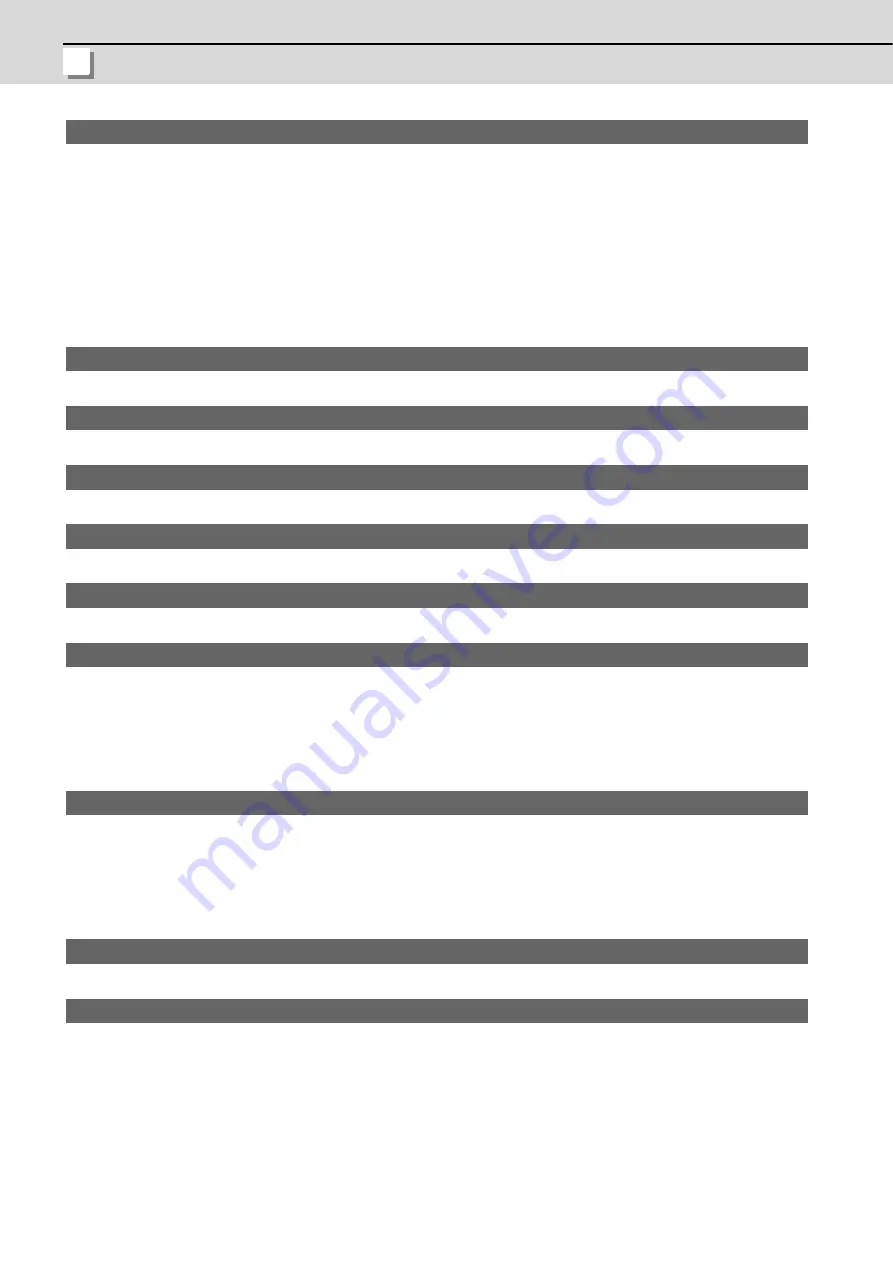
Appendix 1 Explanation of Parameters
MITSUBISHI CNC
276
【
#2295
】
SV095 ZUPD Vertical axis pull up distance
Set this parameter to adjust the pull up distance when the vertical axis pull up function is enabled.
