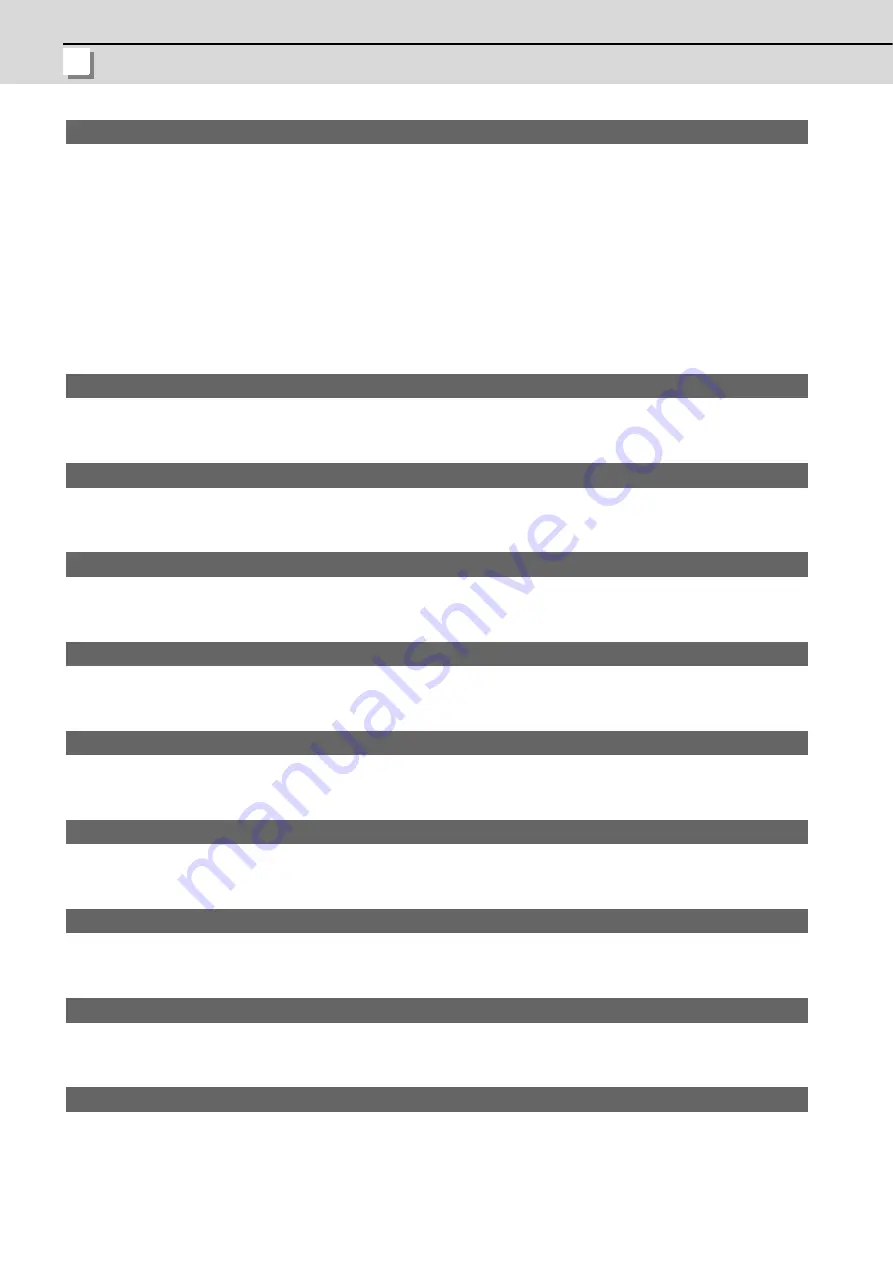
Appendix 1 Explanation of Parameters
MITSUBISHI CNC
196
【
#1193
】
inpos Validate in-position check
Select the manner of how to check deceleration when a positioning command is being issued.
0: Command deceleration check
(Positioning is completed when the deceleration is completed at the acceleration/deceleration
speed commanded from the control unit.)
