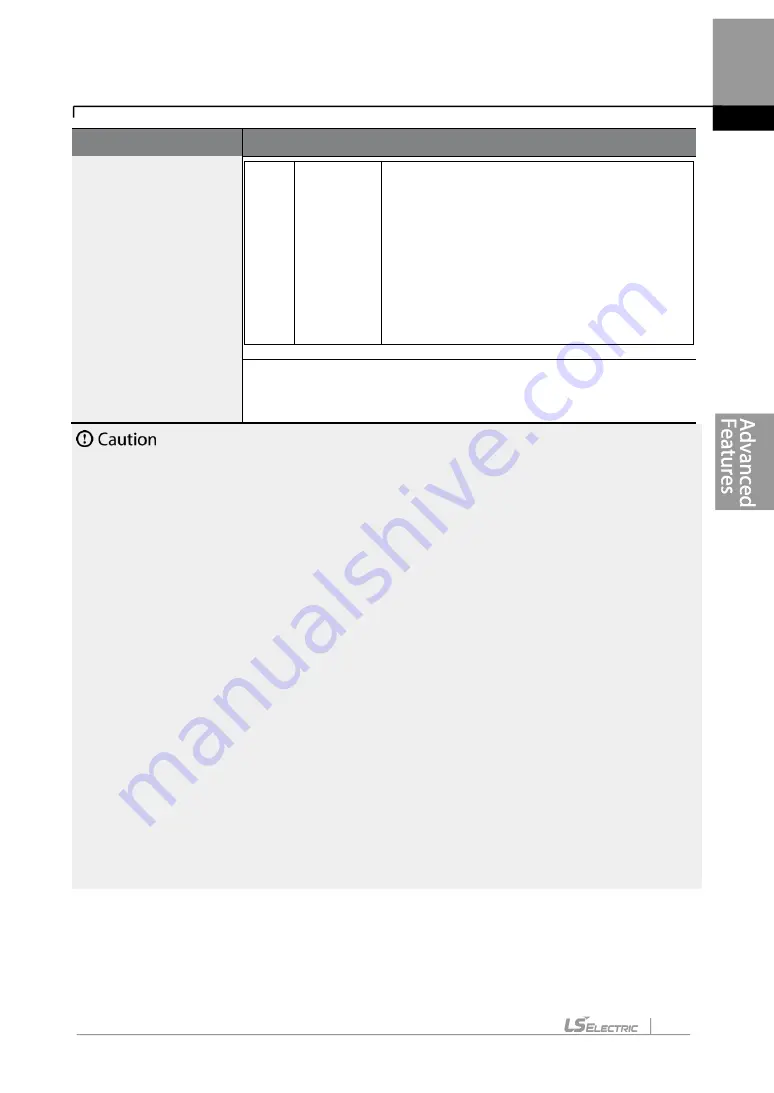
213
Learning Advanced Features
Code
Description
2
All (static
type)
Measures all parameters while the motor is
in the stopped position, including stator
resistance (Rs), no-load current (Noload
Curr), rotor time constant (Tr), etc. Since the
motor is not rotating while the parameters
are measured, the measurements are not
affected when the load is connected to the
motor spindle. However, when measuring
parameters, do not rotate the motor spindle
on the load side.
BAS-14 Noload Curr,
BAS-21 Rs
–BAS-24 Tr
Displays motor parameters measured by auto tuning. For
parameters that are not included in the auto tuning measurement
list, the default setting will be displayed.
•
Perform auto tuning ONLY after the motor has completely stopped running.
•
Auto tuning operates when the inverter’s auto mode is off.
•
Before you run auto tuning, check the motor pole number, rated slip, rated current, rated
volta
ge, and efficiency on the motor’s rating plate and enter the data. The default
parameter setting is used for values that are not entered.
•
When measuring all parameters after selecting 2 ( All-static type) at BAS-20: compared
with rotation type auto tuning where parameters are measured while the motor is rotating,
parameter values measured with static auto tuning may be less accurate. Inaccuracy of the
measured parameters may degrade the performance of operations. Therefore, run static-
type auto tuning by selecting 2 (All) only when the motor cannot be rotated (when gearing
and belts cannot be separated easily, or when the motor cannot be separated mechanically
from the load).
•
If auto tuning operates without wiring the motor,
‘Rs Tune Err’ or ‘Lsig Tune Err’ warning
messages are displayed. It can be reset if you press
‘STOP/RESET’ button of the keypad.
5.22 Time Event Scheduling
Summary of Contents for LSLV-H100 Series
Page 17: ...Preparing the Installation 4 37 90 kW 3 Phase ...
Page 18: ...Preparing the Installation 5 110 132 kW 3 Phase ...
Page 19: ...Preparing the Installation 6 160 185 kW 3 Phase ...
Page 20: ...Preparing the Installation 7 220 250 kW 3 Phase ...
Page 21: ...Preparing the Installation 8 315 400 kW 3 Phase ...
Page 22: ...Preparing the Installation 9 500 kW 3 Phase ...
Page 35: ...Installing the Inverter 22 ...
Page 50: ...37 Installing the Inverter Input and Output Control Terminal Block Wiring Diagram ...
Page 104: ...91 Learning Basic Features 0 10 V Input Voltage Setting Details V1 Quantizing ...
Page 181: ...168 Learning Advanced Features PID Command Block ...
Page 182: ...169 Learning Advanced Features ...
Page 183: ...170 Learning Advanced Features PID Feedback Block ...
Page 184: ...171 Learning Advanced Features PID Output Block ...
Page 185: ...172 Learning Advanced Features PID Output Mode Block ...
Page 198: ...185 Learning Advanced Features EPID1 Control block ...
Page 199: ...186 Learning Advanced Features EPID2 Control block ...
Page 220: ...207 Learning Advanced Features ...
Page 235: ...222 Learning Advanced Features The Time Chart for the Exception Day ...
Page 506: ...Table of Functions 493 ...
Page 520: ...Table of Functions 507 8 16 4 Cooling Tower MC4 Group ...
Page 549: ...Troubleshooting 536 ...
Page 569: ...Technical Specification 556 11 3 External Dimensions 0 75 30 kW 3 phase 37 90 kW 3 phase ...
Page 570: ...Technical Specification 557 110 185 kW 3 phase ...
Page 601: ...588 ...
Page 602: ...589 ...
Page 603: ...590 ...