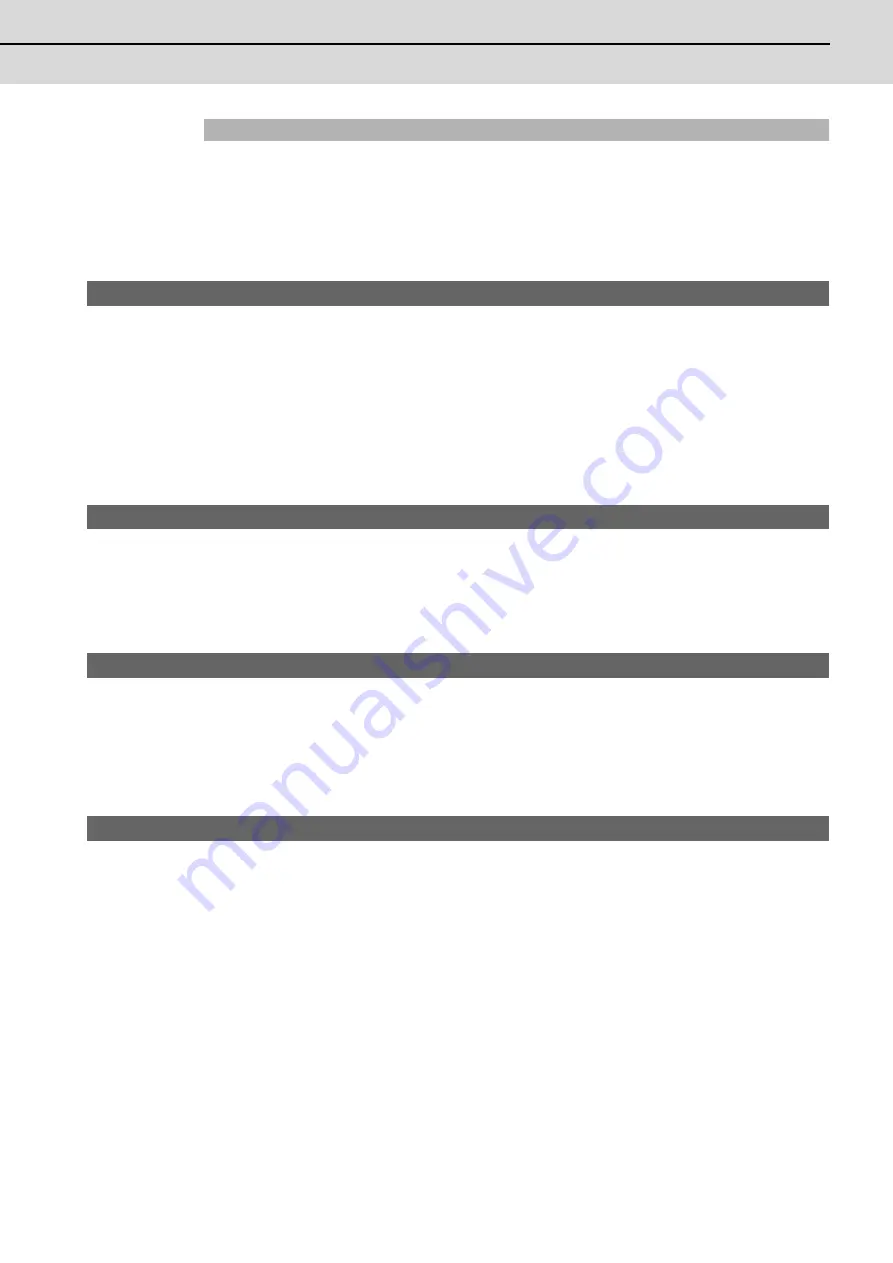
C70 Setup Manual
Appendix 1.5 Servo Parameters
259
bit 1-0 : vcnt Speed loop delay compensation changeover type selection
Normally, use "Changeover type 2".
bit1,0=
00: Disable
01: Changeover type 1
10: Changeover type 2
11: Setting prohibited
Related parameters: SV007
【
#2228(PR)
】
SV028 MSFT Magnetic pole shift amount (for linear/direct-drive motor)
Set this parameter to adjust the motor magnetic pole position and encoder's installation phase when
using linear motors or direct-drive motors.
