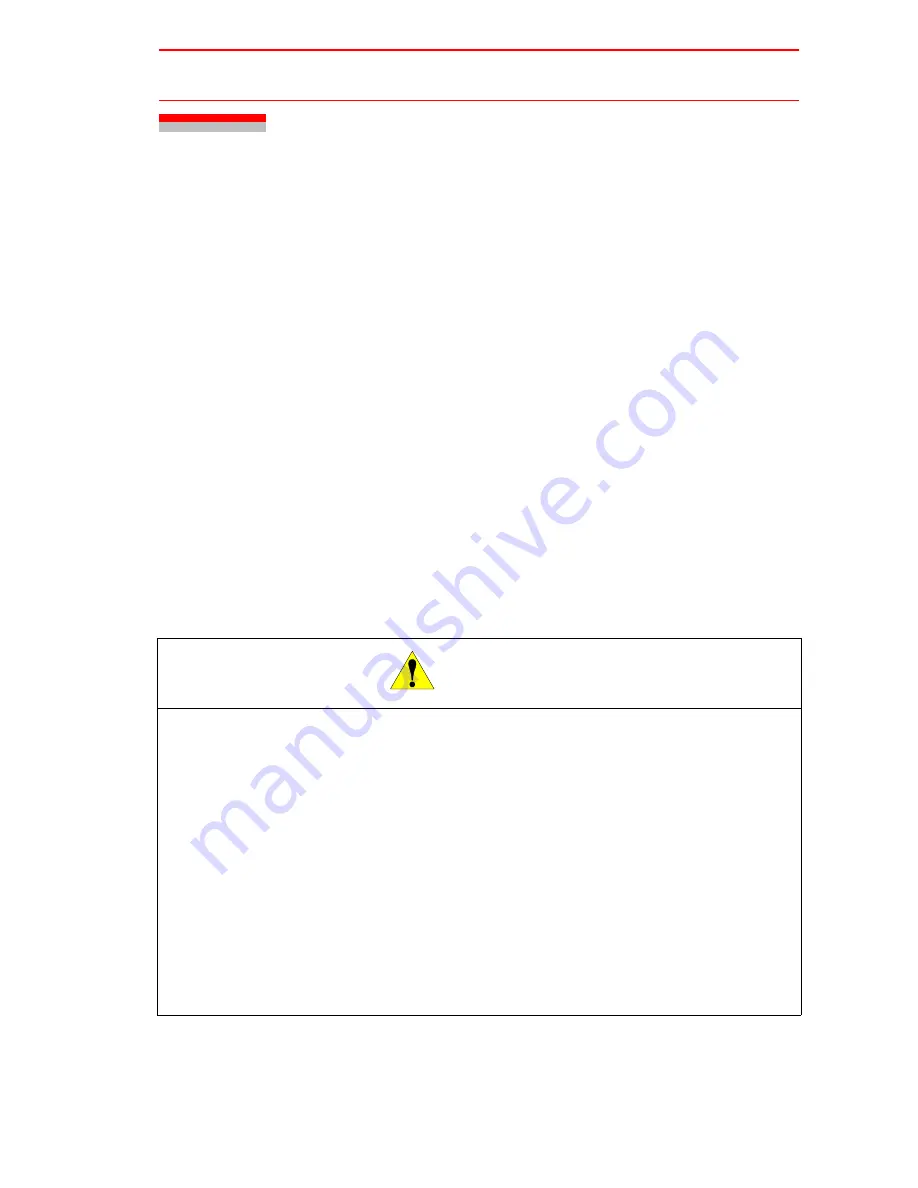
3.11 ARM Control
3-49
3.11
ARM Control
3.11.1
ARM Control
In XRC, the operation performance of the robot which satisfies various demands on the pro-
duction site such as the improvement of the path accuracy and the cycle time shortening is
achieved by adopting the ARM (Advanced Robot Motion) control which Yaskawa Electric Co.,
Ltd. originally developed.
The moment of inertia and the gravity moment etc. of each axis are calculated in the ARM
control, and XRC controls robot motion according to it. It is necessary to set the Robot setup
condition and the tool load information to request these accurately.
The robot setup condition is robot installation angle relative to ground and the weight and a
center of gravity position of the load installed at each part of robot, etc.
The tool load information is weight, a center of gravity position, and moment of inertia at the
center of gravity, of the tool installed at the flange.
It is necessary to set these information correctly to do a better operation control by the ARM
control.
3.11.2
ARM CONTROL Display
In ARM CONTROL display, the robot setup condition etc. are set.
• Set the robot setup condition exactly.
Set the robot setup condition very noting of mistake the unit, the value or the positive and
negative of number.
An appropriate operation control cannot be done, decrease the speed reducer longevity,
or occur the alarm when these are not correctly set.
• Confirm the operation path of robot of each job when you change set-
ting.
Set the robot setup condition when you basically set up the robot.
Confirm the operation path of robot of each job afterwards when you change the setting
unavoidably.
Injury or damage to machinery may result by collision between tool and jig because the
operation path might be changed slightly when the setting about the ARM control is
changed.
C A U T I O N
Summary of Contents for PX2750
Page 2: ......
Page 4: ...PX2850 PX2750 Manipulator Manual ii MOTOMAN NOTES...
Page 20: ...viii...
Page 24: ...xii...
Page 40: ...1 7 Notes on MOTOMAN Disposal 1 16...
Page 58: ...4 3 Connection Methods 4 12...
Page 66: ...6 1 Movement of the Axes 6 4...
Page 72: ...8 2...
Page 73: ......
Page 99: ......
Page 100: ......
Page 282: ...2 8 General I O Signal Assignment 2 72...
Page 318: ...4 4 Recommended Spare Parts 4 30...
Page 333: ...xiv...
Page 334: ...Setup Diagnosis...
Page 335: ......
Page 337: ...1 2...
Page 345: ...2 1 Protection Through Security Mode Settings 2 8...
Page 443: ...3 17 File Initialize 3 98...
Page 465: ...4 2 Addition of Base and Station Axis 4 22...
Page 483: ...5 6 Position Data When Power is Turned ON OFF 5 18...
Page 484: ...Hardware...
Page 485: ......
Page 495: ...6 4 Equipment Configuration 6 10...
Page 497: ...7 2...
Page 505: ...8 8 Open Phase Check 8 8...
Page 525: ...9 4 Recommended Spare Parts 9 20...
Page 526: ...Alarm Error...
Page 527: ......
Page 573: ......
Page 574: ......
Page 575: ......
Page 576: ......
Page 577: ......
Page 578: ......
Page 579: ......
Page 580: ......
Page 581: ......
Page 582: ......
Page 583: ......
Page 584: ......
Page 585: ......
Page 586: ......
Page 587: ......
Page 588: ......
Page 589: ......
Page 590: ......
Page 591: ......
Page 592: ......
Page 593: ......
Page 594: ......
Page 595: ......
Page 596: ......
Page 597: ......
Page 598: ......
Page 599: ......
Page 600: ......
Page 601: ......
Page 602: ......
Page 603: ......
Page 604: ......
Page 605: ......
Page 606: ......
Page 607: ......
Page 608: ......
Page 609: ......
Page 610: ......
Page 611: ......