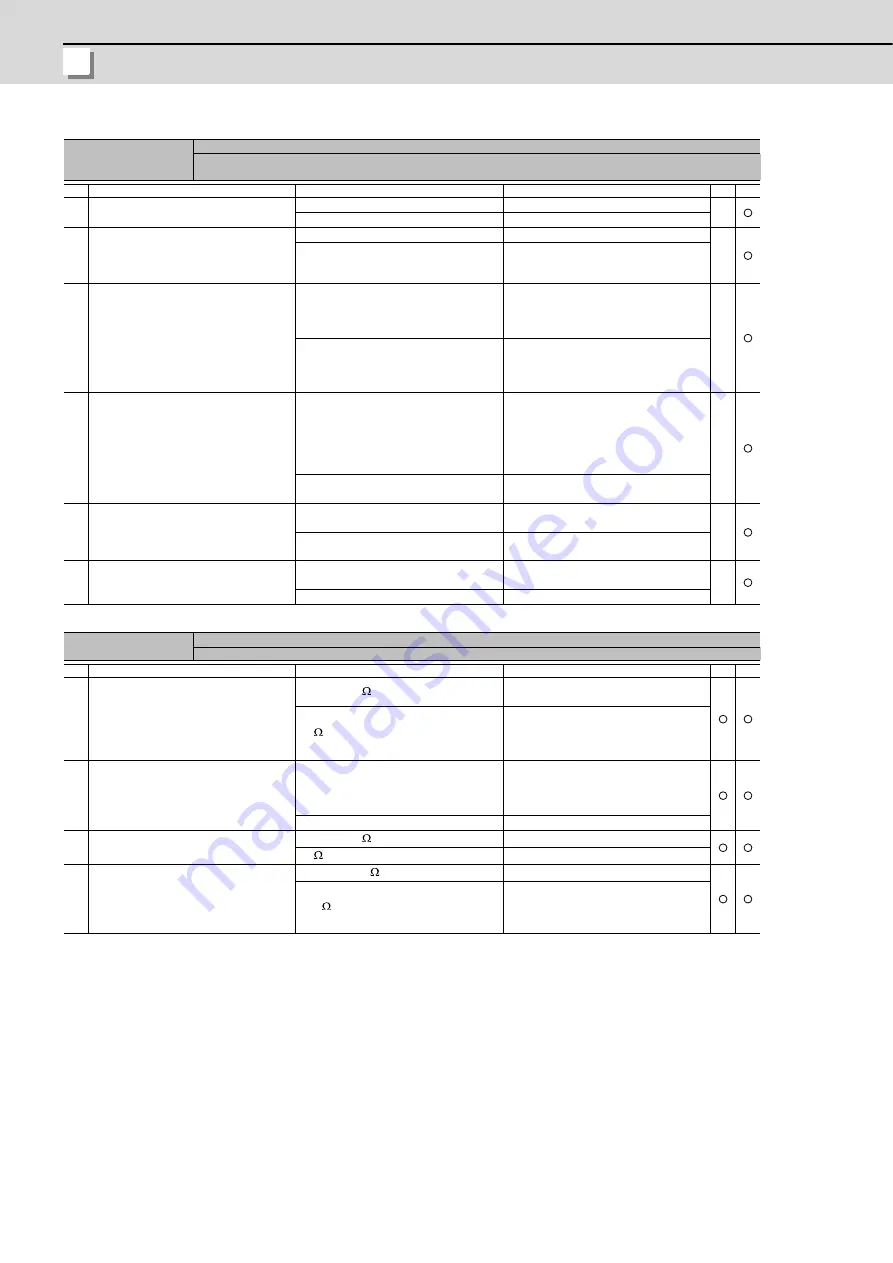
Appendix 2 Explanation of Alarms
MITSUBISHI CNC
562
Alarm No.
23
Excessive speed error
A difference between the speed command and speed feedback was continuously exceeding 50 r/min for longer than the
setting time.
Investigation details
Investigation results
Remedies
SV
SP
1
Check the U, V and W wiring connected to
the spindle drive unit.
The wires are not correctly connected.
Correctly connect.
The wires are correctly connected.
Check the investigation item No. 2.
2
Check the spindle parameter SP020,
SP026, SP027, from SP057 to SP064 and
spindle specification parameters from
slimit1 to slimit4 setting value.
The correct values are not set.
Correctly set.
