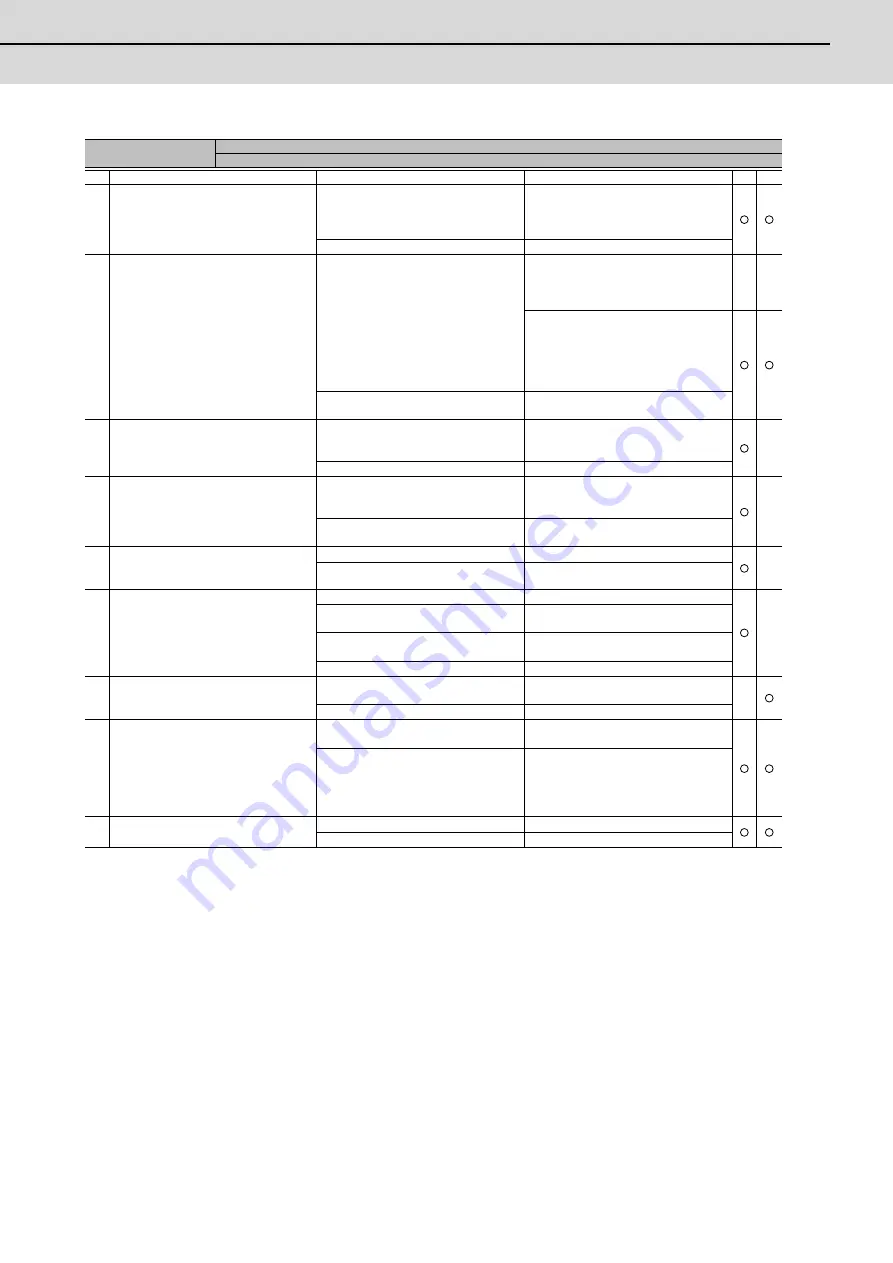
C70 Setup Manual
Appendix 2.16 Troubleshooting
573
(Note)
NR and PR resetting are not possible when the overload level is 50% or more. Do not forcibly reset (AR) by turning
the unit power OFF. If AR resetting is used at 50% or higher, the level is set to 80% when the power is turned ON
next. (Servo)
Alarm No.
50
Overload 1
Overload detection level became over 100%. The motor or the drive unit is overloaded.
Investigation details
Investigation results
Remedies
SV
SP
1
Check the overload parameters.
Servo:SV021, SV022
Spindle:SP021,SP022
The standard values (below) are not set.
Servo:SV021 = 60, SV022 = 150
Spindle:SP021=60,SP022=120
IPM:SP021=300,SP022=100
Set the standard values.
The standard values are set.
