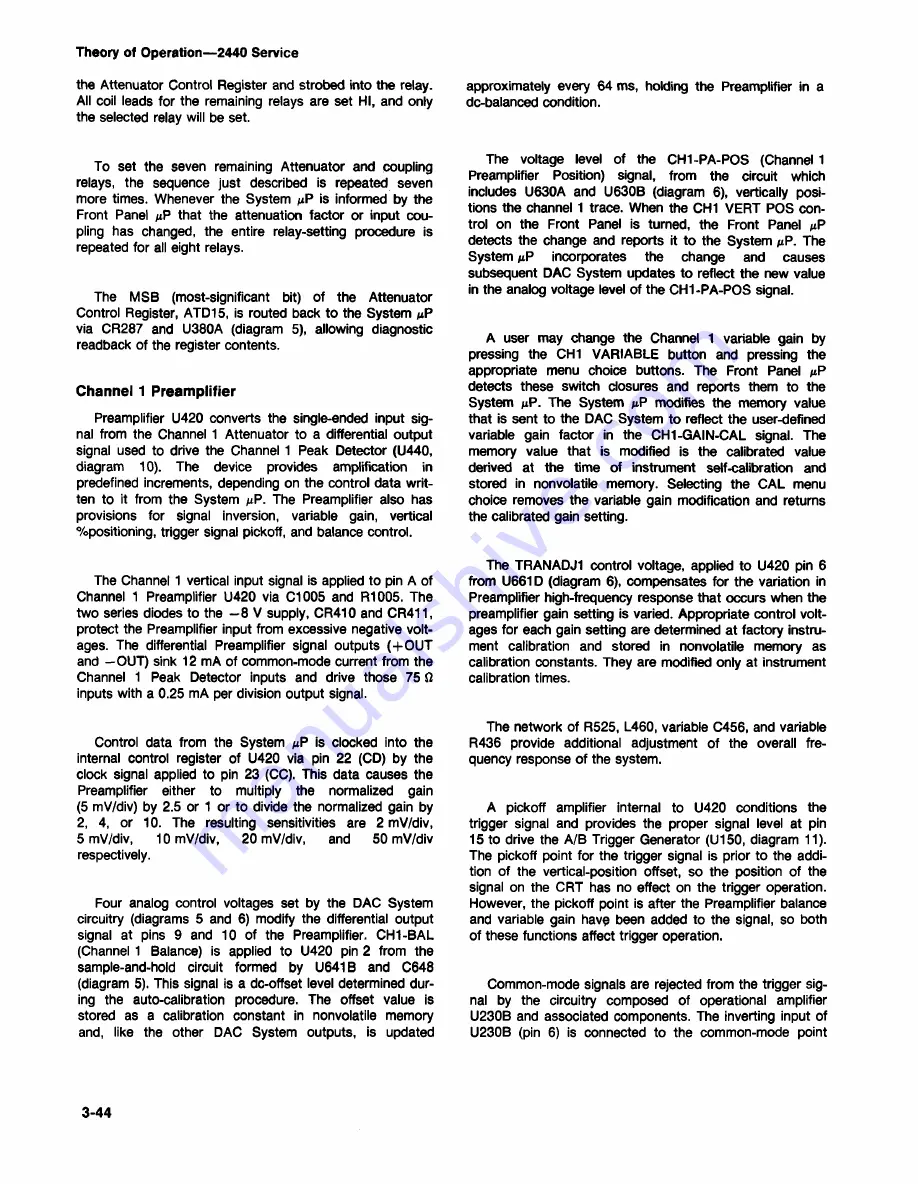
Theory of Operation— 2440 Service
the Attenuator Control Register and strobed into the relay.
All coil leads for the remaining relays are set HI, and only
the selected relay will be set.
To set the seven remaining Attenuator and coupling
relays, the sequence just described is repeated seven
more times. Whenever the System /iP is informed by the
Front Panel
pP
that the attenuation factor or input cou
pling has changed, the entire relay-setting procedure is
repeated for all eight relays.
The M SB (most-significant bit) of the Attenuator
Control Register, ATD15, is routed back to the System
nP
via CR287 and U380A (diagram 5), allowing diagnostic
readback of the register contents.
C hannel 1 Pream plifier
Preamplifier U420 converts the single-ended input sig
nal from the Channel 1 Attenuator to a differential output
signal used to drive the Channel 1 Peak Detector (U440,
diagram
10).
The
device
provides
amplification
in
predefined increments, depending on the control data writ
ten to it from the System juP. The Preamplifier also has
provisions for signal inversion, variable gain, vertical
%positioning, trigger signal pickoff, and balance control.
The Channel 1 vertical input signal is applied to pin A of
Channel 1 Preamplifier U420 via C l 005 and R1005. The
two series diodes to the - 8 V supply, CR410 and CR411,
protect the Preamplifier input from excessive negative volt
ages. The differential Preamplifier signal outputs (+ O U T
and —OUT) sink 12 mA of common-mode current from the
Channel 1 Peak Detector inputs and drive those 7512
inputs with a 0.25 mA per division output signal.
Control data from the System
nP
is clocked into the
internal control register of U420 via pin 22 (CD) by the
clock signal applied to pin 23 (CC). This data causes the
Preamplifier
either
to
multiply the
normalized
gain
(5 mV/div) by 2.5 or 1 or to divide the normalized gain by
2, 4, or 10. The resulting sensitivities are 2 mV/div,
5 mV/div,
10 mV/div,
20 mV/div,
and
50 mV/div
respectively.
