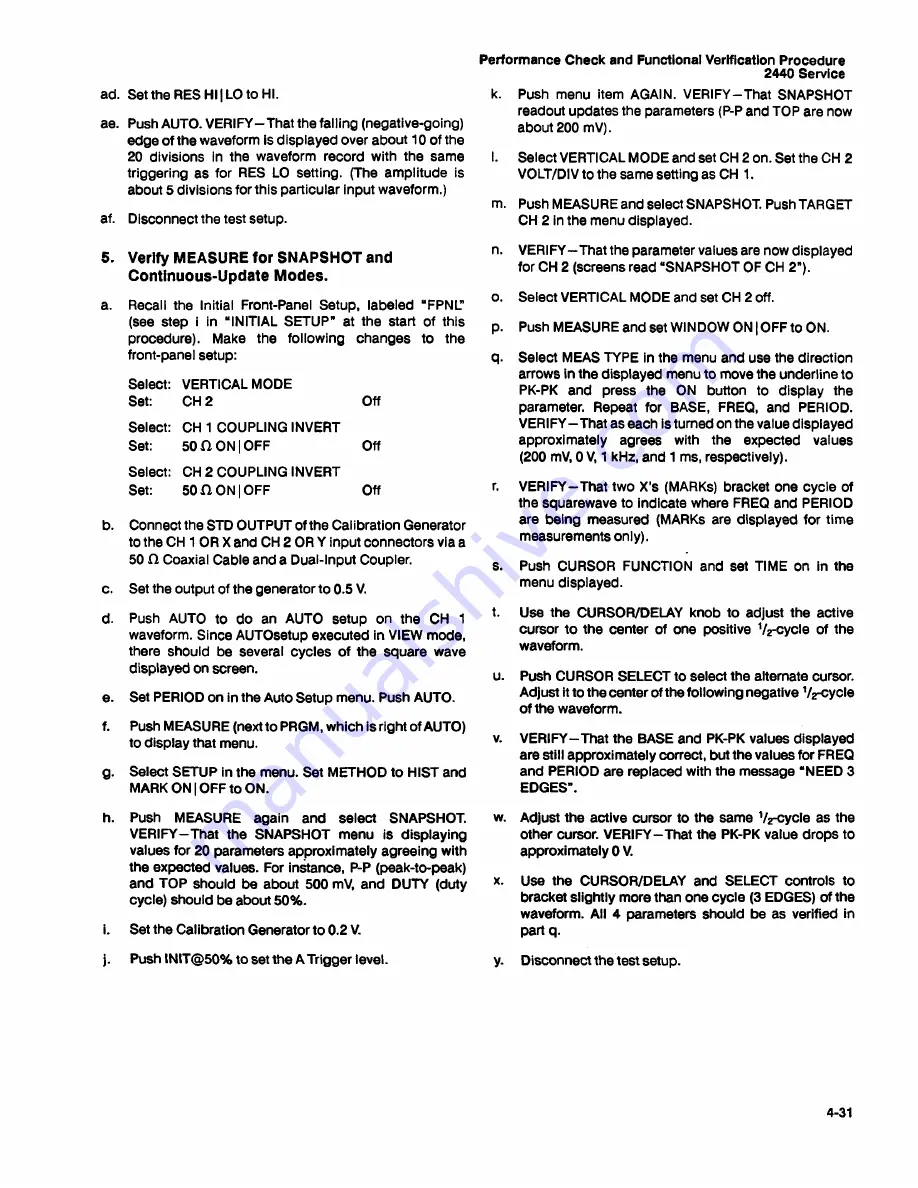
ad. Set the RES HI | LO to HI.
ae. Push AUTO. V ER IFY—That the falling (negative-going)
edge of the waveform is displayed over about 10 of the
20 divisions in the waveform record with the same
triggering as for RES LO setting. (The amplitude is
about 5 divisions for this particular input waveform.)
af. Disconnect the test setup.
5. Verify MEASURE for SNAPSHOT and
Continuous-Update Modes.
a.
Recall the Initial Front-Panel Setup, labeled “FPNL"
(see step i in “INITIAL SETUP" at the start of this
procedure). Make the following changes to the
front-panel setup:
Select:
VERTICAL M O DE
Set:
CH 2
Off
Select:
CH 1 COUPLING INVERT
Set:
50 f t ON | OFF
Off
Select:
CH 2 COUPLING INVERT
Set:
50 f t ON | OFF
Off
b.
Connect the STD OUTPU T of the Calibration Generator
to the CH 1 OR X and CH 2 OR Y input connectors via a
50 f t Coaxial Cable and a Dual-Input Coupler.
c.
Set the output of the generator to 0.5 V.
d.
Push AUTO to do an AUTO setup on the CH 1
waveform. Since AUTOsetup executed in VIEW mode,
there should be several cycles of the square wave
displayed on screen.
e.
Set PERIOD on in the Auto Setup menu. Push AUTO.
f.
Push MEASURE (next to PRGM, which is right of AUTO)
to display that menu.
g.
Select SETU P in the menu. Set M E TH O D to H IS T and
MARK ON | OFF to ON.
h.
Push MEASURE again and select SNAPSHOT.
