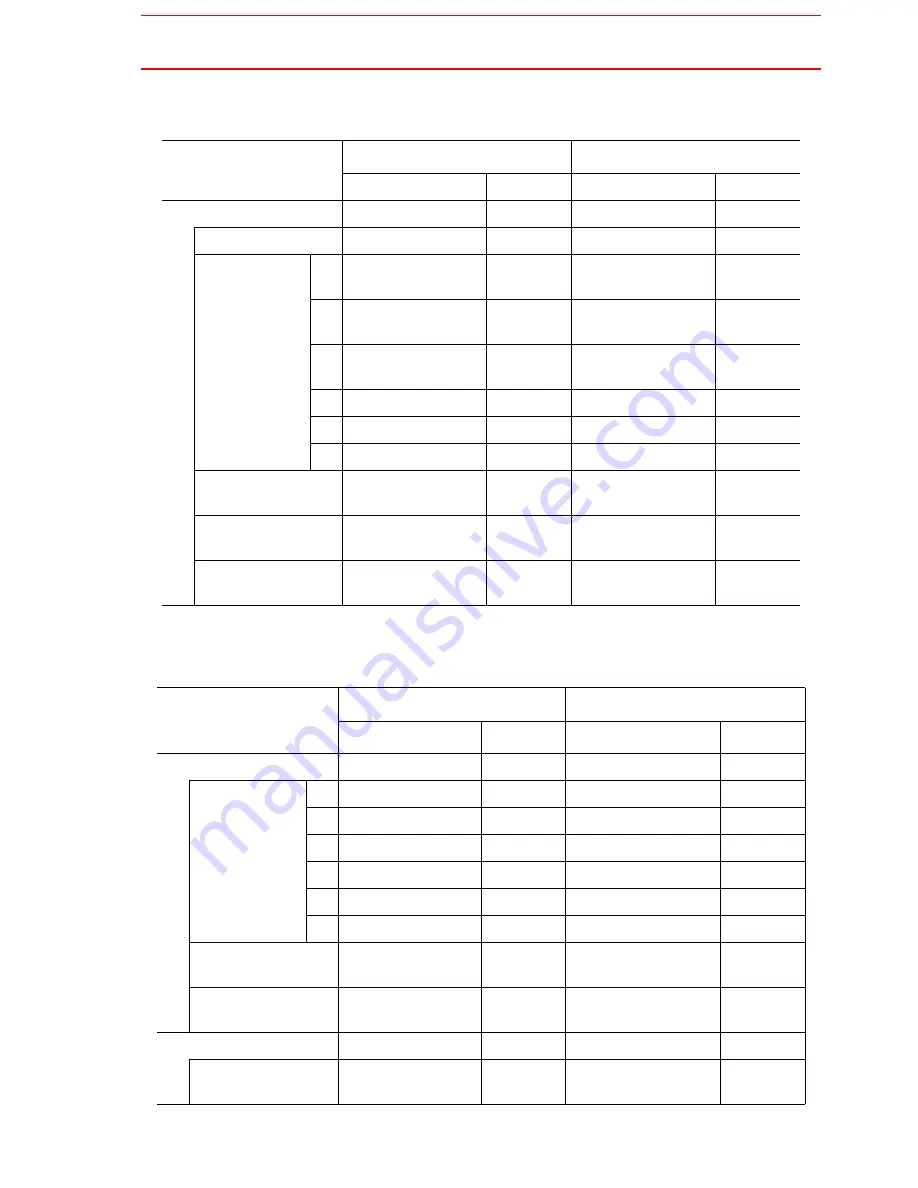
2.6 SERVOPACK
2-31
SERVOPACK Configuration (Small Capacity Type)
Component
SK16X
UP20
Type
Capacity
Type
Capacity
SERVOPACK
CACR-SK16AAC
-
CACR-UP20AAA
-
Converter
JUSP-ACP05JAA
5A
JUSP-ACP05JAA
5A
Amplifier
S
JUSP-
WS10AAY17
1kW
JUSP-WS10AA
1kW
L
JUSP-
WS10AAY17
1kW
JUSP-
WS20AAY22
2kW
U
JUSP-
WS10AAY17
1kW
JUSP-
WS10AAY17
1kW
R
JUSP-WS02AA
200W
JUSP-WS02AA
200W
B
JUSP-WS02AA
200W
JUSP-WS02AA
200W
T
JUSP-WS02AA
200W
JUSP-WS02AA
200W
Servo control
curcuit board
JASP-WRCA01
-
JASP-WRCA01
-
Servo control
power supply
JUSP-RCP01AA
#
-
JUSP-RCP01AA
#
-
Speed monitor
board
JANCD-XFC01
-
JANCD-XFC01
-
SERVOPACK Configuration (Medium Capacity Type)
Component
SK45X
SK16MX
Type
Capacity
Type
Capacity
SERVOPACK
CACR-SK45AAB
-
CACR-SK16MAAB
-
Amplifier
S
JUSP-WS30AA
3kW
JUSP-WS30AA
3kW
L
JUSP-WS20AA
2kW
JUSP-WS20AA
2kW
U
JUSP-WS20AA
2kW
JUSP-WS20AA
2kW
R
JUSP-WS10AA
1kW
JUSP-WS02AA
200W
B
JUSP-WS10AA
1kW
JUSP-WS02AA
200W
T
JUSP-WS10AA
1kW
JUSP-WS02AA
200W
Servo control
curcuit board
JASP-WRCA01
-
JASP-WRCA01
-
Speed monitor
board
JANCD-XFC01
-
JANCD-XFC01
-
Converter
JUSP-ACP25JAA
25A
JUSP-ACP25JAA
25A
Servo control
power supply
JUSP-
RCP01AA
#
-
JUSP-RCP01AA
#
-
Summary of Contents for PX2750
Page 2: ......
Page 4: ...PX2850 PX2750 Manipulator Manual ii MOTOMAN NOTES...
Page 20: ...viii...
Page 24: ...xii...
Page 40: ...1 7 Notes on MOTOMAN Disposal 1 16...
Page 58: ...4 3 Connection Methods 4 12...