The correct values are set.
Check the investigation item No. 3.
3
Measure the acceleration/ deceleration time
from 0 to the point where the spindle speed
reaches its maximum.
If the alarm occurs when forward run is
changed to reverse run, measure the
acceleration/ deceleration time from the
forward to reverse. Also measure it from the
reverse to forward.
12sec or more.
(SP117 setting value or more.)
Increase the spindle acceleration/
deceleration time constant setting
value(sp_t1 to sp_t4).
Reduce the load inertia.
Less than 12sec.
Check the investigation item No. 4.
4
Check the load amount when the alarm
occurred during cutting.
The speed deterioration due to load amount
has exceeded the tolerable range which is
determined by the parameter SP096.
-If SP096 is set to 0, it is regarded as 85%.
Thus a speed of 85% of the machining
speed or faster will be the tolerable speed.
Reduce the cutting load to mitigate the
speed deterioration.
Replace the tool.
The load amount is within the SP096 setting
value.
Check the investigation item No. 5.
5
Check the fluctuation of the input voltage
into the power supply unit with a tester.
Voltage drop during acceleration is 200V or
less
Review the power supply capacity.
Voltage drop during acceleration is 200V or
more
Check the investigation item No.6.
6
Check the capacity of the drive unit.
The capacity does not satisfy the motor
output.
Change the capacity to the selected one.
The capacity satisfies the motor output.
Replace the unit.
Alarm No.
24
Grounding
The motor power cable is in contact with FG (Frame Ground).
Investigation details
Investigation results
Remedies
SV
SP
1
Measure the insulation across the power
cables (U,V,W) for connected motors and
the ground. (Carry out a megger test.)
(Note)
When the insulation is measured,
disconnect wires from the drive unit.
Less than 1M
.
The motor or power cable may be ground
faulted.
1M
or more.
Check the investigation item No. 2.
2
Has oil come in contact with the motor or
power cable?
Oil has come in contact.
Take measures so that oil does not come in
contact. Check the motor's cannon
connector and the inside of the terminal box,
and clean as necessary.
Oil has not come in contact.
Check the investigation item No. 3.
3
Measure the insulation again.
Less than 1M
.
Replace the motor or cable.
1M
or more.
Check the investigation item No. 4.
4
Measure the resistance across the U, V, W
phase terminals of the servo/spindle drive
unit and the ground with a tester.
(Note) Do not measure the insulation as the
unit is damaged.
Less than 100k
.
Replace the drive unit.
100k
or more.
Replace the power supply unit.
Summary of Contents for C70
Page 1: ......
Page 3: ......
Page 9: ......
Page 11: ......
Page 13: ......
Page 18: ...1 1 Outline ...
Page 21: ...1 Outline MITSUBISHI CNC 4 ...
Page 22: ...5 2 GOT Initial Setup ...
Page 73: ...2 GOT Initial Setup MITSUBISHI CNC 56 ...
Page 74: ...57 3 PLC CPU Initial Setup ...
Page 91: ...3 PLC CPU Initial Setup MITSUBISHI CNC 74 ...
Page 92: ...75 4 CNC CPU Initial Setup ...
Page 105: ...4 CNC CPU Initial Setup MITSUBISHI CNC 88 ...
Page 106: ...89 5 Connecting and Setting up Multiple CNC CPU Modules ...
Page 115: ...5 Connecting and Setting up Multiple CNC CPU Modules MITSUBISHI CNC 98 ...
Page 116: ...99 6 Setting Machine Parameters ...
Page 130: ...113 7 Setting the Position Detection System ...
Page 153: ...7 Setting the Position Detection System MITSUBISHI CNC 136 ...
Page 154: ...137 8 Deceleration Check ...
Page 159: ...8 Deceleration Check MITSUBISHI CNC 142 ...
Page 160: ...143 9 Setting the Tool Entry Prohibited Range ...
Page 169: ...9 Setting the Tool Entry Prohibited Range MITSUBISHI CNC 152 ...
Page 170: ...153 10 Data Backup and Restoration ...
Page 184: ...167 Appendix 1 Explanation of Parameters ...
Page 435: ...Appendix 1 Explanation of Parameters MITSUBISHI CNC 418 ...
Page 436: ...419 Appendix 2 Explanation of Alarms ...
Page 608: ...591 Appendix 3 Display on 7 segment LED ...
Page 624: ......
Page 628: ......