V E R IF Y -T h a t the SN A PSH O T menu is displaying
values for 20 parameters approximately agreeing with
the expected values. For instance, P-P (peak-to-peak)
and T O P should be about 500 mV, and D UTY (duty
cycle) should be about 50 % .
i.
Set the Calibration Generator to 0.2 V.
j.
Push IN IT @ 5 0 % to set the A Trigger level.
Perform ance C heck and Functional Verification Procedure
2440 Service
k.
Push menu item AGAIN. V ER IFY—That SNAPSHOT
readout updates the parameters (P-P and TOP are now
about 200 mV).
l
.
Select VERTICAL MO DE and set CH 2 on. Set the CH 2
VOLT/DIV to the same setting as CH 1.
m. Push MEASURE and select SNAPSHOT. Push TARGET
CH 2 in the menu displayed.
n.
V ER IFY—That the parameter values are now displayed
for CH 2 (screens read “SNAPSHOT OF CH 2").
o.
Select VERTICAL M ODE and set CH 2 off.
p.
Push MEASURE and set W INDOW ON I OFF to ON.
q.
Select MEAS TYPE in the menu and use the direction
arrows in the displayed menu to move the underline to
PK-PK and press the ON button to display the
parameter. Repeat for BASE, FREQ, and PERIOD.
V E R IF Y -T h a t as each is turned on the value displayed
approximately agrees with the expected values
(200 mV, 0 V, 1 kHz, and 1 ms, respectively).
r.
V E R IF Y -T h a t two X ’s (MARKs) bracket one cycle of
the squarewave to indicate where FREQ and PERIOD
are being measured (MARKs are displayed for time
measurements only).
s.
Push CURSOR FUNCTION and set TIM E on in the
menu displayed.
t.
Use the CURSOR/DELAY knob to adjust the active
cursor to the center of one positive
72
-cycle of the
waveform.
u.
Push CURSOR SELECT to select the alternate cursor.
Adjust it to the center of the following negative 72-cycle
of the waveform.
v.
V E R IF Y —That the BASE and PK-PK values displayed
are still approximately correct, but the values for FREQ
and PERIOD are replaced with the message “NEED 3
ED G ES ’ .
w. Adjust the active cursor to the same 72-cycle as the
other cursor. V E R IF Y -T h a t the PK-PK value drops to
approximately 0 V.
x.
Use the CURSOR/DELAY and SELECT controls to
bracket slightly more than one cycle (3 EDGES) of the
waveform. All 4 parameters should be as verified in
p a rtq .
y.
Disconnect the test setup.
4-31
Summary of Contents for 2440
Page 4: ......
Page 12: ......
Page 38: ......
Page 91: ...Theory of Operation 2440 Service 3 49 Figure 3 5 Simplified CCD architecture ...
Page 120: ...Theory of Operation 2440 Service Figure 3 10 DC Restorer 3 78 ...
Page 130: ...Theory of Operation 2440 Service 3 88 ...
Page 136: ...Theory of Operation 2440 Service Figure 3 15 PWM Regulator and Inverter 3 94 ...
Page 138: ...Theory of Operation 2440 Service Figure 3 16 PWM switching waveforms 3 96 ...
Page 208: ......
Page 322: ......
Page 419: ......
Page 423: ...2440 Service Figure 9 4b 2440 Block diagram part 2 6330 27 BLOCK DIAGRAM PART 2 ...
Page 427: ......
Page 428: ...2440 Service WAVEFORMS FOR DIAGRAM 1 6 2 8 5 3 2 ...
Page 429: ......
Page 432: ...2440 Service WAVEFORMS FOR DIAGRAM 2 BUS ISOLATED 6 6 0 3 4 9 ...
Page 433: ...WAVEFORMS FOR DIAGRAM 2 ...
Page 439: ......
Page 445: ......
Page 450: ...2440 Service WAVEFORMS FOR DIAGRAM 8 6603 27 ...
Page 455: ...W A V EFO R M S FOR D IAG RAM 11 WAVEFORMS FOR DIAGRAM 11 6603 29 ...
Page 458: ...WAVEFORMS FOR DIAGRAM 12 ...
Page 463: ...WAVEFORMS FOR DIAGRAM 14 ...
Page 471: ... C N i u i t e x r 4 j u J l i 1 i 6 28 5 44 WAVEFORMS FOR DIAGRAM 18 ...
Page 476: ...WAVEFORMS FOR DIAGRAM 20 ...
Page 490: ...YES ...
Page 492: ......
Page 494: ......
Page 499: ...YES ...
Page 501: ......
Page 502: ...2440 Service FIG 1 C A B IN E T ...
Page 503: ......
Page 510: ...2440 Service SISSVHO Z Old ...
Page 511: ......
Page 512: ...A12 2440 Service F IG 3 C IR C U IT BOARDS ...
Page 513: ......
Page 517: ...10 16 R E V J U L 1993 Replaceable Mechanical Parts ...
Page 518: ...2440 Service ...
Page 519: ...FIG 4 L V H V PWR SUPPLY ...
Page 520: ...FIG 5 ACCESSORIES 2440 Service ...
Page 521: ......
Page 523: ......
Page 529: ......
Page 530: ......
Page 531: ......