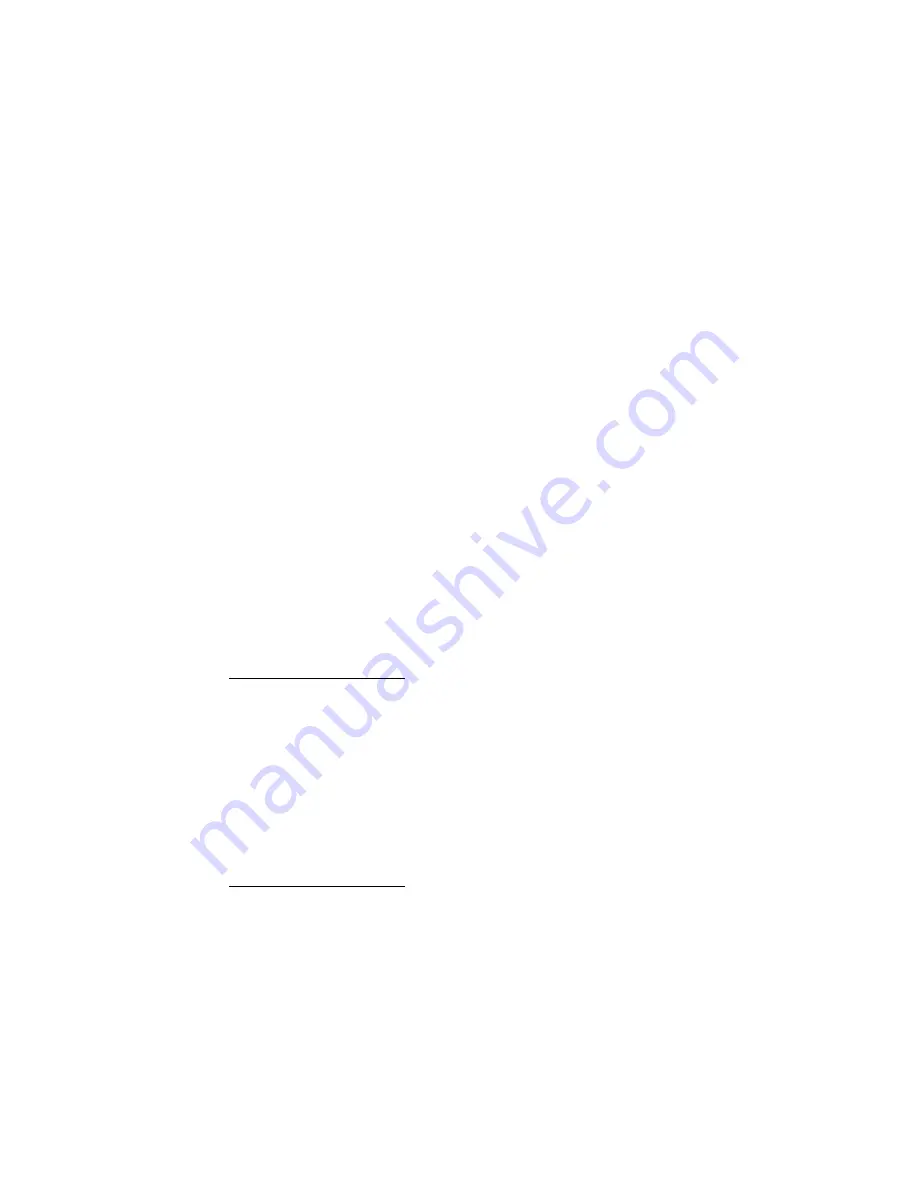
- 162 -
BASIC OPERATION
The external lead axis can, by programming, become the basic source for motion control of a
second follower axis. Most of the capabilities of the IOM and PCM-1 are available with one
additional input function (JOB SYNC) added and two additional outputs (AT SYNC) and
(SYNC FAULT) added. The basis of operation is determined by the relationship of the external
lead encoder, or drive, to the follower axis drive motor. The relationship is established based on
the programmable ratio of follower axis turns to lead axis turns over a programmable sync ratio
range of (.125 to 20). For example, if the user programs a sync ratio of “2”, what is being asked
is for two turns of the follower axis for every one turn of the lead.
The SCS-2 sync encoder is a two channel amplified sine wave encoder. Each of the channels has
1000 lines. The PCM-2 inputs are A, A {compliment}, B and B {compliment}. Quadrature
encoding of these two signals produces a 4 times result so that one revolution of the sync
encoder produces the equivalent of 4000 counts/steps per revolution. For resolving distance
counting from the sync encoder, 4000 counts per turn becomes important.
The base number system used for the digital drive is binary and 12 bits. Resolution is one part in
4096. Since this number may be difficult to work with because of units, the drive electronics
allow for a conversion of this to any number from 200 to 25,000 with the default being 4000.
This is provided as a means to achieve meaningful units. When a follower axis is receiving its
synchronization source from a digital drive lead axis, then the count source becomes the binary
4096 counts per turn.
There are mathematical limitations and hardware limitations to the precision of the ratio feature.
An example is provided. The drive uses a term SR1. To compute the relationship (SR1 can be
any whole integer from 200 to 32,000). The PCX software provides a user friendly conversion
by asking for the number of follower turns wanted to equal lead turns.
N
(TURNS)
= SR1
N = 4000 if lead count source is an encoder
= 4096 if lead count source is another digital drive
TURNS is the number you enter from PCX.
Consider you enter:
3.000
4000
3
(Assume encoder for N)
= 1333 1/3 = SR1
But SR1 must be a whole integer between a range of 200 to 32,000 so PCX will use 1333 for the
value going to the drive for SR1 and replace the value 3.000 you programmed with 3.0007502 ->
{infinity}. PCX will also inform you that a perfect match does not exist. The number 4000 in
the above example is a constant based on the SCS-2 encoder. This constant changes to 4096 if
you select the lead axis to be a digital drive.
Some Application Examples
Artisan Technology Group - Quality Instrumentation ... Guaranteed | (888) 88-SOURCE | www.artisantg.com