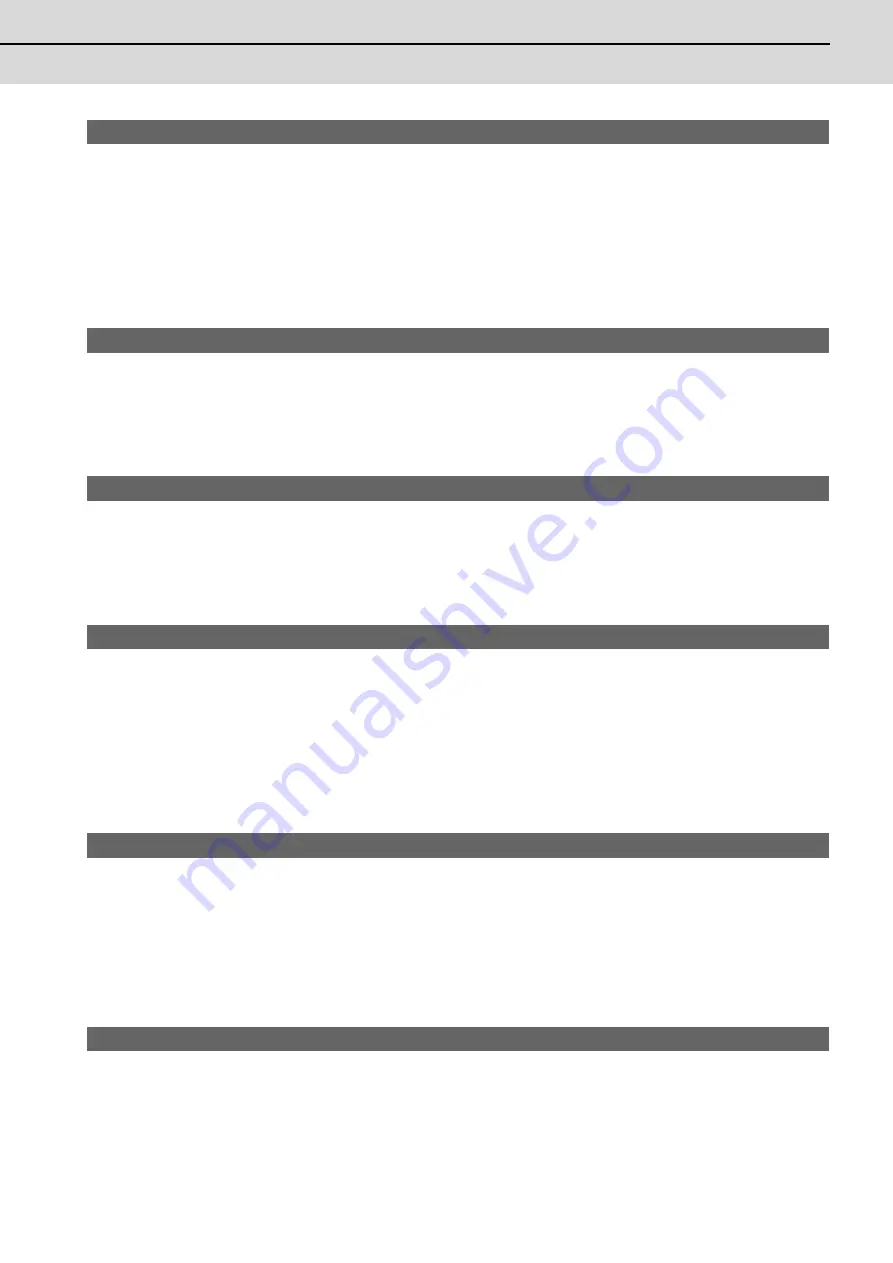
C70 Setup Manual
Appendix 1.6 Spindle Parameters
315
【
#13051
】
SP051 DFBT Dual feed back control time constant
Set the control time constant in dual feed back.
When the function is valid, the standard setting is "100". When "0" is set, the value is 1 ms.
When the time constant is increased, the operation will get closer to the semi-closed control and the
limit of the position loop gain will be raised.
