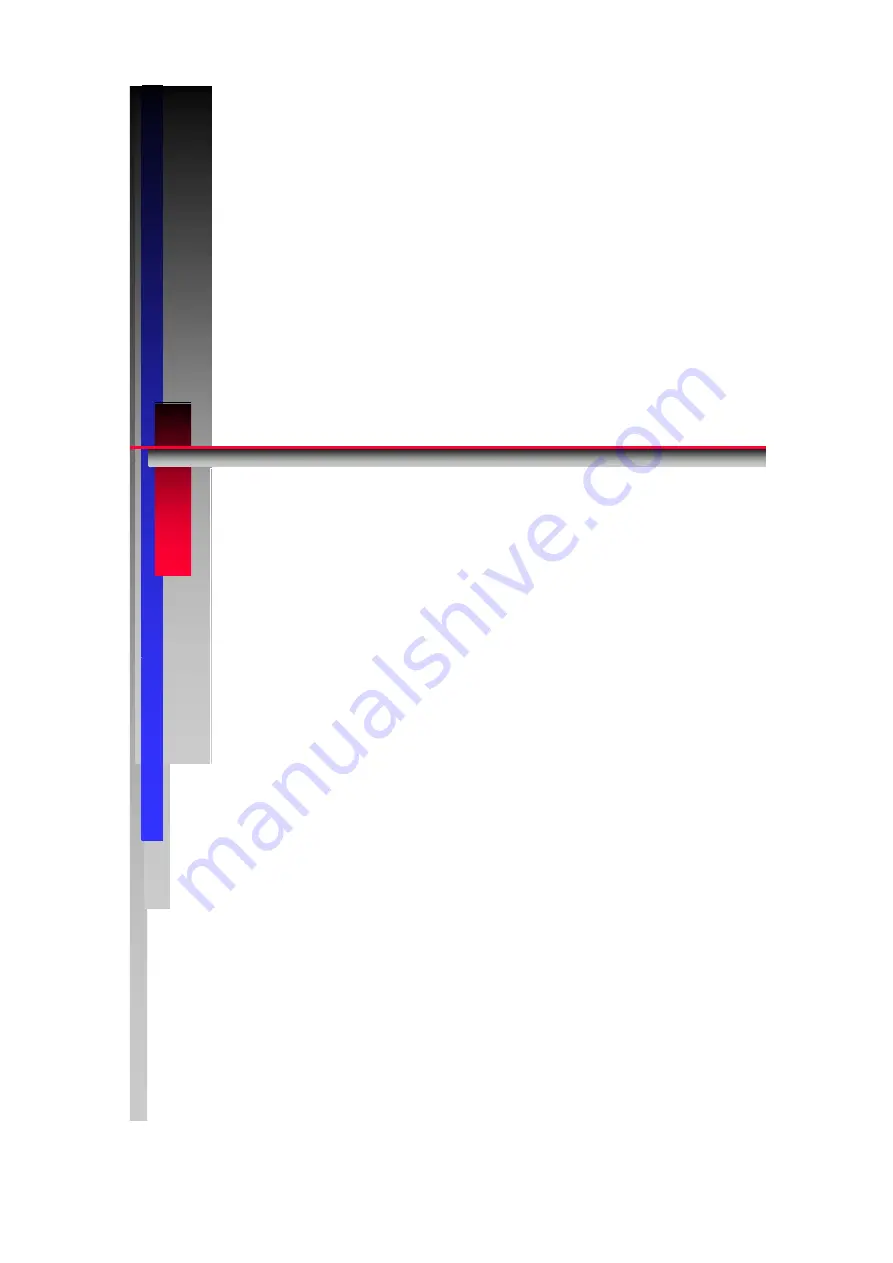
Confidential
C
C
X
X
D
D
I
I
-
-
1
1
S
S
y
y
s
s
t
t
e
e
m
m
C
C
X
X
D
D
I
I
-
-
3
3
1
1
S
S
e
e
r
r
v
v
i
i
c
c
e
e
M
M
a
a
n
n
u
u
a
a
l
l
V
V
e
e
r
r
.
.
0
0
6
6
M
M
e
e
d
d
i
i
c
c
a
a
l
l
P
P
r
r
o
o
d
d
u
u
c
c
t
t
s
s
T
T
e
e
c
c
h
h
n
n
i
i
c
c
a
a
l
l
S
S
e
e
r
r
v
v
i
i
c
c
e
e
D
D
e
e
p
p
t
t
C
C
o
o
p
p
y
y
r
r
i
i
g
g
h
h
t
t
b
b
y
y
C
C
a
a
n
n
o
o
n
n
J
J
u
u
n
n
.
.
2
2
0
0
0
0
9
9
Summary of Contents for CXDI-31
Page 11: ...Labels and Markings Rear iii ...
Page 14: ...Labels and Markings Rear vi ...
Page 18: ......
Page 20: ......
Page 34: ...2 Installation Manual No 7 No Name E O power connector guard Name Remarks Remarks Table 3 8 ...
Page 46: ...2 Installation Manual 20 2 Set up on the left side Screw x 4 on the E O box Fig 9 Fig 10 ...
Page 151: ...2 Installation Manual 125 8 1 3 Storage Box Fig 3 ...
Page 152: ...2 Installation Manual 126 8 2 Option 8 2 1 Grid L 21 8mm 4 1 22 3mm 8 1 22 5mm 10 1 Fig 4 ...
Page 157: ...3 CXDI 31 Imaging Unit 1 1 Unit Diagram Fig 1 DC DC Conversion Board ...
Page 184: ......
Page 186: ......
Page 187: ...4 CXDI 31 E O Box 1 CXDI 31 E O Box Unit Diagram Fig 1 1 ...
Page 198: ......