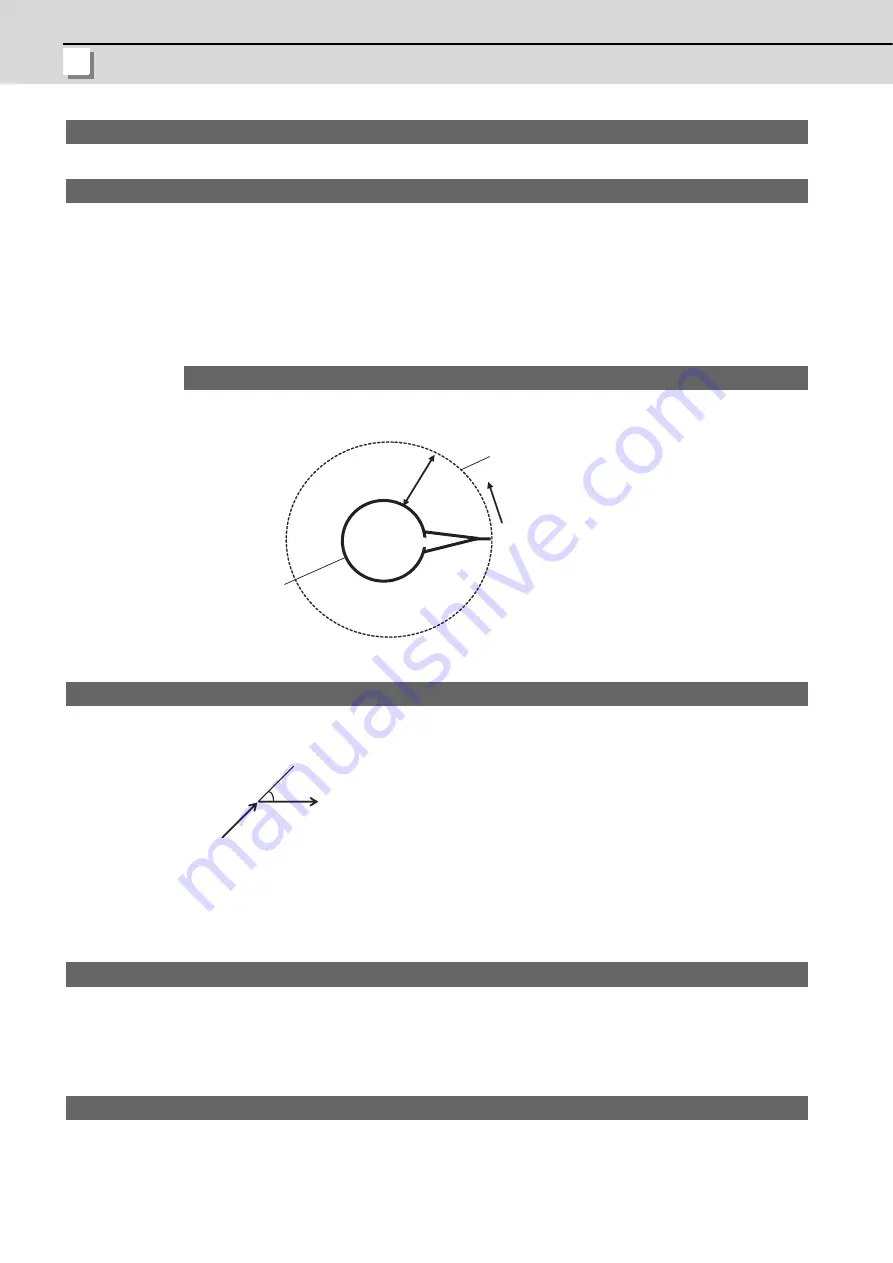
Appendix 1 Explanation of Parameters
MITSUBISHI CNC
172
【
#8018
】
G84/G74 n (for M system only)
Not used. Set to "0".
【
#8019
】
R COMP
Set a compensation coefficient for reducing a control error in the reduction of a corner roundness
and arc radius.
Indicates a maximum control error (mm) in parentheses.
The larger the set value is, the smaller the theoretical error will be. However, since the speed at the
corner goes down, the cycle time will be extended.
Coefficient = 100 - set value
(Note) This function will be enabled when "#8021 COMP_CHANGE" is set to "0".
---Setting range---
0 to 99 (%)
Theoretical radius decrease error amount
Displays the theoretical radius decrease error amount,
Δ
R(mm), from the automatic calculation by
NC.
Theoretical radius decrease amount in arc
【
#8020
】
DCC. angle
Set the minimum value of an angle (external angle) that should be assumed to be a corner.
When an inter-block angle (external angle) in high-accuracy mode is larger than the set value, it will
be determined as a corner and the speed will go down to sharpen the edge.
(Note) If "0" is set, it will be handled as "5" degrees.
The standard setting value is "0".
---Setting range---
0 to 30 (°)
0: 5 degree (Equals to setting "5")
【
#8041
】
C-rot.R
Set the length from the center of the normal line control axis to the tool tip. This is used to calculate
the turning speed at the block joint.
This is enabled during the normal line control type II.
---Setting range---
0.000 to 99999.999 (mm)
【
#8042
】
C-ins.R
Set the radius of the arc to be automatically inserted into the corner during normal line control.
This is enabled during the normal line control type I.
---Setting range---
0.000 to 99999.999 (mm)
+
Ǎ
R
F
Command path
Path after
servo control
ǰ
If the set value is smaller than
ǰ
,
the speed goes down to optimize
the corner.
Summary of Contents for C70
Page 1: ......
Page 3: ......
Page 9: ......
Page 11: ......
Page 13: ......
Page 18: ...1 1 Outline ...
Page 21: ...1 Outline MITSUBISHI CNC 4 ...
Page 22: ...5 2 GOT Initial Setup ...
Page 73: ...2 GOT Initial Setup MITSUBISHI CNC 56 ...
Page 74: ...57 3 PLC CPU Initial Setup ...
Page 91: ...3 PLC CPU Initial Setup MITSUBISHI CNC 74 ...
Page 92: ...75 4 CNC CPU Initial Setup ...
Page 105: ...4 CNC CPU Initial Setup MITSUBISHI CNC 88 ...
Page 106: ...89 5 Connecting and Setting up Multiple CNC CPU Modules ...
Page 115: ...5 Connecting and Setting up Multiple CNC CPU Modules MITSUBISHI CNC 98 ...
Page 116: ...99 6 Setting Machine Parameters ...
Page 130: ...113 7 Setting the Position Detection System ...
Page 153: ...7 Setting the Position Detection System MITSUBISHI CNC 136 ...
Page 154: ...137 8 Deceleration Check ...
Page 159: ...8 Deceleration Check MITSUBISHI CNC 142 ...
Page 160: ...143 9 Setting the Tool Entry Prohibited Range ...
Page 169: ...9 Setting the Tool Entry Prohibited Range MITSUBISHI CNC 152 ...
Page 170: ...153 10 Data Backup and Restoration ...
Page 184: ...167 Appendix 1 Explanation of Parameters ...
Page 435: ...Appendix 1 Explanation of Parameters MITSUBISHI CNC 418 ...
Page 436: ...419 Appendix 2 Explanation of Alarms ...
Page 608: ...591 Appendix 3 Display on 7 segment LED ...
Page 624: ......
Page 628: ......