Investigate item 2.
2
Check the items below displayed on the
drive monitor screen during operation.
<Servo>
Max.current 3 (%)
Overload(%)
<Spindle>
Load meter(%)
Perform the machining such as rapid
traverse, where an alarm occurs. The
examples are below.
<Servo>
[1] Max.current 3 constantly displays the
maximum value.
[2] Overload increases at a rapid speed.
<Spindle>
[1] The time to display 120% lasts long.
[2] The value is higher than normal.
Servo
[1] Mount a smaller workpiece.
[2] Increase the time constant.
[3] Check the investigation item No.6.
Spindle
[1] Lower the cutting amount.
[2] Extend the cycle time.
The value is within the supposed level and
there is no problem.
Investigate item 3.
3
Check whether machine resonance is
occurring.
Check for vibration and abnormal noise at
the spindle and table.
Resonance is occurring when a tool or
workpiece is mounted or during machining.
(The load inertia changes)
Adjust the parameters.
[1] Set the optimal notch filter.
[2] Lower VGN1 (SV005,SP005).
Resonance is not occurring.
Investigate item 4.
4
Check whether the shaft sways when the
motor is stopped.
"Hunting" of the spindle
"Vibration" of the table
The motor is hunting.
Adjust the parameters.
[1] Increase VGN1 (SV005, SP005).
[2] Lower VIA (SV008, SP008).
The motor is not hunting.
Servo: Investigate item 5
Spindle: Investigate item 7
5
Check the brake operation.
[1] Check the brake relay.
[2] Check the connector (CN20) connection.
The motor brakes are not released.
Correct the faulty section.
The motor brake operation is normal.
Investigate item 6.
6
Check the load current with the NC Servo
Monitor, and investigate the machine load.
The cutting load is large.
Lower the cutting load.
There is interference with the positioning
pin.
When using the positioning pin, turn the
servo OFF when stopped.
An excessive force is applied from the
machine.
Check whether the ball screw is bent, or
whether there is a fault in the guide.
The machine load is not large.
Investigate item 8.
7
Check the PLG output waveform.
TS5690 cannot be checked.
There is a problem.
Adjust the PLG output waveform.
For TS5690, reinstall.
Normal
Investigate item 8.
8
Confirm the motor capacity selection again.
The motor performance is insufficient.
Lower the acceleration/deceleration rate or
cutting load.
The motor performance is sufficient.
Check the tool mounted on the spindle.
- The service life is reached.
Increase the number of teeth (chips) of the
milling cutter, etc.
Investigate item 9.
9
Try replacing the drive unit.
Improved.
Use as it is.
Not improved.
Replace the motor.
Summary of Contents for C70
Page 1: ......
Page 3: ......
Page 9: ......
Page 11: ......
Page 13: ......
Page 18: ...1 1 Outline ...
Page 21: ...1 Outline MITSUBISHI CNC 4 ...
Page 22: ...5 2 GOT Initial Setup ...
Page 73: ...2 GOT Initial Setup MITSUBISHI CNC 56 ...
Page 74: ...57 3 PLC CPU Initial Setup ...
Page 91: ...3 PLC CPU Initial Setup MITSUBISHI CNC 74 ...
Page 92: ...75 4 CNC CPU Initial Setup ...
Page 105: ...4 CNC CPU Initial Setup MITSUBISHI CNC 88 ...
Page 106: ...89 5 Connecting and Setting up Multiple CNC CPU Modules ...
Page 115: ...5 Connecting and Setting up Multiple CNC CPU Modules MITSUBISHI CNC 98 ...
Page 116: ...99 6 Setting Machine Parameters ...
Page 130: ...113 7 Setting the Position Detection System ...
Page 153: ...7 Setting the Position Detection System MITSUBISHI CNC 136 ...
Page 154: ...137 8 Deceleration Check ...
Page 159: ...8 Deceleration Check MITSUBISHI CNC 142 ...
Page 160: ...143 9 Setting the Tool Entry Prohibited Range ...
Page 169: ...9 Setting the Tool Entry Prohibited Range MITSUBISHI CNC 152 ...
Page 170: ...153 10 Data Backup and Restoration ...
Page 184: ...167 Appendix 1 Explanation of Parameters ...
Page 435: ...Appendix 1 Explanation of Parameters MITSUBISHI CNC 418 ...
Page 436: ...419 Appendix 2 Explanation of Alarms ...
Page 608: ...591 Appendix 3 Display on 7 segment LED ...
Page 624: ......
Page 628: ......