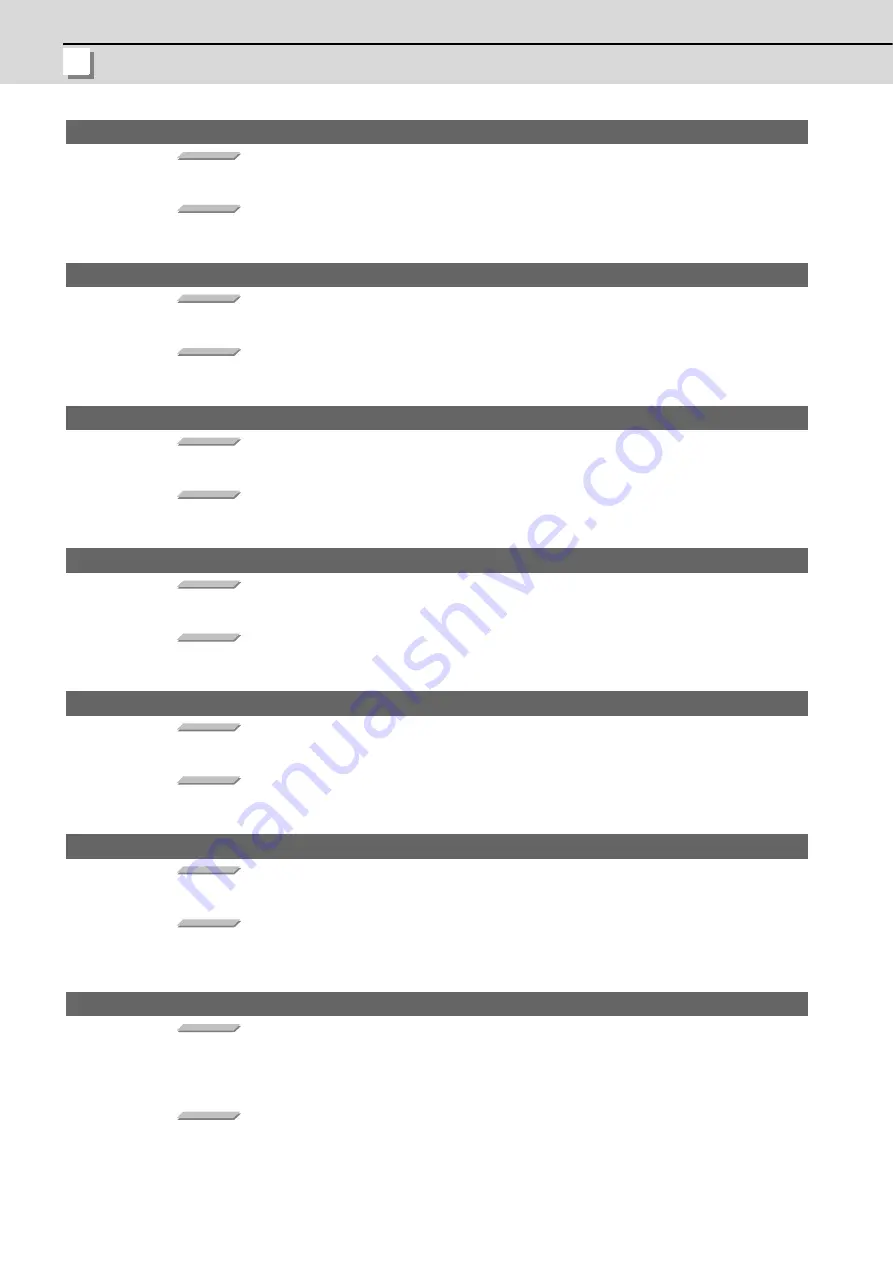
Appendix 2 Explanation of Alarms
MITSUBISHI CNC
510
A01 MULTI CPU ERROR 4352
Details
- An incorrect number of devices were designated with the exclusive instruction for multi-CPUs high-
speed communication set in the program.
