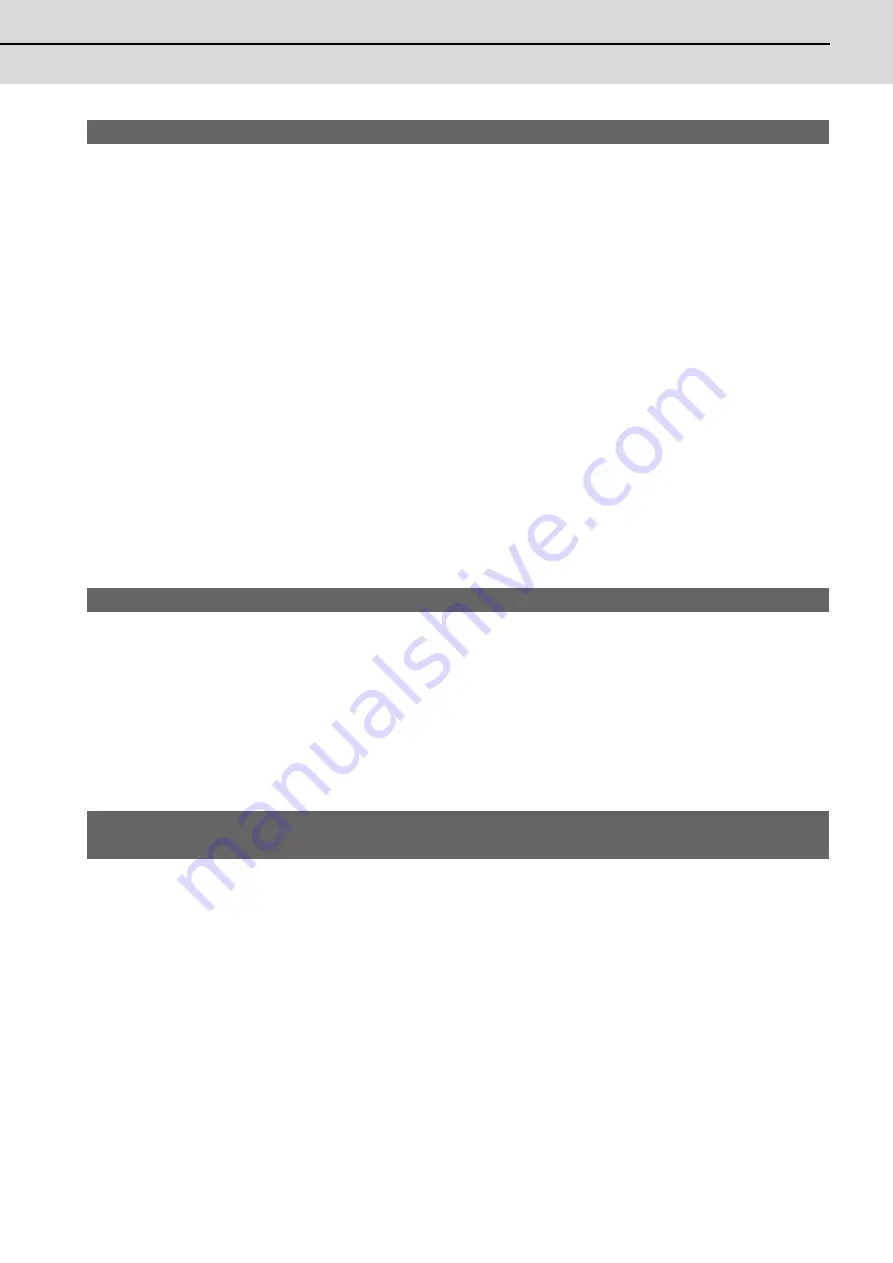
C70 Setup Manual
Appendix 1.9 DeviceNet Parameters
363
【
#29076(PR)
】
Slave Function Comm.Status PLC side Device Slave function communication
status
Set the device to store the following data:
Slave function I/O communication status is stored.