However, this cannot be used when the spindle slip occurs in machine configuration such as V-belt
drive.
Related parameters: SP017/bit1, SP052
---Setting range---
0 to 9999 (ms)
【
#13052
】
SP052 DFBN Dual feedback control non-sensitive band
Set the non-sensitive band in the dual feedback control.
Normally set to "0".
Related parameters: SP017/bit1, SP051
---Setting range---
0 to 9999 (1/1000°)
【
#13053
】
SP053 ODS Excessive error detection width (non-interpolation mode)
Set the excessive error detection width in non-interpolation mode.
Standard setting value: ODS = Maximum motor speed [r/min] × 6/PGV/2
When set to "0", the excessive error detection will not be performed.
---Setting range---
0 to 32767 (°)
【
#13054
】
SP054 ORE Overrun detection width in closed loop control
Set the overrun detection width in the full-closed loop control.
When the gap between the motor side encoder and the machine side encoder exceeds the set
value, it is judged as an overrun and "Alarm 43" is detected.
When "-1" is set, if the differential velocity between the motor side encoder and the machine side
encoder exceeds the 30% of the maximum motor speed, it will be judged as overrun and "Alarm 43"
will be detected.
When "0" is set, overrun will be detected with 2°.
In the full-closed loop control, normally set this parameter to "360". During V-belt drive, set to "-1".
---Setting range---
-1 to 32767 (°)
【
#13055
】
SP055 EMGx Max. gate off delay time after emergency stop
Set the time required to forcibly execute READY OFF after the emergency stop is input.
Normally set to "20000".
When "0" is set, READY OFF is forcibly executed with "7000ms".
When the set time is shorter than the time to decelerate and stop, the spindle will stop with the
dynamic brake after the set time is out.
Related parameters: SP056
---Setting range---
0 to 29900 (ms)
【
#13056
】
SP056 EMGt Deceleration time constant at emergency stop
Set the time constant used for the deceleration control at emergency stop. Set the time required to
stop from the maximum motor speed (TSP).
When "0" is set, the deceleration control is executed with "7000ms".
Related parameters: SP055
---Setting range---
0 to 29900 (ms)
Summary of Contents for C70
Page 1: ......
Page 3: ......
Page 9: ......
Page 11: ......
Page 13: ......
Page 18: ...1 1 Outline ...
Page 21: ...1 Outline MITSUBISHI CNC 4 ...
Page 22: ...5 2 GOT Initial Setup ...
Page 73: ...2 GOT Initial Setup MITSUBISHI CNC 56 ...
Page 74: ...57 3 PLC CPU Initial Setup ...
Page 91: ...3 PLC CPU Initial Setup MITSUBISHI CNC 74 ...
Page 92: ...75 4 CNC CPU Initial Setup ...
Page 105: ...4 CNC CPU Initial Setup MITSUBISHI CNC 88 ...
Page 106: ...89 5 Connecting and Setting up Multiple CNC CPU Modules ...
Page 115: ...5 Connecting and Setting up Multiple CNC CPU Modules MITSUBISHI CNC 98 ...
Page 116: ...99 6 Setting Machine Parameters ...
Page 130: ...113 7 Setting the Position Detection System ...
Page 153: ...7 Setting the Position Detection System MITSUBISHI CNC 136 ...
Page 154: ...137 8 Deceleration Check ...
Page 159: ...8 Deceleration Check MITSUBISHI CNC 142 ...
Page 160: ...143 9 Setting the Tool Entry Prohibited Range ...
Page 169: ...9 Setting the Tool Entry Prohibited Range MITSUBISHI CNC 152 ...
Page 170: ...153 10 Data Backup and Restoration ...
Page 184: ...167 Appendix 1 Explanation of Parameters ...
Page 435: ...Appendix 1 Explanation of Parameters MITSUBISHI CNC 418 ...
Page 436: ...419 Appendix 2 Explanation of Alarms ...
Page 608: ...591 Appendix 3 Display on 7 segment LED ...
Page 624: ......
Page 628: ......