Four analog control voltages set by the DAC System
circuitry (diagrams 5 and 6) modify the differential output
signal at pins 9 and 10 of the Preamplifier. CH1-BAL
(Channel 1 Balance) is applied to U420 pin 2 from the
sample-and-hold circuit formed by U641B and C648
(diagram 5). This signal is a dc-offset level determined dur
ing the auto-calibration procedure. The offset value is
stored as a calibration constant in nonvolatile memory
and, like the other DAC System outputs, is updated
approximately every 64 ms, holding the Preamplifier in a
dc-balanced condition.
The voltage level of the CH1-PA-POS (Channel 1
Preamplifier Position) signal, from the circuit which
includes U630A and U630B (diagram 6), vertically posi
tions the channel 1 trace. When the C H I VER T POS con
trol on the Front Panel is turned, the Front Panel
nP
detects the change and reports it to the System
nP.
The
System
nP
incorporates
the
change
and
causes
subsequent DAC System updates to reflect the new value
in the analog voltage level of the CH1-PA-POS signal.
A user may change the Channel 1 variable gain by
pressing the C H I VARIABLE button and pressing the
appropriate menu choice buttons. The Front Panel
fiP
detects these switch closures and reports them to the
System
nP.
The System
tiP
modifies the memory value
that is sent to the DAC System to reflect the user-defined
variable gain factor in the CH1-GAIN-CAL signal. The
memory value that is modified is the calibrated value
derived at the time of instrument self-calibration and
stored in nonvolatile memory. Selecting the CAL menu
choice removes the variable gain modification and returns
the calibrated gain setting.
The TRANADJ1 control voltage, applied to U420 pin 6
from U661D (diagram 6), compensates for the variation in
Preamplifier high-frequency response that occurs when the
preamplifier gain setting is varied. Appropriate control volt
ages for each gain setting are determined at factory instru
ment calibration and stored in nonvolatile memory as
calibration constants. They are modified only at instrument
calibration times.
The network of R525, L460, variable C456, and variable
R436 provide additional adjustment of the overall fre
quency response of the system.
A pickoff amplifier internal to U420 conditions the
trigger signal and provides the proper signal level at pin
15 to drive the A/B Trigger Generator (U150, diagram 11).
The pickoff point for the trigger signal is prior to the addi
tion of the vertical-position offset, so the position of the
signal on the CRT has no effect on the trigger operation.
However, the pickoff point is after the Preamplifier balance
and variable gain have been added to the signal, so both
of these functions affect trigger operation.
Common-mode signals are rejected from the trigger sig
nal by the circuitry composed of operational amplifier
U230B and associated components. The inverting input of
U230B (pin 6) is connected to the common-mode point
3 -4 4
Summary of Contents for 2440
Page 4: ......
Page 12: ......
Page 38: ......
Page 91: ...Theory of Operation 2440 Service 3 49 Figure 3 5 Simplified CCD architecture ...
Page 120: ...Theory of Operation 2440 Service Figure 3 10 DC Restorer 3 78 ...
Page 130: ...Theory of Operation 2440 Service 3 88 ...
Page 136: ...Theory of Operation 2440 Service Figure 3 15 PWM Regulator and Inverter 3 94 ...
Page 138: ...Theory of Operation 2440 Service Figure 3 16 PWM switching waveforms 3 96 ...
Page 208: ......
Page 322: ......
Page 419: ......
Page 423: ...2440 Service Figure 9 4b 2440 Block diagram part 2 6330 27 BLOCK DIAGRAM PART 2 ...
Page 427: ......
Page 428: ...2440 Service WAVEFORMS FOR DIAGRAM 1 6 2 8 5 3 2 ...
Page 429: ......
Page 432: ...2440 Service WAVEFORMS FOR DIAGRAM 2 BUS ISOLATED 6 6 0 3 4 9 ...
Page 433: ...WAVEFORMS FOR DIAGRAM 2 ...
Page 439: ......
Page 445: ......
Page 450: ...2440 Service WAVEFORMS FOR DIAGRAM 8 6603 27 ...
Page 455: ...W A V EFO R M S FOR D IAG RAM 11 WAVEFORMS FOR DIAGRAM 11 6603 29 ...
Page 458: ...WAVEFORMS FOR DIAGRAM 12 ...
Page 463: ...WAVEFORMS FOR DIAGRAM 14 ...
Page 471: ... C N i u i t e x r 4 j u J l i 1 i 6 28 5 44 WAVEFORMS FOR DIAGRAM 18 ...
Page 476: ...WAVEFORMS FOR DIAGRAM 20 ...
Page 490: ...YES ...
Page 492: ......
Page 494: ......
Page 499: ...YES ...
Page 501: ......
Page 502: ...2440 Service FIG 1 C A B IN E T ...
Page 503: ......
Page 510: ...2440 Service SISSVHO Z Old ...
Page 511: ......
Page 512: ...A12 2440 Service F IG 3 C IR C U IT BOARDS ...
Page 513: ......
Page 517: ...10 16 R E V J U L 1993 Replaceable Mechanical Parts ...
Page 518: ...2440 Service ...
Page 519: ...FIG 4 L V H V PWR SUPPLY ...
Page 520: ...FIG 5 ACCESSORIES 2440 Service ...
Page 521: ......
Page 523: ......
Page 529: ......
Page 530: ......
Page 531: ......