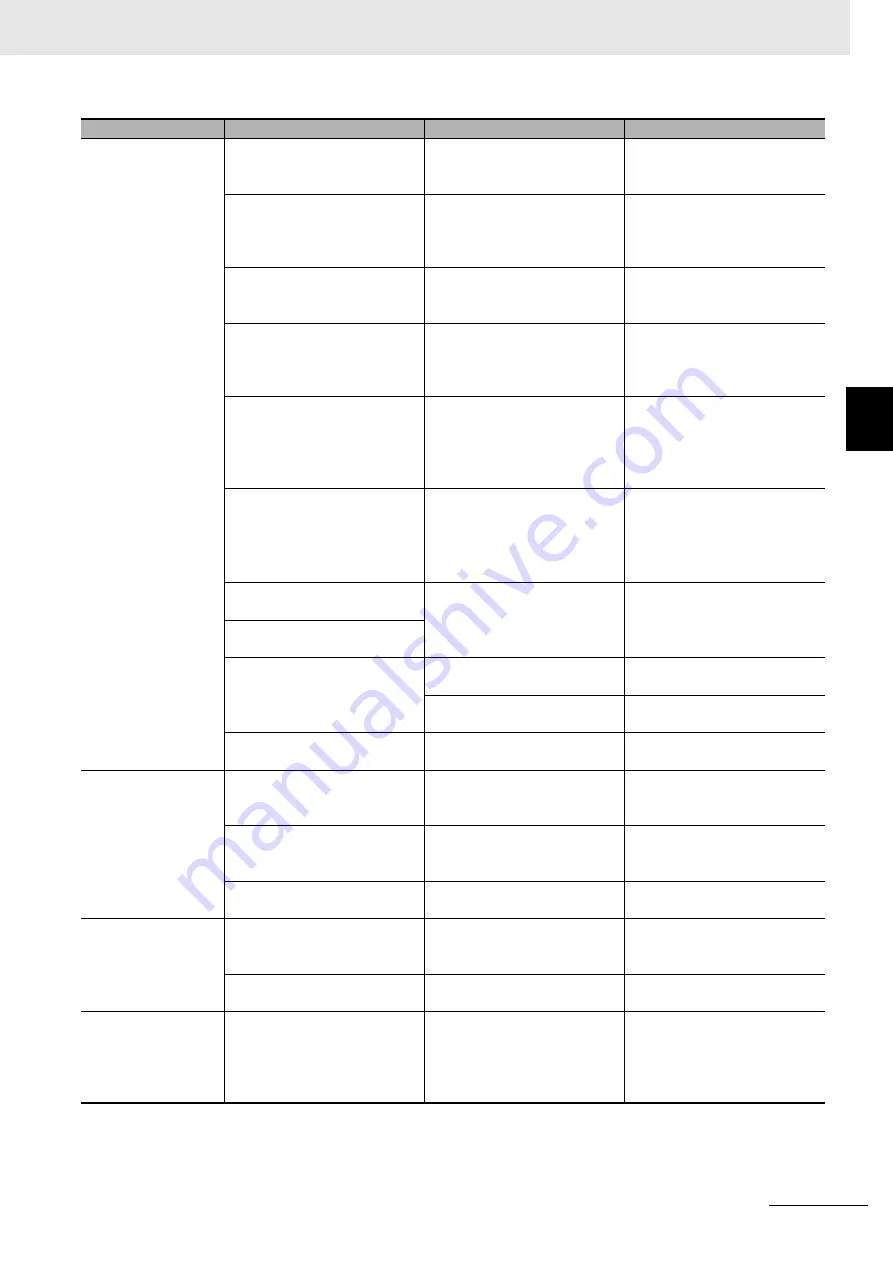
12 - 43
12 Troubleshooting
AC Servomotors/Servo Drives 1S-series with Built-in EtherCAT® Communications User’s Manual (I586)
12-
5 T
rou
blesh
oo
ting
12
12-
5-3
T
roubleshooting Using th
e Ope
ration State
The Servo locks but
the Servomotor does
not rotate.
The host controller does not
give a command.
For a position command, check
to see if the speed and position
are set to
0
.
Enter position and speed data.
Start the Servomotor.
The Servo Drive received a
command but it is not
accepted.
Check to see if the Servo Drive
retains the object value for two
communications cycles or more
in Profile position mode (pp).
Set the Servo Drive so that it
retains the object value for two
communications cycles or
more.
It is hard to determine if the
Servomotor is rotating.
Check to see if the velocity
command given by the host
controller is too small.
Check the velocity command
from the host controller.
The holding brake is operating. Check the Brake Interlock Out-
put (BKIR) signal and the +24
VDC power supply.
Check to see if the holding
brake on a Servomotor with
brake is released when the
Servo is locked.
The torque limits set in the
Positive torque limit value
(60E0 hex) and the
Negative
torque limit value
(60E1 hex)
are too small.
Check to see if the torque limits
in objects 60E0 hex and 60E1
hex are set to a value close to
0
.
Set the maximum torque that
you use for each of these
objects.
Positive Drive Prohibition Input
(POT) or Negative Drive Prohi-
bition Input (NOT) is OFF.
Check the ON/OFF state of the
POT and NOT signals from the
Sysmac Studio.
• Turn ON the POT and NOT
signals.
• Disable them in the settings
when the POT and NOT sig-
nals are not used.
The motor power cable is wired
incorrectly.
Check the wiring.
Wire correctly.
The encoder cable is wired
incorrectly.
Power is not supplied.
Check the power supply and
the 7-segment display.
Turn ON the power.
Check the voltage between the
power terminals.
Wire the power-ON circuit cor-
rectly.
The Servo Drive is broken
down.
---
Replace the Servo Drive.
The Servomotor oper-
ates momentarily, but
then it does not oper-
ate after that.
The position commands given
are too little.
Check the position data and the
electronic gear ratio at the host
controller.
Set the correct data.
The motor power cable is wired
incorrectly.
Check the wiring of the motor
power cable’s phases U, V, and
W.
Wire correctly.
The encoder cable is wired
incorrectly.
Check the encoder cable’s wir-
ing.
Wire correctly.
The Servomotor
rotates without a com-
mand.
There are inputs of small val-
ues in velocity control mode.
Check if there is an input in
velocity control mode.
Set the velocity command to
0
.
Alternatively, change the mode
to position control mode.
The motor power cable is wired
incorrectly.
Check the wiring.
Wire correctly.
When the runaway
detection function is
enabled, the
Servomotor rotates
without a command.
The Servomotor power cable is
wired incorrectly, and condi-
tions under which the runaway
detection function cannot work
are satisfied.
Check the wiring.
Wire correctly.
Symptom
Probable cause
Check items
Measures
Summary of Contents for R88D-1SN ECT Series
Page 973: ......