1: In-position check
(Positioning is completed when the servo drive unit detects the machine having reached within
a set distance from the end point. This set distance is determined in "#2224 SV024".)
2: Command deceleration check (Commanded deceleration check is executed when cutting feed
is shifted to rapid traverse.)
3: In-position check (Commanded deceleration check is executed when cutting feed is shifted to
rapid traverse.)
For the details of each setting values, refer to "Deceleration Check" - "Deceleration Check and
Parameters".
【
#1194
】
H_acdc Time constant 0 for handle feed
Select the time constant for manual handle feed.
0: Use time constant for G01
1: Time constant 0 (step)
【
#1195
】
Mmac Macro call for M command
Select whether to enable or disable M command macro call of user macro.
0: Disable
1: Enable
【
#1196
】
Smac Macro call for S command
Select whether to enable or disable S command macro call of user macro.
0: Disable
1: Enable
【
#1197
】
Tmac Macro call for T command
Select whether to enable or disable T command macro call of user macro.
0: Disable
1: Enable
【
#1198
】
M2mac Macro call with 2nd miscellaneous code
Select whether to enable or disable 2nd miscellaneous command macro call of user macro.
0: Disable
1: Enable
【
#1199(PR)
】
Sselect Select initial spindle control
Select the initial condition of spindle control after power is turned ON.
0: 1st spindle control mode (G43.1)
1: 2nd spindle control mode (G44.1)
【
#1200(PR)
】
G0_acc Validate acceleration and deceleration with inclination constant G0
Select the acceleration and deceleration type when a rapid traverse command is issued.
0: Acceleration and deceleration with constant time (conventional type)
1: Acceleration and deceleration with a constant angle of inclination
【
#1201(PR)
】
G1_acc Validate acceleration and deceleration with inclination constant G1
Select the acceleration and deceleration type when a linear interpolation command is issued.
0: Acceleration and deceleration with constant time (conventional type)
1: Acceleration and deceleration with a constant angle of inclination
【
#1202
】
mirofs Distance between facing turrets (for L system only)
Set the distance between tools (edges) (between facing turrets).
---Setting range---
0 to 99999.999 (mm)
Summary of Contents for C70
Page 1: ......
Page 3: ......
Page 9: ......
Page 11: ......
Page 13: ......
Page 18: ...1 1 Outline ...
Page 21: ...1 Outline MITSUBISHI CNC 4 ...
Page 22: ...5 2 GOT Initial Setup ...
Page 73: ...2 GOT Initial Setup MITSUBISHI CNC 56 ...
Page 74: ...57 3 PLC CPU Initial Setup ...
Page 91: ...3 PLC CPU Initial Setup MITSUBISHI CNC 74 ...
Page 92: ...75 4 CNC CPU Initial Setup ...
Page 105: ...4 CNC CPU Initial Setup MITSUBISHI CNC 88 ...
Page 106: ...89 5 Connecting and Setting up Multiple CNC CPU Modules ...
Page 115: ...5 Connecting and Setting up Multiple CNC CPU Modules MITSUBISHI CNC 98 ...
Page 116: ...99 6 Setting Machine Parameters ...
Page 130: ...113 7 Setting the Position Detection System ...
Page 153: ...7 Setting the Position Detection System MITSUBISHI CNC 136 ...
Page 154: ...137 8 Deceleration Check ...
Page 159: ...8 Deceleration Check MITSUBISHI CNC 142 ...
Page 160: ...143 9 Setting the Tool Entry Prohibited Range ...
Page 169: ...9 Setting the Tool Entry Prohibited Range MITSUBISHI CNC 152 ...
Page 170: ...153 10 Data Backup and Restoration ...
Page 184: ...167 Appendix 1 Explanation of Parameters ...
Page 435: ...Appendix 1 Explanation of Parameters MITSUBISHI CNC 418 ...
Page 436: ...419 Appendix 2 Explanation of Alarms ...
Page 608: ...591 Appendix 3 Display on 7 segment LED ...
Page 624: ......
Page 628: ......