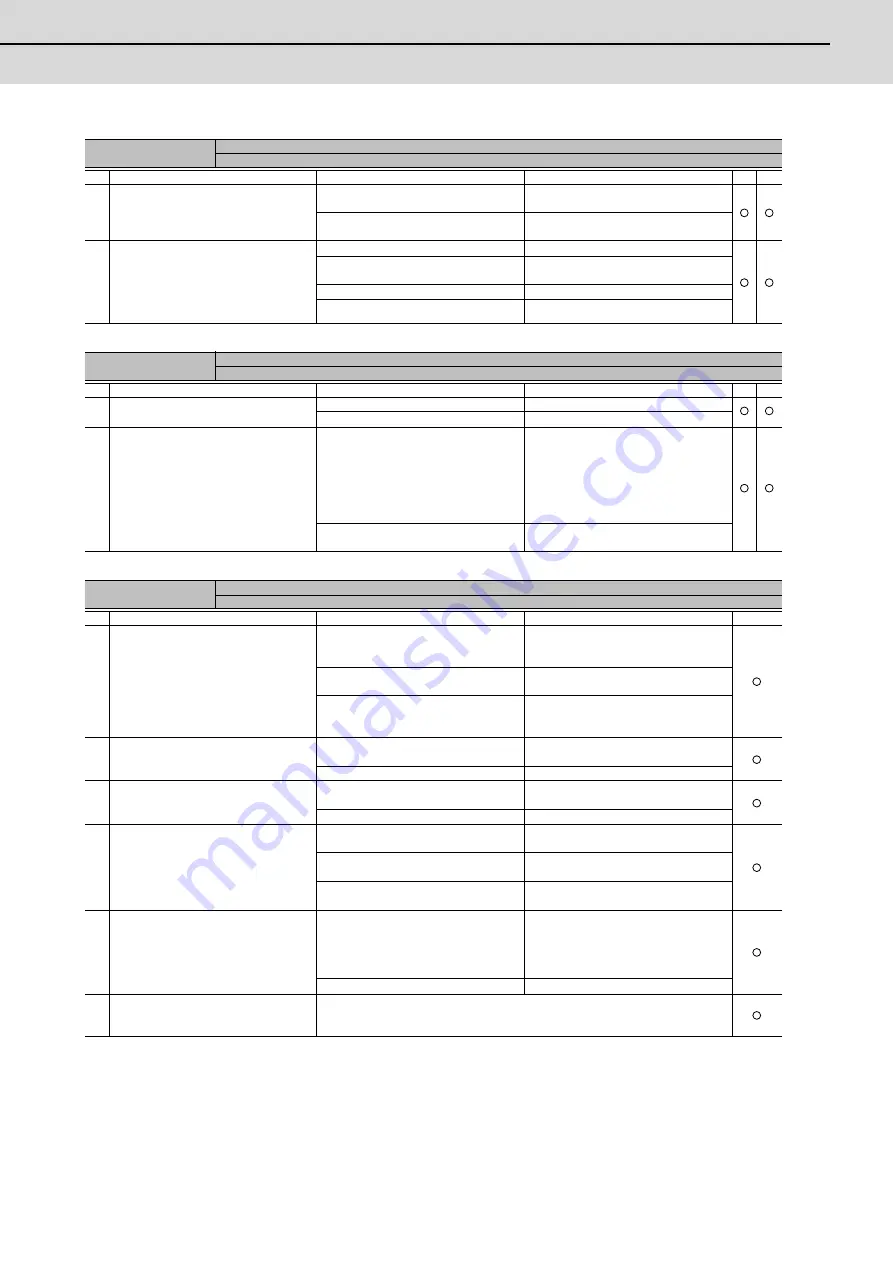
C70 Setup Manual
Appendix 2.16 Troubleshooting
577
Alarm No.
5E
Safety observation: Feedback speed error
In safety monitoring mode, the motor speed was detected to exceed the safe speed.
Investigation details
Investigation results
Remedies
SV
SP
1
Check the DI input timing.
The feedback speed and safe speed limit
value are the same.
Reduce the commanded speed on the NC
side or increase the safe speed limit value.
The feedback speed is slower than the safe
speed.
Replace the drive unit.
2
Check the wiring and setting environment.
1) Correctly grounded?
2) Any noise generating devices around the
unit?
3) Are the speed/position detector cables
correctly shielded?
1) The grounding is incomplete.
Correctly ground.
2) The alarm occurs easily when a specific
device operates.
Use noise measures on the device
described on the left.
