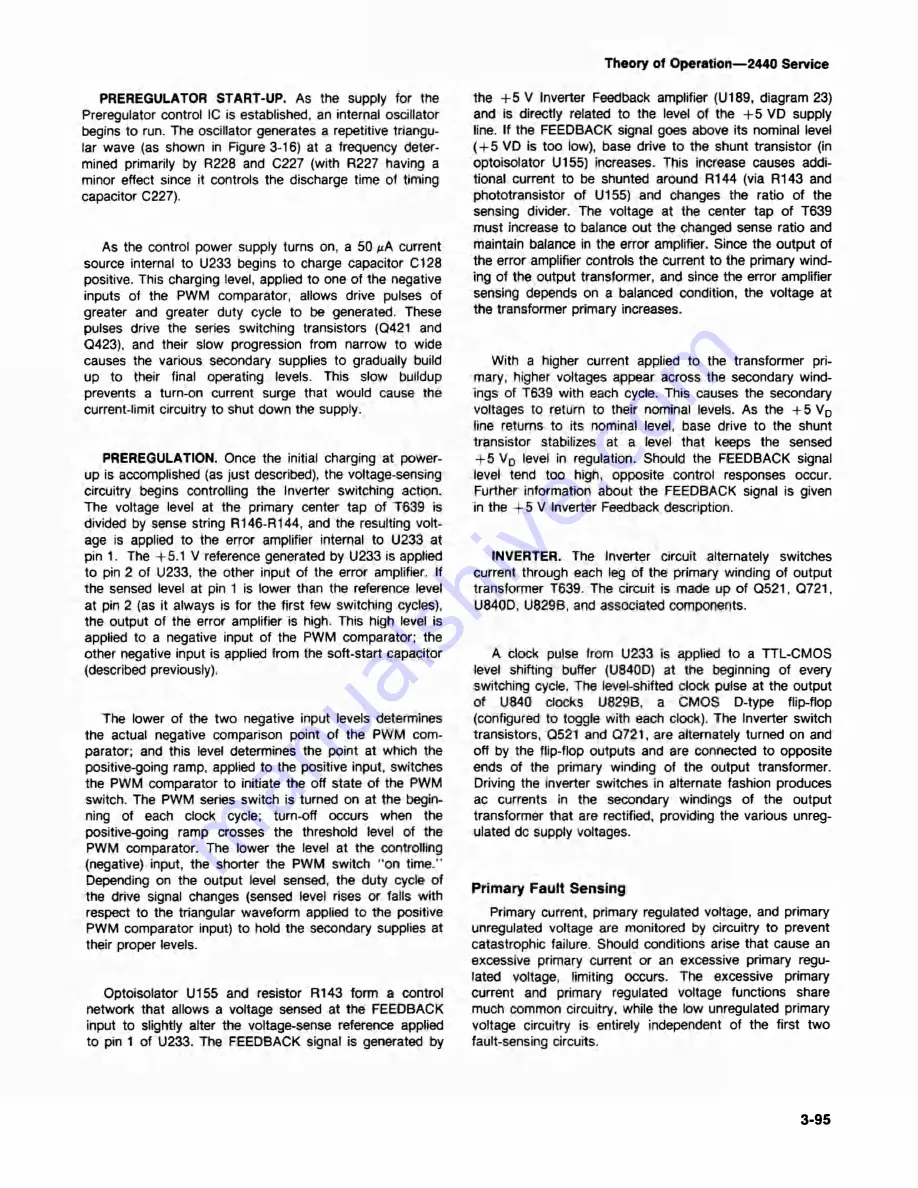
Theory of Operation— 2440 Service
PREREGULATOR START-UP. As the supply for the
Preregulator control 1C is established, an internal oscillator
begins to run. The oscillator generates a repetitive triangu
lar wave (as shown in Figure 3-16) at a frequency deter
mined primarily by R228 and C227 (with R227 having a
minor effect since it controls the discharge time of timing
capacitor C227).
As the control power supply turns on, a 50
nA
current
source internal to U233 begins to charge capacitor C l 28
positive. This charging level, applied to one of the negative
inputs of the PWM comparator, allows drive pulses of
greater and greater duty cycle to be generated. These
pulses drive the series switching transistors (Q421 and
Q423), and their slow progression from narrow to wide
causes the various secondary supplies to gradually build
up to their final operating levels. This slow buildup
prevents a turn-on current surge that would cause the
current-limit circuitry to shut down the supply.
PREREGULATION. Once the initial charging at power-
up is accomplished (as just described), the voltage-sensing
circuitry begins controlling the Inverter switching action.
The voltage level at the primary center tap of T639 is
divided by sense string R146-R144, and the resulting volt
age is applied to the error amplifier internal to U233 at
pin 1. The + 5 .1 V reference generated by U233 is applied
to pin 2 of U233, the other input of the error amplifier. If
the sensed level at pin 1 is lower than the reference level
at pin 2 (as it always is for the first few switching cycles),
the output of the error amplifier is high. This high level is
applied to a negative input of the PWM comparator; the
other negative input is applied from the soft-start capacitor
(described previously).
The lower of the two negative input levels determines
the actual negative comparison point of the PWM com
parator; and this level determines the point at which the
positive-going ramp, applied to the positive input, switches
the PWM comparator to initiate the off state of the PWM
switch. The PWM series switch is turned on at the begin
ning of each clock cycle; turn-off occurs when the
positive-going ramp crosses the threshold level of the
PWM comparator. The lower the level at the controlling
(negative) input, the shorter the PWM switch “on time.”