Page 66: ...6 1 Movement of the Axes 6 4...
Page 72: ...8 2...
Page 73: ......
Page 99: ......
Page 100: ......
Page 282: ...2 8 General I O Signal Assignment 2 72...
Page 318: ...4 4 Recommended Spare Parts 4 30...
Page 333: ...xiv...
Page 334: ...Setup Diagnosis...
Page 335: ......
Page 337: ...1 2...
Page 345: ...2 1 Protection Through Security Mode Settings 2 8...
Page 443: ...3 17 File Initialize 3 98...
Page 465: ...4 2 Addition of Base and Station Axis 4 22...
Page 483: ...5 6 Position Data When Power is Turned ON OFF 5 18...
Page 484: ...Hardware...
Page 485: ......
Page 495: ...6 4 Equipment Configuration 6 10...
Page 497: ...7 2...
Page 505: ...8 8 Open Phase Check 8 8...
Page 525: ...9 4 Recommended Spare Parts 9 20...
Page 526: ...Alarm Error...
Page 527: ......
Page 573: ......
Page 574: ......
Page 575: ......
Page 576: ......
Page 577: ......
Page 578: ......
Page 579: ......
Page 580: ......
Page 581: ......
Page 582: ......
Page 583: ......
Page 584: ......
Page 585: ......
Page 586: ......
Page 587: ......
Page 588: ......
Page 589: ......
Page 590: ......
Page 591: ......
Page 592: ......
Page 593: ......
Page 594: ......
Page 595: ......
Page 596: ......
Page 597: ......
Page 598: ......
Page 599: ......
Page 600: ......
Page 601: ......
Page 602: ......
Page 603: ......
Page 604: ......
Page 605: ......
Page 606: ......
Page 607: ......
Page 608: ......
Page 609: ......
Page 610: ......
Page 611: ......