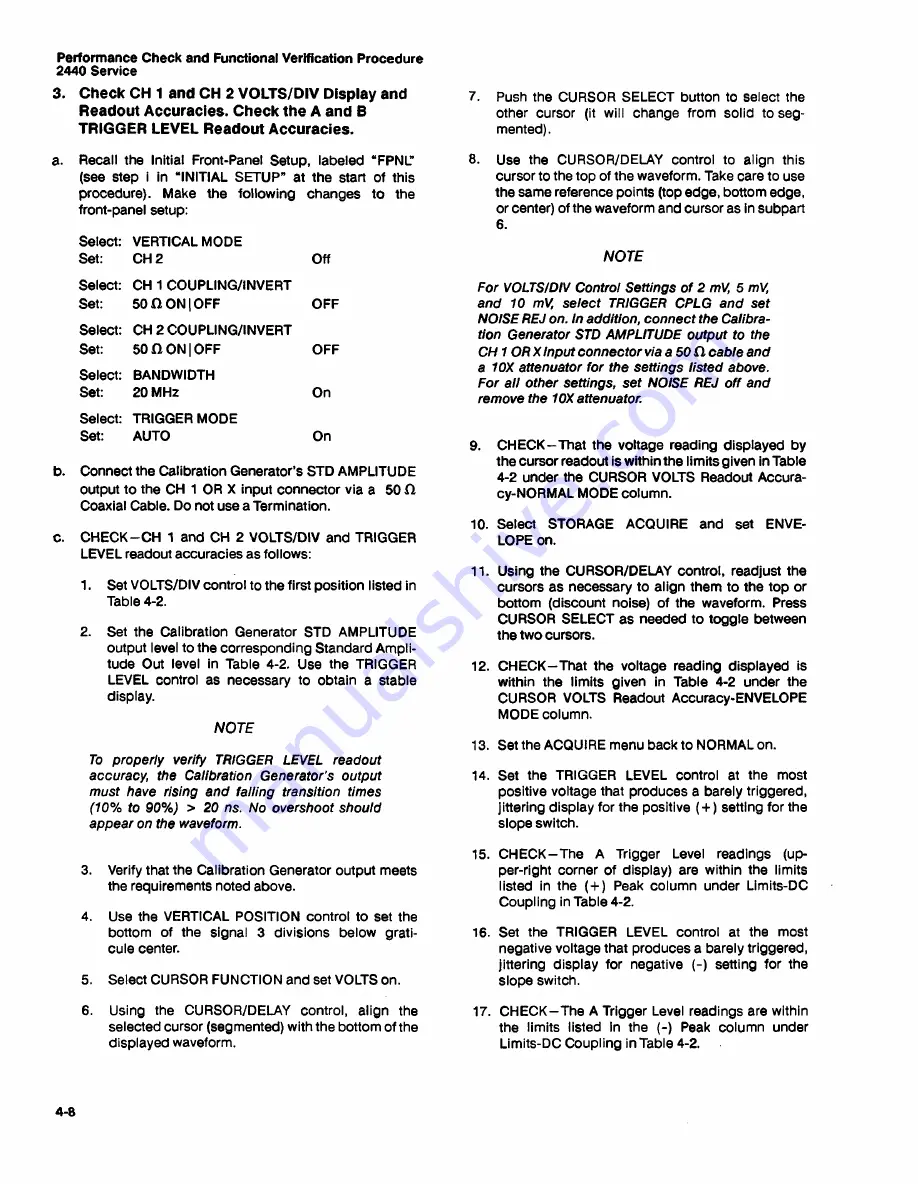
Performance Check and Functional Verification Procedure
2440 Service
3. Check CH 1 and CH 2 VOLTS/DIV Display and
Readout Accuracies. Check the A and B
TRIGGER LEVEL Readout Accuracies.
a.
Recall the Initial Front-Panel Setup, labeled “FPNL”
(see step i in “INITIAL S E T U P ” at the start of this
procedure). Make the following changes to the
front-panel setup:
Select:
Set:
VERTICAL M O DE
CH 2
Off
Select:
Set:
CH 1 C O U PLIN G /IN VER T
50 Q ON | OFF
OFF
Select:
Set:
CH 2 C O U PLIN G /IN VER T
50 f t ON | OFF
OFF
Select:
Set:
BANDWIDTH
20 MHz
On
Select:
Set:
TRIGGER M O DE
AUTO
On
b.
Connect the Calibration Generator’s STD A M PLITUDE
output to the CH 1 OR X input connector via a 50 f t
Coaxial Cable. Do not use a Termination.
c.
C H E C K -C H 1 and C H 2 VOLTS/DIV and TRIGG ER
LEVEL readout accuracies as follows:
1.
Set VOLTS/DIV control to the first position listed in
Table 4-2.
2.
Set the Calibration Generator STD AMPLITUDE
output level to the corresponding Standard Ampli
tude Out level in Table 4-2. Use the TRIGGER
LEVEL control as necessary to obtain a stable
display.
NOTE
To properly verify TRIGGER LEVEL readout
accuracy, the Calibration Generator’s output
must have rising and falling transition times
(10% to 90%) > 20 ns. No overshoot should
appear on the waveform.