Remedy
- Read the common information of the error using a programming tool, check error step corresponding
to its numerical value (program error location), and correct the problem.
A01 MULTI CPU ERROR 4353
Details
- An unusable device was designated with the exclusive instruction for multi-CPUs high-speed
communication set in the program.
Remedy
- Read the common information of the error using a programming tool, check error step corresponding
to its numerical value (program error location), and correct the problem.
A01 MULTI CPU ERROR 4354
Details
- An unusable character string was designated with the exclusive instruction for multi-CPUs high-
speed communication set in the program.
Remedy
- Read the common information of the error using a programming tool, check error step corresponding
to its numerical value (program error location), and correct the problem.
A01 MULTI CPU ERROR 4355
Details
- An invalid number of read/write data (number of request/response data) was designated with the
exclusive instruction for multi-CPUs high-speed communication set in the program.
Remedy
- Read the common information of the error using a programming tool, check error step corresponding
to its numerical value (program error location), and correct the problem.
A01 MULTI CPU ERROR 5000
Details
- The scan time of the initial execution type program exceeded the initial execution watch time
specified in the PLC RAS setting of the PLC parameter dialog box.
Remedy
- Read the individual information of the error with a programming tool, check its value (time), and
shorten the scan time.
A01 MULTI CPU ERROR 5001
Details
- The program scan time exceeded the WDT value specified in the PLC RAS setting of the PLC
parameter dialog box.
Remedy
- Read the individual information of the error with a programming tool, check its value (time), and
shorten the scan time.
- Resolve the endless loop caused by jump transition.
A01 MULTI CPU ERROR 5010
Details
- The program scan time exceeded the constant scan time specified in the PLC RAS setting of the
PLC parameter dialog box.
- The low speed program execution time specified in the PLC RAS setting of the PLC parameter
dialog box exceeded the excess time of the constant scan.
Remedy
- Review the constant scan setting time.
- Review the constant scan time and low speed program execution time in the PLC parameter so that
the margin time of constant scan may be fully reserved.
Summary of Contents for C70
Page 1: ......
Page 3: ......
Page 9: ......
Page 11: ......
Page 13: ......
Page 18: ...1 1 Outline ...
Page 21: ...1 Outline MITSUBISHI CNC 4 ...
Page 22: ...5 2 GOT Initial Setup ...
Page 73: ...2 GOT Initial Setup MITSUBISHI CNC 56 ...
Page 74: ...57 3 PLC CPU Initial Setup ...
Page 91: ...3 PLC CPU Initial Setup MITSUBISHI CNC 74 ...
Page 92: ...75 4 CNC CPU Initial Setup ...
Page 105: ...4 CNC CPU Initial Setup MITSUBISHI CNC 88 ...
Page 106: ...89 5 Connecting and Setting up Multiple CNC CPU Modules ...
Page 115: ...5 Connecting and Setting up Multiple CNC CPU Modules MITSUBISHI CNC 98 ...
Page 116: ...99 6 Setting Machine Parameters ...
Page 130: ...113 7 Setting the Position Detection System ...
Page 153: ...7 Setting the Position Detection System MITSUBISHI CNC 136 ...
Page 154: ...137 8 Deceleration Check ...
Page 159: ...8 Deceleration Check MITSUBISHI CNC 142 ...
Page 160: ...143 9 Setting the Tool Entry Prohibited Range ...
Page 169: ...9 Setting the Tool Entry Prohibited Range MITSUBISHI CNC 152 ...
Page 170: ...153 10 Data Backup and Restoration ...
Page 184: ...167 Appendix 1 Explanation of Parameters ...
Page 435: ...Appendix 1 Explanation of Parameters MITSUBISHI CNC 418 ...
Page 436: ...419 Appendix 2 Explanation of Alarms ...
Page 608: ...591 Appendix 3 Display on 7 segment LED ...
Page 624: ......
Page 628: ......