00(HEX): OFFLINE; being initialized; bus-off; network power OFF
40(HEX): STOP; I/O communication being stopped
80(HEX): READY; waiting to establish the connection from the master node
C0(HEX): OPERATE; I/O communication in progress
The communication status above varies according to the auto communication start setting (address:
0631H):
- When "0: Not automatically start" is set:
Turning the power ON automatically changes the status from OFFLINE (00(HEX)) to STOP
(40(HEX)).
Turning ON the I/O communication request (Y11) changes the state to OPERATE (C0(HEX)).
However, the status is READY (80(HEX)) until the I/O communication request is received from the
master node.
- When "1: Automatically start" is set:
Turning the power ON automatically changes the status from OFFLINE (00(HEX)) to OPERATE
(C0(HEX)). However, the status is STOP (40(HEX)) until the I/O communication request is
received from the master node.
If a reset message is received from the network, the status automatically returns to OFFLINE
(00(HEX)) and makes transitions from OFFLINE (00(HEX)) to OPERATE (C0(HEX)).
---Setting range---
Within the number of device points set in the PC parameter's device setting.
【
#29077(PR)
】
Slave Function Error Inform. PLC side Device Slave function error information
Set a device to store the following data:
<Higher byte>
The communication error code occurred in the slave function is stored.
<Lower byte>
The node No. (MAC ID) of the node where the error occurred is stored.
FE(HEX), FF(HEX) (254, 255): Local node (QJ71DN91)
00 to 3F(HEX) (0 to 63): Node No. (MAC ID) of the node where the error occurred.
---Setting range---
Within the number of device points set in the PC parameter's device setting.
【
#29078(PR)
】
Master Func. IO Addr. Area Module side Transfer Cont.
Master function I/O address area read word count
Set a read word count of the data which stores the head address and the size (in word form) of the
master function receive and transmit data used by each slave node.
The standard setting is "252".
---Setting range---
1 to 252
Summary of Contents for C70
Page 1: ......
Page 3: ......
Page 9: ......
Page 11: ......
Page 13: ......
Page 18: ...1 1 Outline ...
Page 21: ...1 Outline MITSUBISHI CNC 4 ...
Page 22: ...5 2 GOT Initial Setup ...
Page 73: ...2 GOT Initial Setup MITSUBISHI CNC 56 ...
Page 74: ...57 3 PLC CPU Initial Setup ...
Page 91: ...3 PLC CPU Initial Setup MITSUBISHI CNC 74 ...
Page 92: ...75 4 CNC CPU Initial Setup ...
Page 105: ...4 CNC CPU Initial Setup MITSUBISHI CNC 88 ...
Page 106: ...89 5 Connecting and Setting up Multiple CNC CPU Modules ...
Page 115: ...5 Connecting and Setting up Multiple CNC CPU Modules MITSUBISHI CNC 98 ...
Page 116: ...99 6 Setting Machine Parameters ...
Page 130: ...113 7 Setting the Position Detection System ...
Page 153: ...7 Setting the Position Detection System MITSUBISHI CNC 136 ...
Page 154: ...137 8 Deceleration Check ...
Page 159: ...8 Deceleration Check MITSUBISHI CNC 142 ...
Page 160: ...143 9 Setting the Tool Entry Prohibited Range ...
Page 169: ...9 Setting the Tool Entry Prohibited Range MITSUBISHI CNC 152 ...
Page 170: ...153 10 Data Backup and Restoration ...
Page 184: ...167 Appendix 1 Explanation of Parameters ...
Page 435: ...Appendix 1 Explanation of Parameters MITSUBISHI CNC 418 ...
Page 436: ...419 Appendix 2 Explanation of Alarms ...
Page 608: ...591 Appendix 3 Display on 7 segment LED ...
Page 624: ......
Page 628: ......