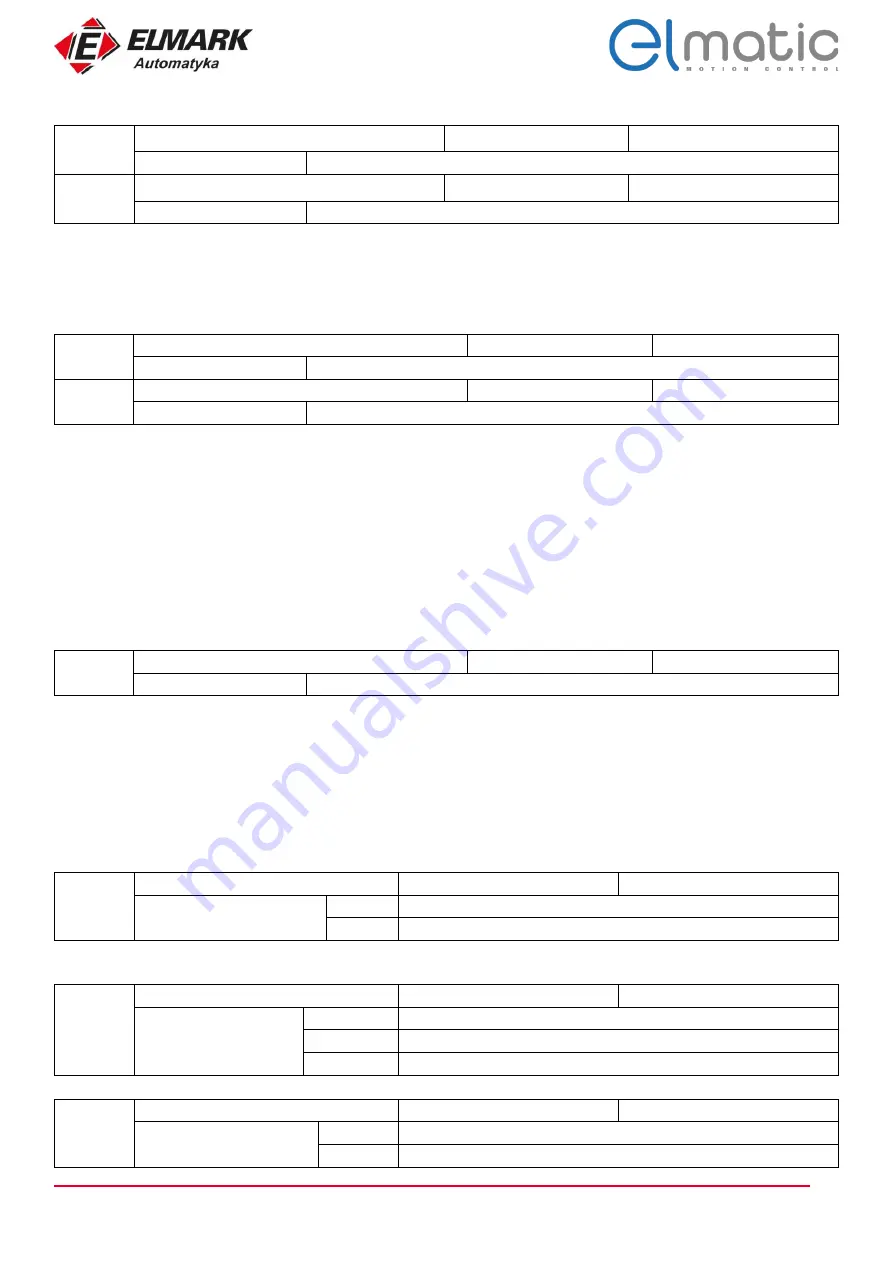
81
Elmark Automatyka S.A.
ul. Niemcewicza 76, 05-075 Warszawa, tel. (+48) 22 773 79 37; [email protected]; www.elmark.com.pl
NIP: 5252072585; KRS: 0000803828, Sąd Rejonowy dla M-St. Warszawy, XIV Wydział Gosp. KRS; Kapitał Zakładowy 525.000 zł, w pełni opłacony
When the torque setting using 1 ~ 7, communication, analog input and pulse input. The data format is -100.00% to 100.00%. 100%
corresponds to the value of C0.03.
C0.05
Forward maximum frequency in torque control
Default
50.00Hz
Setting Range
0.00 ~ maximum frequency
C0.06
Reverse maximum frequency in torque control
Default
50.00Hz
Setting Range
0.00 ~ maximum frequency
This two parameters are used to set the maximum frequency in forward or reverse rotation in torque control mode.
In torque control, if the load torque is smaller than the motor output torque, the motor's rotational speed will rise continuously.
To avoid runaway of the mechanical system, the motor maximum rotating speed must be limited in torque control.
You can implement continuous change of the maximum frequency in torque control dynamically by controlling the frequency
upper limit.
C0.07
Acceleration time in torque control
Default
0.00s
Setting Range
0.00s ~ 650.00s
C0.08
Deceleration time in torque control
Default
0.00s
Setting Range
0.00s ~ 650.00s
In torque control, the difference between the motor output torque and the load torque determines the speed change rate of the
motor and load. The motor rotational speed may change quickly and this will result in noise or too large mechanical stress. The
setting of acceleration/deceleration time in torque control makes the motor rotational speed change smoothly.
However, in applications requiring rapid torque response, set the acceleration/deceleration time in torque control to 0.00s. For
example, two AC drives are connected to drive the same load. To balance the load allocation, set one AC drive as master in speed
control and the other as slave in torque control. The slave receives the master's output torque as the torque command and must
follow the master rapidly. In this case, the acceleration/deceleration time of the slave in torque control is set to 0.0s.
Group C5: Control Optimization Parameters
C5.00
PWM switchover frequency upper limit
Default
12.00Hz
Setting Range
0.00Hz ~ 15Hz
This parameter is valid only for V/F control.
It is used to determine the wave modulation mode in V/F control of asynchronous motor.
If the frequency is lower than the value of this parameter, the waveform is 7-segment continuous modulation. If the frequency is
higher than the value of this parameter, the waveform is 5-segment intermittent modulation.
The 7-segment continuous modulation causes more loss to switches of the AC drive but smaller current ripple. The 5-segment
intermittent modulation causes less loss to switches of the AC drive but larger current ripple. This may lead to motor running
instability at high frequency. Do not modify this parameter generally.
For instability of V/F control, refer to parameter P4.11. For loss to AC drive and temperature rise, refer to parameter P0.17.
C5.01
PWM modulation mode
Default
0
Setting Range
0
Asynchronous modulation
1
Synchronous modulation
Only V/F control is effective. asynchronous modulation is used when the output frequency is high( over 100HZ),conducive to the
quality of the output voltage.
C5.02
Dead compensation way
Default
1
Setting Range
0
No compensation
1
compensation mode 1
2
compensation mode 2
It doesn't have to modify generally.
C5.03
Random PWM depth
Default
0
Selling Range
0
Random PWM invalid
1-10
PWM carrier frequency random depth
Summary of Contents for elmatic ED2000
Page 1: ......