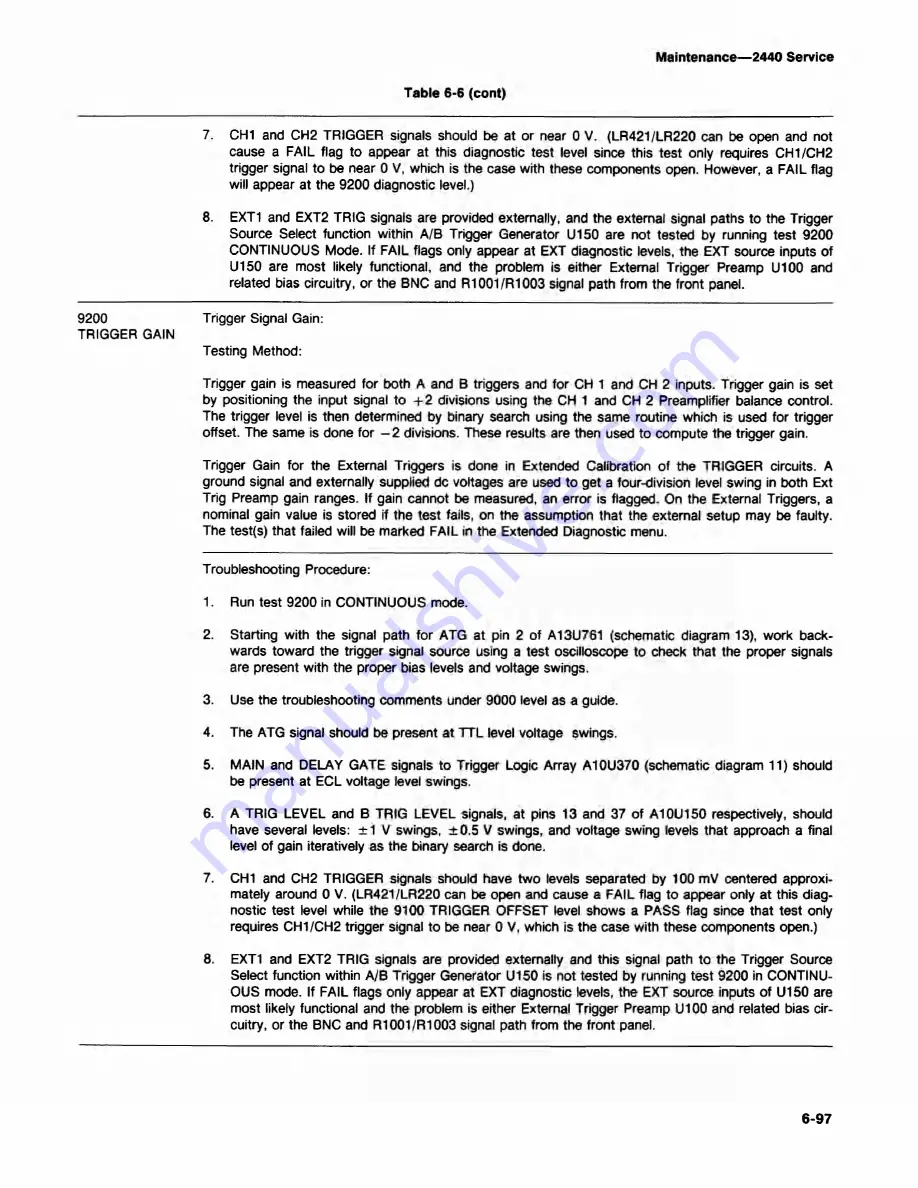
Table 6-6 (cont)
Maintenance— 2440 Service
7.
C H I and CH2 TRIGGER signals should be at or near 0 V. (LR421/LR220 can be open and not
cause a FAIL flag to appear at this diagnostic test level since this test only requires CH1/CH2
trigger signal to be near 0 V, which is the case with these components open. However, a FAIL flag
will appear at the 9200 diagnostic level.)
8.
EXT1 and EXT2 TRIG signals are provided externally, and the external signal paths to the Trigger
Source Select function within A/B Trigger Generator U150 are not tested by running test 9200
CONTINUOUS Mode. If FAIL flags only appear at EXT diagnostic levels, the EXT source inputs of
U150 are most likely functional, and the problem is either External Trigger Preamp U100 and
related bias circuitry, or the BNC and R 1001/R1003 signal path from the front panel.
9200
Trigger Signal Gain:
TRIGGER GAIN
Testing Method:
Trigger gain is measured for both A and B triggers and for CH 1 and CH 2 inputs. Trigger gain is set
by positioning the input signal to + 2 divisions using the CH 1 and CH 2 Preamplifier balance control.
The trigger level is then determined by binary search using the same routine which is used for trigger
offset. The same is done for —2 divisions. These results are then used to compute the trigger gain.
