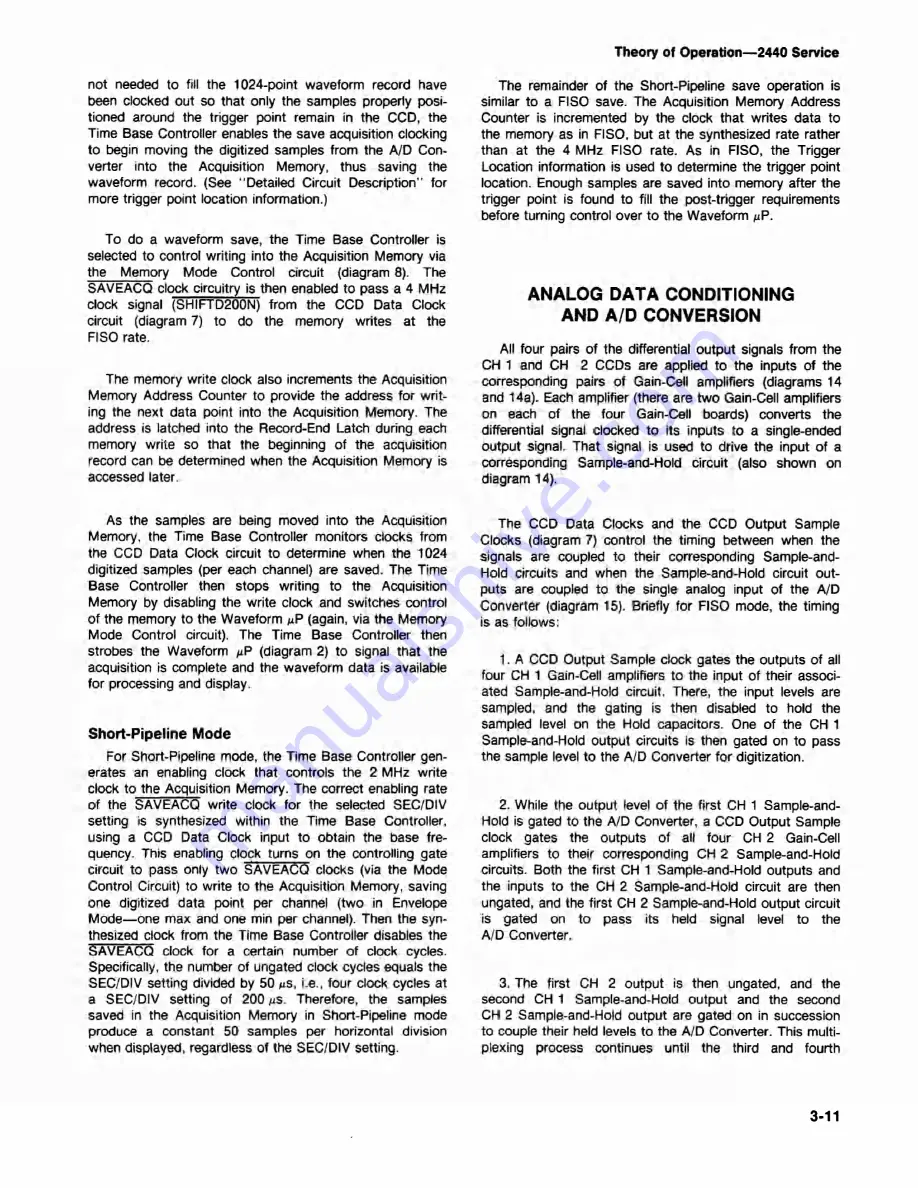
Theory of O peration— 2440 S ervice
not needed to fill the 1024-point waveform record have
been clocked out so that only the samples properly posi
tioned around the trigger point remain in the CCD, the
Time Base Controller enables the save acquisition clocking
to begin moving the digitized samples from the A/D Con
verter into the Acquisition Memory, thus saving the
waveform record. (See “ Detailed Circuit Description" for
more trigger point location information.)
To do a waveform save, the Time Base Controller is
selected to control writing into the Acquisition Memory via
the
Memory
Mode Control
circuit (diagram 8). The
SAVEACQ clock circuitry is then enabled to pass a 4 MHz
clock signal (SHIFTD200N) from the CCD Data Clock
circuit (diagram 7) to do the memory writes at the
FI SO rate.
The memory write clock also increments the Acquisition
Memory Address Counter to provide the address for writ
ing the next data point into the Acquisition Memory. The
address is latched into the Record-End Latch during each
memory write so that the beginning of the acquisition
record can be determined when the Acquisition Memory is
accessed later.
As the samples are being moved into the Acquisition
Memory, the Time Base Controller monitors clocks from
the CCD Data Clock circuit to determine when the 1024
digitized samples (per each channel) are saved. The Time
Base Controller then stops writing to the Acquisition
Memory by disabling the write clock and switches control
of the memory to the Waveform
n P
(again, via the Memory
Mode Control circuit). The Time Base Controller then
strobes the Waveform ^P (diagram 2) to signal that the
acquisition is complete and the waveform data is available
for processing and display.
S h o rt-P ip e lin e M o d e
For Short-Pipeline mode, the Time Base Controller gen
erates an enabling clock that controls the 2 MHz write
clock to the Acquisition Memory. The correct enabling rate
of the SAVEACQ write clock for the selected SEC/DIV
setting is synthesized within the Time Base Controller,
using a CCD Data Clock input to obtain the base fre
quency. This enabling clock turns on the controlling gate
circuit to pass only two SAVEACQ clocks (via the Mode
Control Circuit) to write to the Acquisition Memory, saving
one digitized data point per channel (two in Envelope
Mode— one max and one min per channel). Then the syn-
thesized clock from the Time Base Controller disables the
SAVEACQ clock for a certain number of clock cycles.