3) The cable is not correctly shielded.
Correctly shield the cable.
No abnormality is found in particular.
Replace the drive unit.
Alarm No.
5F
External contactor error
A contact of the external contactor is welding.
Investigation details
Investigation results
Remedies
SV
SP
1
Check whether the contactor's contact has
melted.
The contactor is melted.
Replace the contactor.
The contactor is not melted.
Check the investigation item No. 2.
2
Check whether the axis where an alarm
occurred was a contactor control axis.
The alarm occurred at the axis where the
contactor control is not executed.
Check the parameter.(SVJ3/SPJ3)
With contactor control
Servo:SV082, Spindle:SP227
0800h is added to the setting value.
Without contactor control
Change "Bit A,B" to "00" in the parameter
above.
The alarm occurred at the axis where the
contactor control is executed.
Replace the drive unit.
Alarm No.
61
Power supply: Power module overcurrent
Overcurrent protection function in the power module of power supply has started its operation.
Investigation details
Investigation results
Remedies
CV
1
Check the state of the operation when the
alarm occurs, and check the repeatability.
The alarm occurs immediately after
200VAC is supplied or after READY is
turned ON.
Replace the unit.
The alarm occurs occasionally during
READY ON.
Check the investigation item No. 3.
The alarm occurs after continuous operation
for a long time.
The unit is hot.
Check the investigation item No. 2.
2
Check the load state of all motors (during
stopped).
The total load of all motors exceeds the
rated capacity of the power supply unit.
Lower the motor load and operation
frequency.
The total does not exceed the capacity.
Check the investigation item No. 3.
3
Check the power capacity of the facility.
Check the capacity of the step-down
transformer (KVA).
The power capacity of the facility is
insufficient.
Increase the power capacity of the facility.
The specified power capacity is secured.
Check the investigation item No. 4.
4
Measure the voltage across wires.
Is the voltage 170V or more even when the
motor is accelerating?
The voltage drops to 170V or less
occasionally.
Increase the power capacity of the facility.
The difference of the voltage across wires is
10V or more.
Improve the power phase balance.
The difference of the voltage across wires is
less than 10V.
Check the investigation item No. 5.
5
Check whether there is any device
(machine) causing the power distortion.
Abnormal noise is heard from an AC reactor
when stopping at the servo ON.
Improve the source of the distortion.
For example, when abnormal noise is heard
from another machine that is in operation,
move the wiring to the power which is far
from the machine's power supply.
Abnormal noise is not heard.
Check the investigation item No. 6.
6
Check if there is any abnormality in the
unit's ambient environment.
(Ex. Noise, grounding, etc.)
Take remedies according to the causes of the abnormality in the ambient environment.
Summary of Contents for C70
Page 1: ......
Page 3: ......
Page 9: ......
Page 11: ......
Page 13: ......
Page 18: ...1 1 Outline ...
Page 21: ...1 Outline MITSUBISHI CNC 4 ...
Page 22: ...5 2 GOT Initial Setup ...
Page 73: ...2 GOT Initial Setup MITSUBISHI CNC 56 ...
Page 74: ...57 3 PLC CPU Initial Setup ...
Page 91: ...3 PLC CPU Initial Setup MITSUBISHI CNC 74 ...
Page 92: ...75 4 CNC CPU Initial Setup ...
Page 105: ...4 CNC CPU Initial Setup MITSUBISHI CNC 88 ...
Page 106: ...89 5 Connecting and Setting up Multiple CNC CPU Modules ...
Page 115: ...5 Connecting and Setting up Multiple CNC CPU Modules MITSUBISHI CNC 98 ...
Page 116: ...99 6 Setting Machine Parameters ...
Page 130: ...113 7 Setting the Position Detection System ...
Page 153: ...7 Setting the Position Detection System MITSUBISHI CNC 136 ...
Page 154: ...137 8 Deceleration Check ...
Page 159: ...8 Deceleration Check MITSUBISHI CNC 142 ...
Page 160: ...143 9 Setting the Tool Entry Prohibited Range ...
Page 169: ...9 Setting the Tool Entry Prohibited Range MITSUBISHI CNC 152 ...
Page 170: ...153 10 Data Backup and Restoration ...
Page 184: ...167 Appendix 1 Explanation of Parameters ...
Page 435: ...Appendix 1 Explanation of Parameters MITSUBISHI CNC 418 ...
Page 436: ...419 Appendix 2 Explanation of Alarms ...
Page 608: ...591 Appendix 3 Display on 7 segment LED ...
Page 624: ......
Page 628: ......