When the pull up function is enabled and this parameter is set to "0", for a rotary motor, 8/1000 of a
rotation at the motor end is internally set as the pull up distance, and for a linear motor, 80[
μ
m] is
set.
Related parameters:
SV032 : The pull up direction is determined. When "0" is set, pull up control is not executed.
SV033/bitE : Start-up of the pull up function
SV048 : Set the drop prevention time. When "0" is set, pull up control is not executed.
---Setting range---
0 to 2000 (
μ
m)
【
#2296
】
SV096
Not used. Set to "0".
【
#2297
】
SV097
Not used. Set to "0".
【
#2298
】
SV098
Not used. Set to "0".
【
#2299
】
SV099
Not used. Set to "0".
【
#2300
】
SV100
Not used. Set to "0".
【
#2301
】
SV101 TMA1 OMR-FF movement averaging filter time constant 1
Set the movement averaging filter time constant in OMR-FF control.
The standard setting is "88".
Set to "0" when not using OMR-FF control.
---Setting range---
0 to 711 (0.01ms)
【
#2302
】
SV102 TMA2 OMR-FF movement averaging filter time constant 2
Set the movement averaging filter time constant in OMR-FF control.
The standard setting is "88".
Set to "0" when not using OMR-FF control.
---Setting range---
0 to 711 (0.01ms)
【
#2303
】
SV103
Not used. Set to "0".
【
#2304
】
SV104 FFR0 OMR-FF inner rounding compensation gain for G0
Set the inner rounding compensation amount (drive side feed forward gain) in OMR-FF control.
When a shape tracking error is too large in OMR-FF control, adjust it by setting this parameter.
The higher the setting value is, the less the shape tracking error will be, however, overshooting
during acceleration/deceleration will increase.
Lower the value when vibration occurs during the G0 acceleration/deceleration.
The standard setting is "10000".
Set to "0" when not using OMR-FF control.
---Setting range---
0 to 20000 (0.01%)
Summary of Contents for C70
Page 1: ......
Page 3: ......
Page 9: ......
Page 11: ......
Page 13: ......
Page 18: ...1 1 Outline ...
Page 21: ...1 Outline MITSUBISHI CNC 4 ...
Page 22: ...5 2 GOT Initial Setup ...
Page 73: ...2 GOT Initial Setup MITSUBISHI CNC 56 ...
Page 74: ...57 3 PLC CPU Initial Setup ...
Page 91: ...3 PLC CPU Initial Setup MITSUBISHI CNC 74 ...
Page 92: ...75 4 CNC CPU Initial Setup ...
Page 105: ...4 CNC CPU Initial Setup MITSUBISHI CNC 88 ...
Page 106: ...89 5 Connecting and Setting up Multiple CNC CPU Modules ...
Page 115: ...5 Connecting and Setting up Multiple CNC CPU Modules MITSUBISHI CNC 98 ...
Page 116: ...99 6 Setting Machine Parameters ...
Page 130: ...113 7 Setting the Position Detection System ...
Page 153: ...7 Setting the Position Detection System MITSUBISHI CNC 136 ...
Page 154: ...137 8 Deceleration Check ...
Page 159: ...8 Deceleration Check MITSUBISHI CNC 142 ...
Page 160: ...143 9 Setting the Tool Entry Prohibited Range ...
Page 169: ...9 Setting the Tool Entry Prohibited Range MITSUBISHI CNC 152 ...
Page 170: ...153 10 Data Backup and Restoration ...
Page 184: ...167 Appendix 1 Explanation of Parameters ...
Page 435: ...Appendix 1 Explanation of Parameters MITSUBISHI CNC 418 ...
Page 436: ...419 Appendix 2 Explanation of Alarms ...
Page 608: ...591 Appendix 3 Display on 7 segment LED ...
Page 624: ......
Page 628: ......