3.
Verify that the Calibration Generator output meets
the requirements noted above.
4.
Use the VERTICAL POSITION control to set the
bottom of the signal 3 divisions below grati
cule center.
5.
Select CURSOR FU N CTIO N and set VOLTS on.
6.
Using the CURSOR/DELAY control, align the
selected cursor (segmented) with the bottom of the
displayed waveform.
7.
Push the CURSOR SELECT button to select the
other cursor (it will change from solid to seg
mented).
8.
Use the CURSOR/DELAY control to align this
cursor to the top of the waveform. Take care to use
the same reference points (top edge, bottom edge,
or center) of the waveform and cursor as in subpart
6
.
NOTE
For VOLTS/DIV Control Settings of 2 mV,
5
mV,
and 10 mV, select TRIGGER CPLG and set
NOISE REJ on. In addition, connect the Calibra
tion Generator STD AMPLITUDE output to the
C H I OR X Input connector via a 5 0 0 cable and
a 10X attenuator for the settings listed above.
For all other settings, set NOISE REJ off and
remove the 10X attenuator.
9.
C H E C K —That the voltage reading displayed by
the cursor readout is within the limits given in Table
4 -2 under the CURSOR VOLTS Readout Accura-
cy-NORMAL M O DE column.
10. Select STORAGE ACQ UIRE and set ENVE
LOPE on.
11. Using the CURSOR/DELAY control, readjust the
cursors as necessary to align them to the top or
bottom (discount noise) of the waveform. Press
CURSO R SELECT as needed to toggle between
the two cursors.
12. C H E C K —That the voltage reading displayed is
within the limits given in Table 4-2 under the
CURSO R VOLTS Readout Accuracy-ENVELOPE
M O DE column.
13. Set the ACQUIRE menu back to NORMAL on.
14. Set the TRIGGER LEVEL control at the most
positive voltage that produces a barely triggered,
jittering display for the positive ( + ) setting for the
slope switch.
15. C H E C K -T h e A Trigger Level readings (up
per-right corner of display) are within the limits
listed in the ( + ) Peak column under Limits-DC
Coupling in Table 4-2.
16. Set the TRIGGER LEVEL control at the most
negative voltage that produces a barely triggered,
jittering display for negative (-) setting for the
slope switch.
17. C H E C K -T h e A Trigger Level readings are within
the limits listed In the (-) Peak column under
Limits-DC Coupling in Table 4-2.
4-8
Summary of Contents for 2440
Page 4: ......
Page 12: ......
Page 38: ......
Page 91: ...Theory of Operation 2440 Service 3 49 Figure 3 5 Simplified CCD architecture ...
Page 120: ...Theory of Operation 2440 Service Figure 3 10 DC Restorer 3 78 ...
Page 130: ...Theory of Operation 2440 Service 3 88 ...
Page 136: ...Theory of Operation 2440 Service Figure 3 15 PWM Regulator and Inverter 3 94 ...
Page 138: ...Theory of Operation 2440 Service Figure 3 16 PWM switching waveforms 3 96 ...
Page 208: ......
Page 322: ......
Page 419: ......
Page 423: ...2440 Service Figure 9 4b 2440 Block diagram part 2 6330 27 BLOCK DIAGRAM PART 2 ...
Page 427: ......
Page 428: ...2440 Service WAVEFORMS FOR DIAGRAM 1 6 2 8 5 3 2 ...
Page 429: ......
Page 432: ...2440 Service WAVEFORMS FOR DIAGRAM 2 BUS ISOLATED 6 6 0 3 4 9 ...
Page 433: ...WAVEFORMS FOR DIAGRAM 2 ...
Page 439: ......
Page 445: ......
Page 450: ...2440 Service WAVEFORMS FOR DIAGRAM 8 6603 27 ...
Page 455: ...W A V EFO R M S FOR D IAG RAM 11 WAVEFORMS FOR DIAGRAM 11 6603 29 ...
Page 458: ...WAVEFORMS FOR DIAGRAM 12 ...
Page 463: ...WAVEFORMS FOR DIAGRAM 14 ...
Page 471: ... C N i u i t e x r 4 j u J l i 1 i 6 28 5 44 WAVEFORMS FOR DIAGRAM 18 ...
Page 476: ...WAVEFORMS FOR DIAGRAM 20 ...
Page 490: ...YES ...
Page 492: ......
Page 494: ......
Page 499: ...YES ...
Page 501: ......
Page 502: ...2440 Service FIG 1 C A B IN E T ...
Page 503: ......
Page 510: ...2440 Service SISSVHO Z Old ...
Page 511: ......
Page 512: ...A12 2440 Service F IG 3 C IR C U IT BOARDS ...
Page 513: ......
Page 517: ...10 16 R E V J U L 1993 Replaceable Mechanical Parts ...
Page 518: ...2440 Service ...
Page 519: ...FIG 4 L V H V PWR SUPPLY ...
Page 520: ...FIG 5 ACCESSORIES 2440 Service ...
Page 521: ......
Page 523: ......
Page 529: ......
Page 530: ......
Page 531: ......