Depending on the output level sensed, the duty cycle of
the drive signal changes (sensed level rises or falls with
respect to the triangular waveform applied to the positive
PWM comparator input) to hold the secondary supplies at
their proper levels.
Optoisolator U155 and resistor R143 form a control
network that allows a voltage sensed at the FEEDBACK
input to slightly alter the voltage-sense reference applied
to pin 1 of U233. The FEEDBACK signal is generated by
the + 5 V Inverter Feedback amplifier (U189, diagram 23)
and is directly related to the level of the + 5 VD supply
line. If the FEEDBACK signal goes above its nominal level
( + 5 VD is too low), base drive to the shunt transistor (in
optoisolator U155) increases. This increase causes addi
tional current to be shunted around R144 (via R143 and
phototransistor of U155) and changes the ratio of the
sensing divider. The voltage at the center tap of T639
must increase to balance out the changed sense ratio and
maintain balance in the error amplifier. Since the output of
the error amplifier controls the current to the primary wind
ing of the output transformer, and since the error amplifier
sensing depends on a balanced condition, the voltage at
the transformer primary increases.
With a higher current applied to the transformer pri
mary, higher voltages appear across the secondary wind
ings of T639 with each cycle. This causes the secondary
voltages to return to their nominal levels. As the + 5 V D
line returns to its nominal level, base drive to the shunt
transistor stabilizes at a level that keeps the sensed
+ 5 V D level in regulation. Should the FEEDBACK signal
level tend too high, opposite control responses occur.
Further information about the FEEDBACK signal is given
in the + 5 V Inverter Feedback description.
INVERTER. The Inverter circuit alternately switches
current through each leg of the primary winding of output
transformer T639. The circuit is made up of Q521, Q721,
U840D, U829B, and associated components.
A clock pulse from U233 is applied to a TTL-CMO S
level shifting buffer (U840D) at the beginning of every
switching cycle. The level-shifted clock pulse at the output
of
U840
clocks
U829B,
a
CM OS
D-type flip-flop
(configured to toggle with each clock). The Inverter switch
transistors, Q521 and Q 721, are alternately turned on and
off by the flip-flop outputs and are connected to opposite
ends of the primary winding of the output transformer.
Driving the inverter switches in alternate fashion produces
ac currents in the secondary windings of the output
transformer that are rectified, providing the various unreg
ulated dc supply voltages.
Prim ary Fault Sensing
Primary current, primary regulated voltage, and primary
unregulated voltage are monitored by circuitry to prevent
catastrophic failure. Should conditions arise that cause an
excessive primary current or an excessive primary regu
lated voltage, limiting occurs. The excessive primary
current and primary regulated voltage functions share
much common circuitry, while the low unregulated primary
voltage circuitry is entirely independent of the first two
fault-sensing circuits.
3 -9 5
Summary of Contents for 2440
Page 4: ......
Page 12: ......
Page 38: ......
Page 91: ...Theory of Operation 2440 Service 3 49 Figure 3 5 Simplified CCD architecture ...
Page 120: ...Theory of Operation 2440 Service Figure 3 10 DC Restorer 3 78 ...
Page 130: ...Theory of Operation 2440 Service 3 88 ...
Page 136: ...Theory of Operation 2440 Service Figure 3 15 PWM Regulator and Inverter 3 94 ...
Page 138: ...Theory of Operation 2440 Service Figure 3 16 PWM switching waveforms 3 96 ...
Page 208: ......
Page 322: ......
Page 419: ......
Page 423: ...2440 Service Figure 9 4b 2440 Block diagram part 2 6330 27 BLOCK DIAGRAM PART 2 ...
Page 427: ......
Page 428: ...2440 Service WAVEFORMS FOR DIAGRAM 1 6 2 8 5 3 2 ...
Page 429: ......
Page 432: ...2440 Service WAVEFORMS FOR DIAGRAM 2 BUS ISOLATED 6 6 0 3 4 9 ...
Page 433: ...WAVEFORMS FOR DIAGRAM 2 ...
Page 439: ......
Page 445: ......
Page 450: ...2440 Service WAVEFORMS FOR DIAGRAM 8 6603 27 ...
Page 455: ...W A V EFO R M S FOR D IAG RAM 11 WAVEFORMS FOR DIAGRAM 11 6603 29 ...
Page 458: ...WAVEFORMS FOR DIAGRAM 12 ...
Page 463: ...WAVEFORMS FOR DIAGRAM 14 ...
Page 471: ... C N i u i t e x r 4 j u J l i 1 i 6 28 5 44 WAVEFORMS FOR DIAGRAM 18 ...
Page 476: ...WAVEFORMS FOR DIAGRAM 20 ...
Page 490: ...YES ...
Page 492: ......
Page 494: ......
Page 499: ...YES ...
Page 501: ......
Page 502: ...2440 Service FIG 1 C A B IN E T ...
Page 503: ......
Page 510: ...2440 Service SISSVHO Z Old ...
Page 511: ......
Page 512: ...A12 2440 Service F IG 3 C IR C U IT BOARDS ...
Page 513: ......
Page 517: ...10 16 R E V J U L 1993 Replaceable Mechanical Parts ...
Page 518: ...2440 Service ...
Page 519: ...FIG 4 L V H V PWR SUPPLY ...
Page 520: ...FIG 5 ACCESSORIES 2440 Service ...
Page 521: ......
Page 523: ......
Page 529: ......
Page 530: ......
Page 531: ......