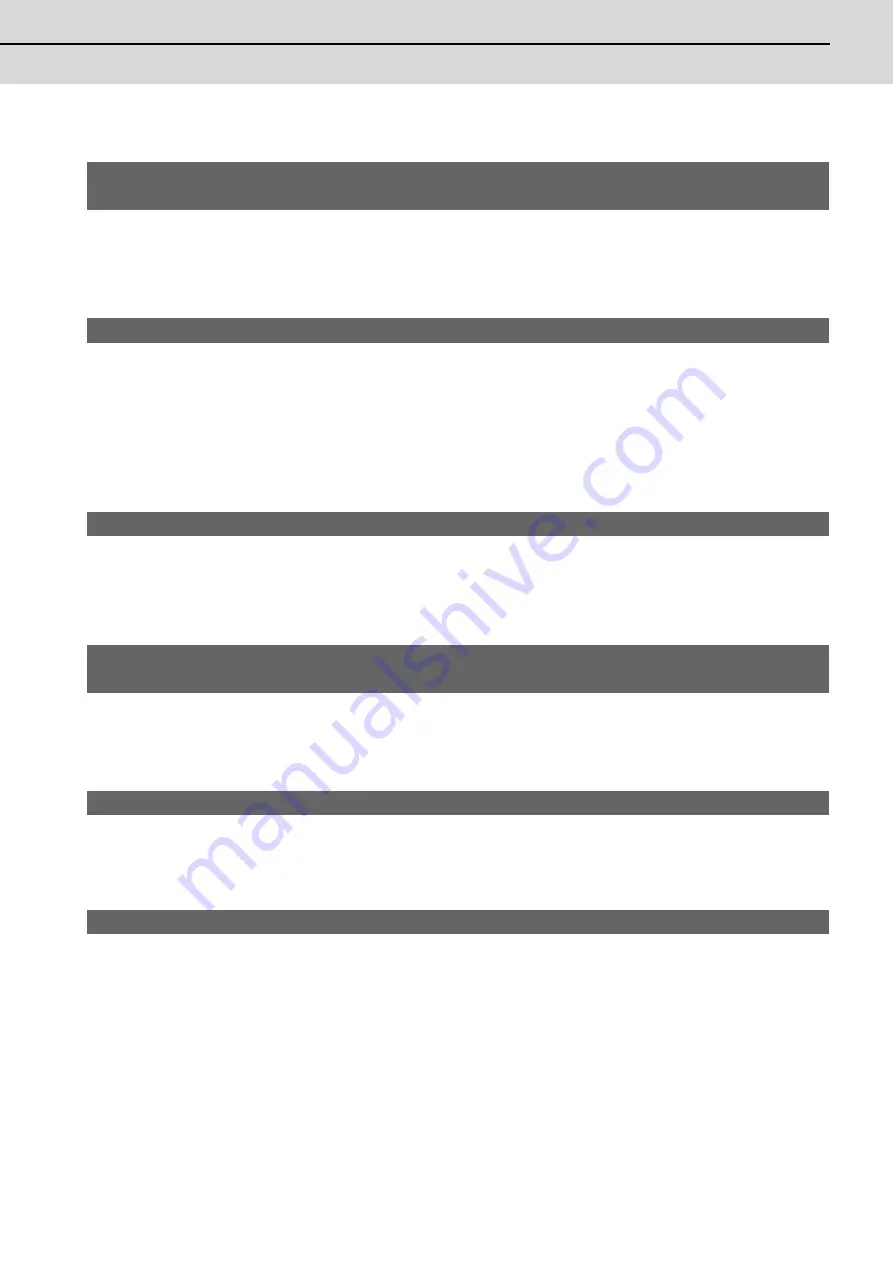
C70 Setup Manual
Appendix 1.7 Multi-CPU Parameters
341
Appendix 1.7 Multi-CPU Parameters
【
#26701, 26711, 26721, 26731(PR)
】
CPU specific send range(K) Cyclic transmission area
size
Set the size of the cyclic transmission area to be allocated to each CPU module configuring the
multi-CPU system. The area size for NC CPU should be 3 [K points].