Trigger Gain for the External Triggers is done in Extended Calibration of the TRIGGER circuits. A
ground signal and externally supplied dc voltages are used to get a four-division level swing in both Ext
Trig Preamp gain ranges. If gain cannot be measured, an error is flagged. On the External Triggers, a
nominal gain value is stored if the test fails, on the assumption that the external setup may be faulty.
The test(s) that failed will be marked FAIL in the Extended Diagnostic menu.
Troubleshooting Procedure:
1.
Run test 9200 in CONTINUOUS mode.
2.
Starting with the signal path for ATG at pin 2 of A13U761 (schematic diagram 13), work back
wards toward the trigger signal source using a test oscilloscope to check that the proper signals
are present with the proper bias levels and voltage swings.
3.
Use the troubleshooting comments under 9000 level as a guide.
4.
The ATG signal should be present at TTL level voltage swings.
5.
MAIN and DELAY GATE signals to Trigger Logic Array A10U370 (schematic diagram 11) should
be present at ECL voltage level swings.
6.
A TRIG LEVEL and B TRIG LEVEL signals, at pins 13 and 37 of A10U150 respectively, should
have several levels: + 1 V swings, ± 0.5 V swings, and voltage swing levels that approach a final
level of gain iteratively as the binary search is done.
7.
C H I and CH2 TRIGGER signals should have two levels separated by 100 mV centered approxi
mately around 0 V. (LR421/LR220 can be open and cause a FAIL flag to appear only at this diag
nostic test level while the 9100 TRIGGER OFFSET level shows a PASS flag since that test only
requires CH1/CH2 trigger signal to be near 0 V, which is the case with these components open.)
8.
EXT1 and EXT2 TRIG signals are provided externally and this signal path to the Trigger Source
Select function within A/B Trigger Generator U150 is not tested by running test 9200 in CONTINU
OUS mode. If FAIL flags only appear at EXT diagnostic levels, the EXT source inputs of U150 are
most likely functional and the problem is either External Trigger Preamp U100 and related bias cir
cuitry, or the BNC and R1001/R1003 signal path from the front panel.
6-97
Summary of Contents for 2440
Page 4: ......
Page 12: ......
Page 38: ......
Page 91: ...Theory of Operation 2440 Service 3 49 Figure 3 5 Simplified CCD architecture ...
Page 120: ...Theory of Operation 2440 Service Figure 3 10 DC Restorer 3 78 ...
Page 130: ...Theory of Operation 2440 Service 3 88 ...
Page 136: ...Theory of Operation 2440 Service Figure 3 15 PWM Regulator and Inverter 3 94 ...
Page 138: ...Theory of Operation 2440 Service Figure 3 16 PWM switching waveforms 3 96 ...
Page 208: ......
Page 322: ......
Page 419: ......
Page 423: ...2440 Service Figure 9 4b 2440 Block diagram part 2 6330 27 BLOCK DIAGRAM PART 2 ...
Page 427: ......
Page 428: ...2440 Service WAVEFORMS FOR DIAGRAM 1 6 2 8 5 3 2 ...
Page 429: ......
Page 432: ...2440 Service WAVEFORMS FOR DIAGRAM 2 BUS ISOLATED 6 6 0 3 4 9 ...
Page 433: ...WAVEFORMS FOR DIAGRAM 2 ...
Page 439: ......
Page 445: ......
Page 450: ...2440 Service WAVEFORMS FOR DIAGRAM 8 6603 27 ...
Page 455: ...W A V EFO R M S FOR D IAG RAM 11 WAVEFORMS FOR DIAGRAM 11 6603 29 ...
Page 458: ...WAVEFORMS FOR DIAGRAM 12 ...
Page 463: ...WAVEFORMS FOR DIAGRAM 14 ...
Page 471: ... C N i u i t e x r 4 j u J l i 1 i 6 28 5 44 WAVEFORMS FOR DIAGRAM 18 ...
Page 476: ...WAVEFORMS FOR DIAGRAM 20 ...
Page 490: ...YES ...
Page 492: ......
Page 494: ......
Page 499: ...YES ...
Page 501: ......
Page 502: ...2440 Service FIG 1 C A B IN E T ...
Page 503: ......
Page 510: ...2440 Service SISSVHO Z Old ...
Page 511: ......
Page 512: ...A12 2440 Service F IG 3 C IR C U IT BOARDS ...
Page 513: ......
Page 517: ...10 16 R E V J U L 1993 Replaceable Mechanical Parts ...
Page 518: ...2440 Service ...
Page 519: ...FIG 4 L V H V PWR SUPPLY ...
Page 520: ...FIG 5 ACCESSORIES 2440 Service ...
Page 521: ......
Page 523: ......
Page 529: ......
Page 530: ......
Page 531: ......