Specifically, the number of ungated clock cycles equals the
SEC/DIV setting divided by 50
fis,
i.e., four clock cycles at
a SEC/DIV setting of 200
ns.
Therefore, the samples
saved in the Acquisition Memory in Short-Pipeline mode
produce a constant 50 samples per horizontal division
when displayed, regardless of the SEC/DIV setting.
The remainder of the Short-Pipeline save operation is
similar to a FISO save. The Acquisition Memory Address
Counter is incremented by the clock that writes data to
the memory as in FISO, but at the synthesized rate rather
than at the 4 MHz FISO rate. As in FISO, the Trigger
Location information is used to determine the trigger point
location. Enough samples are saved into memory after the
trigger point is found to fill the post-trigger requirements
before turning control over to the Waveform ^P.
ANALOG DATA CONDITIONING
AND A/D CONVERSION
All four pairs of the differential output signals from the
CH 1 and CH 2 CCDs are applied to the inputs of the
corresponding pairs of Gain-Cell amplifiers (diagrams 14
and 14a). Each amplifier (there are two Gain-Cell amplifiers
on each of the four Gain-Cell boards) converts the
differential signal clocked to its inputs to a single-ended
output signal. That signal is used to drive the input of a
corresponding Sample-and-Hold circuit (also shown on
diagram 14).
The CCD Data Clocks and the CCD Output Sample
Clocks (diagram 7) control the timing between when the
signals are coupled to their corresponding Sample-and-
Hold circuits and when the Sample-and-Hold circuit out
puts are coupled to the single analog input of the A/D
Converter (diagram 15). Briefly for FISO mode, the timing
is as follows:
1.
A CCD Output Sample clock gates the outputs of all
four CH 1 Gain-Cell amplifiers to the input of their associ
ated Sample-and-Hold circuit. There, the input levels are
sampled, and the gating is then disabled to hold the
sampled level on the Hold capacitors. One of the CH 1
Sample-and-Hold output circuits is then gated on to pass
the sample level to the A/D Converter for digitization.
2.
While the output level of the first CH 1 Sample-and-
Hold is gated to the A/D Converter, a CCD Output Sample
clock gates the outputs of all four CH 2 Gain-Cell
amplifiers to their corresponding CH 2 Sample-and-Hold
circuits. Both the first CH 1 Sample-and-Hold outputs and
the inputs to the CH 2 Sample-and-Hold circuit are then
ungated, and the first CH 2 Sample-and-Hold output circuit
is gated on to pass its held signal level to the
A/D Converter.
3.
The first CH 2 output is then ungated, and the
second CH 1 Sample-and-Hold output and the second
CH 2 Sample-and-Hold output are gated on in succession
to couple their held levels to the A/D Converter. This multi
plexing process continues until the third and fourth
3-11
Summary of Contents for 2440
Page 4: ......
Page 12: ......
Page 38: ......
Page 91: ...Theory of Operation 2440 Service 3 49 Figure 3 5 Simplified CCD architecture ...
Page 120: ...Theory of Operation 2440 Service Figure 3 10 DC Restorer 3 78 ...
Page 130: ...Theory of Operation 2440 Service 3 88 ...
Page 136: ...Theory of Operation 2440 Service Figure 3 15 PWM Regulator and Inverter 3 94 ...
Page 138: ...Theory of Operation 2440 Service Figure 3 16 PWM switching waveforms 3 96 ...
Page 208: ......
Page 322: ......
Page 419: ......
Page 423: ...2440 Service Figure 9 4b 2440 Block diagram part 2 6330 27 BLOCK DIAGRAM PART 2 ...
Page 427: ......
Page 428: ...2440 Service WAVEFORMS FOR DIAGRAM 1 6 2 8 5 3 2 ...
Page 429: ......
Page 432: ...2440 Service WAVEFORMS FOR DIAGRAM 2 BUS ISOLATED 6 6 0 3 4 9 ...
Page 433: ...WAVEFORMS FOR DIAGRAM 2 ...
Page 439: ......
Page 445: ......
Page 450: ...2440 Service WAVEFORMS FOR DIAGRAM 8 6603 27 ...
Page 455: ...W A V EFO R M S FOR D IAG RAM 11 WAVEFORMS FOR DIAGRAM 11 6603 29 ...
Page 458: ...WAVEFORMS FOR DIAGRAM 12 ...
Page 463: ...WAVEFORMS FOR DIAGRAM 14 ...
Page 471: ... C N i u i t e x r 4 j u J l i 1 i 6 28 5 44 WAVEFORMS FOR DIAGRAM 18 ...
Page 476: ...WAVEFORMS FOR DIAGRAM 20 ...
Page 490: ...YES ...
Page 492: ......
Page 494: ......
Page 499: ...YES ...
Page 501: ......
Page 502: ...2440 Service FIG 1 C A B IN E T ...
Page 503: ......
Page 510: ...2440 Service SISSVHO Z Old ...
Page 511: ......
Page 512: ...A12 2440 Service F IG 3 C IR C U IT BOARDS ...
Page 513: ......
Page 517: ...10 16 R E V J U L 1993 Replaceable Mechanical Parts ...
Page 518: ...2440 Service ...
Page 519: ...FIG 4 L V H V PWR SUPPLY ...
Page 520: ...FIG 5 ACCESSORIES 2440 Service ...
Page 521: ......
Page 523: ......
Page 529: ......
Page 530: ......
Page 531: ......