During the DC excitation of the initial setup (SV034/bit4=1), set the same value displayed in "AFLT
gain" on the NC monitor screen.
Related parameters: SV034/bit4, SV061, SV062, SV063
For general motor:
Not used. Set to "0".
---Setting range---
-18000 to 18000 (Mechanical angle 0.01°)
【
#2229
】
SV029 VCS Speed at the change of speed loop gain
Noise at high speed rotation including rapid traverse can be reduced by lowering the speed loop gain
at high speeds.
Set the speed at which the speed loop gain changes. Use this with SV006 (VGN2).
When not using, set to "0".
---Setting range---
0 to 9999 (r/min)
【
#2230
】
SV030 IVC Voltage non-sensitive band compensation
When 100% is set, the voltage reduction amount equivalent to the logical non-energization in the
PWM control will be compensated.
When "0" is set, 100% compensation will be performed.
Adjust in increments of 10% from the default value of 100%.
If increased too much, vibration or vibration noise may be generated.
---Setting range---
0 to 255 (%)
【
#2231
】
SV031 OVS1 Overshooting compensation 1
This compensates the motor torque when overshooting occurs during positioning. This is valid only
when the overshooting compensation (SV027/bitB,A) is selected.
Type 3 SV027/bitB,A=11
Set the compensation amount based on the motor stall current. Observing positioning droop
waveform, increase in increments of 1% and find the value where overshooting does not occur.
To vary compensation amount depending on the direction.
When SV042 (OVS2) is "0", change the SV031 (OVS1) value in both of the +/- directions to
compensate.
To vary the compensation amount depending on the command direction, set this and SV042
(OVS2).
(SV031: + direction, SV042: - direction. However, the directions may be opposite depending on
other settings.)
When "-1" is set, the compensation will not be performed in the direction of the command.
Related parameters: SV027/bitB,A, SV034/bitF-C, SV042, SV082/bit2
---Setting range---
-1 to 100 (Stall current %)
Note that the range will be "-1 - 10000" (Stall current 0.01%) when SV082/bit2 is "1".
Summary of Contents for C70
Page 1: ......
Page 3: ......
Page 9: ......
Page 11: ......
Page 13: ......
Page 18: ...1 1 Outline ...
Page 21: ...1 Outline MITSUBISHI CNC 4 ...
Page 22: ...5 2 GOT Initial Setup ...
Page 73: ...2 GOT Initial Setup MITSUBISHI CNC 56 ...
Page 74: ...57 3 PLC CPU Initial Setup ...
Page 91: ...3 PLC CPU Initial Setup MITSUBISHI CNC 74 ...
Page 92: ...75 4 CNC CPU Initial Setup ...
Page 105: ...4 CNC CPU Initial Setup MITSUBISHI CNC 88 ...
Page 106: ...89 5 Connecting and Setting up Multiple CNC CPU Modules ...
Page 115: ...5 Connecting and Setting up Multiple CNC CPU Modules MITSUBISHI CNC 98 ...
Page 116: ...99 6 Setting Machine Parameters ...
Page 130: ...113 7 Setting the Position Detection System ...
Page 153: ...7 Setting the Position Detection System MITSUBISHI CNC 136 ...
Page 154: ...137 8 Deceleration Check ...
Page 159: ...8 Deceleration Check MITSUBISHI CNC 142 ...
Page 160: ...143 9 Setting the Tool Entry Prohibited Range ...
Page 169: ...9 Setting the Tool Entry Prohibited Range MITSUBISHI CNC 152 ...
Page 170: ...153 10 Data Backup and Restoration ...
Page 184: ...167 Appendix 1 Explanation of Parameters ...
Page 435: ...Appendix 1 Explanation of Parameters MITSUBISHI CNC 418 ...
Page 436: ...419 Appendix 2 Explanation of Alarms ...
Page 608: ...591 Appendix 3 Display on 7 segment LED ...
Page 624: ......
Page 628: ......