---Setting range---
0 to 15 (K points)
(Count the number of points by word)
【
#26702, 26712, 26722, 26732(PR)
】
auto refresh area size Automatic refresh area size
Set the size of the automatic refresh area to be allocated to each CPU module configuring the multi-
CPU system.
Set to "0" for NC CPU, as this CPU does not use the automatic refresh.
If any other CPU uses the automatic refresh, however, you need to set this parameter for such CPU.
If you set a value other than “0” for NC CPU, a self diagnosis error occurs when the power is turned
OFF and ON.
---Setting range---
0 to 14335 (points)
(Count the number of points by word)
【
#26703, 26713, 26723, 26733(PR)
】
Restricted system area(K) System area size
Set the size of the system area to be allocated to each CPU module.
The area size for NC CPU should be 1 [K points].
(Default size of system area is 1K points.)
---Setting range---
0 to 2 (K points)
【
#26704, 26714, 26724, 26734(PR)
】
Unsynchronize CPU boot-up Unsynchronize Multi-CPU
boot-ups
Select whether to synchronize the multi-CPU boot-ups.
0 : Synchronize
1 : Unsynchronize
(Note) Make sure that the value "0" means "synchronize", which is contrary to the setting in GX
Works2 / GX Developer.
【
#26741(PR)
】
Command Slot No. Control signal input slot No.
Set the slot No. of the PLC CPU module to which the control signals are input.
0: CPU slot
1: Slot 0
2: Slot 1
3: Slot 2
【
#26742(PR)
】
G Device TOP number Control signal input device No.
Set the No. of the head device in shared memory to which the control signals are input.
When the setting value is less than 10000, it will be handled as 10000.
---Setting range---
10000 to 16144
* Set this within the setting range of the target CPU's shared memory.
Summary of Contents for C70
Page 1: ......
Page 3: ......
Page 9: ......
Page 11: ......
Page 13: ......
Page 18: ...1 1 Outline ...
Page 21: ...1 Outline MITSUBISHI CNC 4 ...
Page 22: ...5 2 GOT Initial Setup ...
Page 73: ...2 GOT Initial Setup MITSUBISHI CNC 56 ...
Page 74: ...57 3 PLC CPU Initial Setup ...
Page 91: ...3 PLC CPU Initial Setup MITSUBISHI CNC 74 ...
Page 92: ...75 4 CNC CPU Initial Setup ...
Page 105: ...4 CNC CPU Initial Setup MITSUBISHI CNC 88 ...
Page 106: ...89 5 Connecting and Setting up Multiple CNC CPU Modules ...
Page 115: ...5 Connecting and Setting up Multiple CNC CPU Modules MITSUBISHI CNC 98 ...
Page 116: ...99 6 Setting Machine Parameters ...
Page 130: ...113 7 Setting the Position Detection System ...
Page 153: ...7 Setting the Position Detection System MITSUBISHI CNC 136 ...
Page 154: ...137 8 Deceleration Check ...
Page 159: ...8 Deceleration Check MITSUBISHI CNC 142 ...
Page 160: ...143 9 Setting the Tool Entry Prohibited Range ...
Page 169: ...9 Setting the Tool Entry Prohibited Range MITSUBISHI CNC 152 ...
Page 170: ...153 10 Data Backup and Restoration ...
Page 184: ...167 Appendix 1 Explanation of Parameters ...
Page 435: ...Appendix 1 Explanation of Parameters MITSUBISHI CNC 418 ...
Page 436: ...419 Appendix 2 Explanation of Alarms ...
Page 608: ...591 Appendix 3 Display on 7 segment LED ...
Page 624: ......
Page 628: ......